Seal Terminology 101: Getting Started in the World of Seals
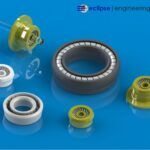
While the average person can probably recognize a rubber O-Ring , knowledge of advanced sealing devices remains a largely obscure field of knowledge. Eclipse is here to be the subject matter experts and guide you to the best sealing solution, but being familiar with some basic seal terminology will aid us in the process.
The ability to effectively communicate the operating conditions and goals of the sealing system will expedite the design and quoting process and ensure that we choose the optimal solution for you.
Below we’ll discuss some common terms and industry nomenclature to get you started in the world of seals.
O-Rings, Gaskets, Spring Seals, Cap Seals – What do I Call These Things?
Sometimes just finding what to call a particular seal can be a challenge in and of itself. We’ve had customers contact us looking for a new “O-Ring” or “gasket” when they actually have a PTFE Canted Coil Spring Energized Seal in front of them.
In many cases, terms like “O-Ring” are used to generically describe any kind of seal regardless of type or functionality.
Other customers who primarily work with metallic or ceramic sealing elements like piston rings or mechanical face seals, might refer to any other type of seal as a “soft seal,” even if it’s made from a highly filled PTFE. Another customer might request an “oil seal” even though their application is a dry-running rotary vacuum arrangement.
Eclipse understands just describing the seal needed can be a major barrier. That’s why we designed our standard part number catalogs to be graphically based to help with product recognition and description.
While the catalogs are meant to demonstrate Eclipse’s capabilities and standard part number schemes, they’re also great tools for communicating seal types and configurations.
Grooves and Glands
The physical space for a seal to occupy is often simply called a groove but can also be referred to as a gland. In most cases, it’s a rectangular groove cut into the hardware whether it be on a piston, in the housing for a rod, or in the face of two mating surfaces.
In contrast to O-Rings and elastomeric seals, PTFE and polymer seals are critically dependent on hardware conditions for proper functionality. Configuring the gland for proper seal installation and preparing the mating surfaces with the necessary finishes and hardness is necessary for successful sealing.
Diameters
OD – Outside Diameter
ID – Inside Diameter
Almost all the polymer seals we manufacture are round parts machined on CNC lathes. Therefore, the diameters are key dimensions for both the seal and mating hardware.
Diameter dimensions are proceeded by the symbol “ Ø ” on manufacturing prints. Many seal prints feature cross-sectional views where the diameters are not shown completely. This leads to some confusion about whether the radius or diameter is being called out.
A radius would be proceeded by the symbol “ R ” and would involve finding the theoretical center of a part to measure/inspect. Therefore, diameters are almost exclusively used to describe the external dimensions of parts.
With that being said, the diameters of thin, flexible parts can be very challenging to measure at times. Tools such as a Visual Measurement Machine, which provides a non-contact method that also takes into account the inevitable part out-of-roundness, can be invaluable for accurate inspection.
The diameters of PTFE and polymer seals are also typically the most difficult dimensions to tightly control while machining, especially at larger sizes. This is due to the inherent instability of polymer materials. Fortunately, most seals are not critically dependent on diameter precision for functionality.
Radial Cross-Section
The radial cross-section of a seal sometimes referred to as the “wall” is equal to the OD minus the ID, divided by two. The radial cross-section is often the most critical dimension for the functionality of a seal. This dimension will determine the compression or squeeze on a spring or O-Ring energizer which is responsible for providing the contact and sealing force of the seal.
Too little or too much compression or interference can cause a number of problems from leakage to excessive wear. Thankfully, the cross-section dimension is typically easy to hold within tight machine tolerances and easy to inspect.
Seal Width or Height
The axial length of the seal can be referred to as either the seal width or seal height. Eclipse typically uses width rather than height because this dimension is most often checked with calipers while holding the seal in your hands, rather than with a height gauge on a calibrated flat surface.
The seal width will always be dimensioned to have clearance in the hardware gland, but how much clearance can be important. In reciprocating applications, a seal too undersized for the groove can shuttle back and forth in the gland causing accelerated wear.
This also creates an opportunity for the seal to become cocked or misaligned in the groove which can lead to premature failure.
Rod and Piston Seals
The majority of the seals Eclipse produces fall under the category of a rod or piston seal. A piston seal typically seals the inside diameter of a cylinder or bore, meaning the outside diameter of the seal is the sealing surface. A rod seal is typically sealing on the outside diameter of a shaft, thus the inside diameter of the seal is the sealing surface.
While this is straightforward most of the time, things are not always as clear. Many HPLC (High-performance liquid chromatography) and other lab testing equipment applications use ceramic shafts that act as reciprocating pistons. So, while they may need a seal for a piston, the product will in reality be a rod seal.
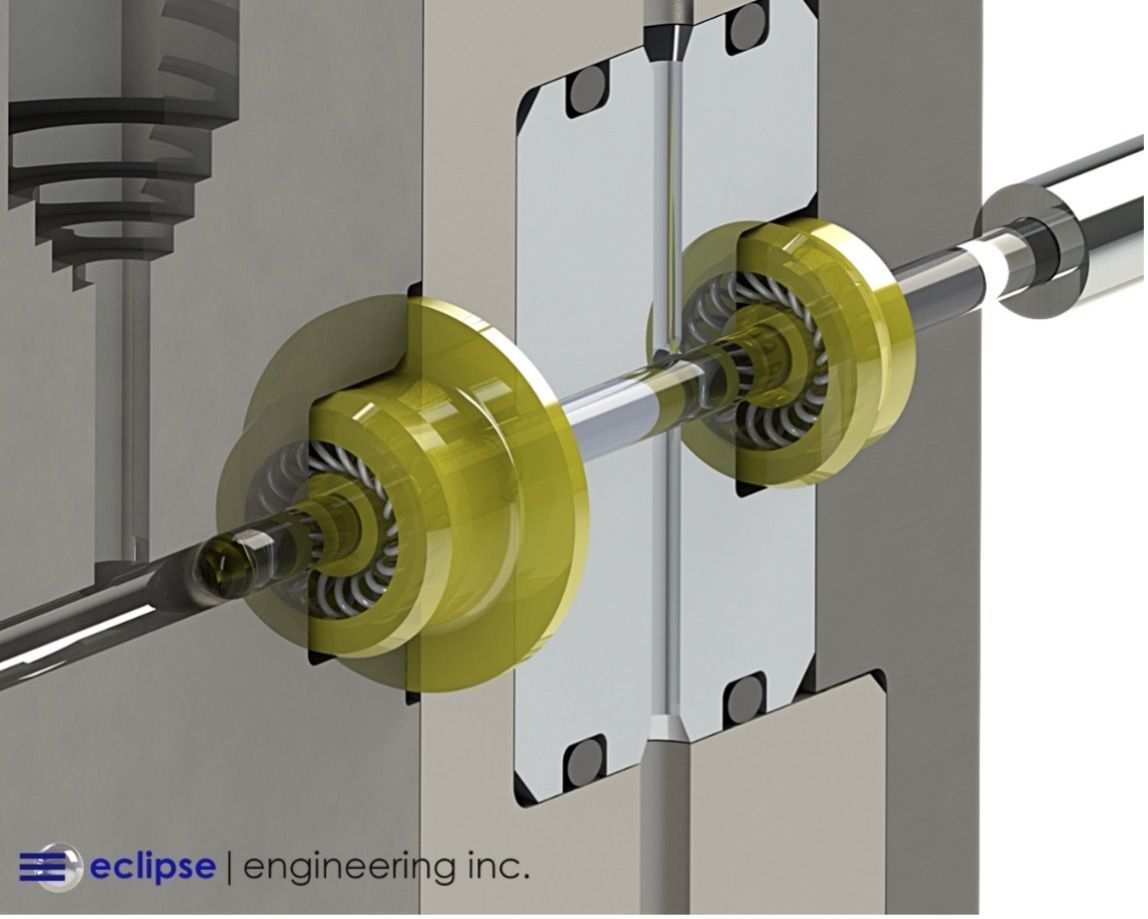
To avoid confusion, we usually differentiate rod and piston seals based on the dynamic sealing surface. If the OD of the seal is dynamic, it’s a piston seal. If the ID of a seal is the dynamic surface, it’s a rod seal.
Some seal types, like most cantilever spring seals, are symmetrical in design and can be used for either application. Other seals, like Canted Coil Spring seals, have different geometries based on whether the OD or ID is the primary sealing surface.
This is to provide optimum loading and wear characteristics to extend seal life and enhance sealability.
E-Gap
E-Gap is short for extrusion gap and is defined as the clearance between the hardware components. In a piston configuration, this would be the clearance between the piston and bore. In a rod configuration, this is the clearance between the rod and the housing it’s passing through.
In short, it is the physical gap that needs to be sealed in the hardware. It is one of the primary factors in the pressure handling capability of a seal. Seals improperly designed for a particular extrusion gap will cold-flow or extrude through this opening at high pressures.
If you’re wondering how much pressure a seal can hold, the E-Gap will likely be our first indicator.
PV – Pressure Velocity
The PV of a sealing system is the pressure multiplied by the surface speed of the dynamic seal interface.
PV is used as a quick gauge of the plausibility of the success of a sealing system in a given application. The exact value itself is not of tremendous importance, but it provides a relative idea of the stress and projected wear life of a seal.
Trade Names and Acronyms Galore
Polytetrafluoroethylene doesn’t exactly roll off the tongue. How about Polyether Ether Ketone? Anyone need some Ultra High Molecular Weight Polyethylene?
Many of the seal materials Eclipses uses on a daily basis are commonly known and referred to simply by their acronyms (PTFE, PEEK, UHMW) rather than the full chemical names.
Other seal materials are commonly known by trade or brand names, not unlike consumer products like soft drinks or generic prescription drugs. Fluorocarbon (FKM) O-rings for example, are usually called trade name Viton® even if a generic compound is being used.
Teflon®, the first and most common trade name for PTFE is a household term thanks to non-stick frying pans. Yes, this is the same PTFE used to make seals and the low friction and high heat capabilities are a benefit in many sealing applications.
Blended PTFE seal materials can get even more convoluted with multiple fillers having trade or generic names which may or may not be used. Most seal companies also assign their own material codes even if the blend of PTFE is common throughout the industry.
Don’t worry if you’re not a chemist, we’re here to decipher the alphabet soup and provide the best material for your application.
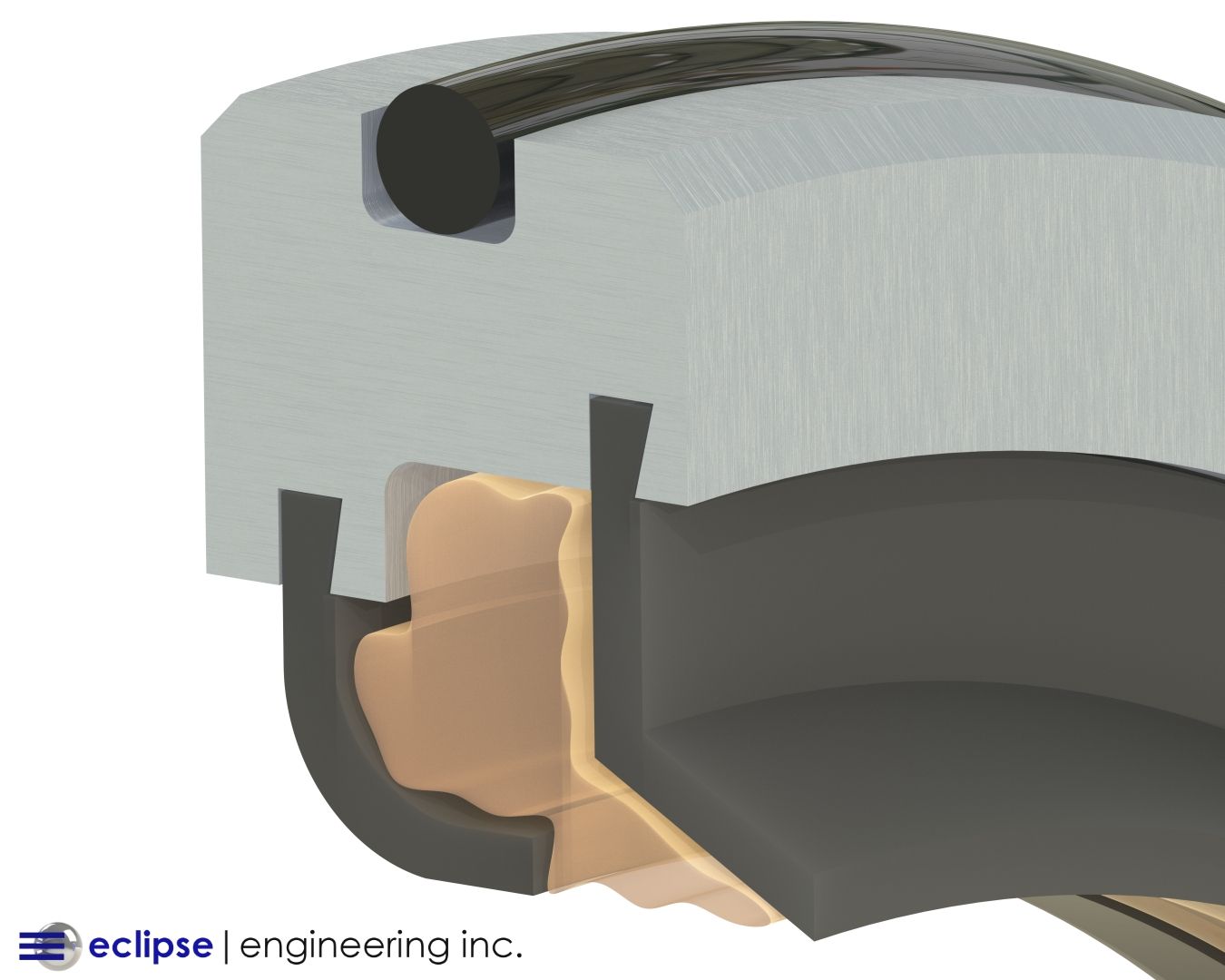