Case Study: Angled Spring Grooves for Custom Spring Energized Ball Seats
A Ball Valve is a simple and robust valve used in applications and industries across the spectrum. It consists of a ball with a hole through the center that can be rotated 90°. The hole is either aligned with flow and thus open, or perpendicular to flow and therefore closed. The straightforward quarter-turn action is fast and simple to operate, and the position of the handle provides a clear indicator of whether the valve is open or closed.
Most typically used as a shut-off valve, many households likely use ball valves at some point in the water supply plumbing. Not relegated to common plumbing, many industries use ball valves for critical control applications including aerospace and cryogenics. Their reliable operation and high-pressure handling ability make them an attractive solution for many specialty operations.
The seals inside the ball valve obviously play an important role in their performance and reliability. There are two main seals in a common ball valve, they are referred to as seats. The seats are typically machined or molded to match the diameter of the ball and are mechanically compressed against the ball face. Seat material varies by application needs, but Virgin PTFE is frequently used.
Eclipse was approached by a customer looking for a very specialized ball seat. They wanted to utilize a spring energizer in the seat. While easy to suggest, this would create a significant challenge in the manufacturing of the seal. Eclipse, nevertheless, would be up for the intrepid endeavor.
The Client's Issue
Eclipse’s customer was looking for a sealing solution for a ball valve in their industrial gas processing plant. The ball valve would serve as a critical shut-off point in the system. The valve would be actuated by an electric motor and therefore could be operated remotely.
The customer was looking for an improvement in the overall wear life of the ball seats, while at the same time, providing consistent and predictable actuation torque. Being motor activated, the torque required to move the ball open or closed was limited. Therefore, the friction generated by the ball seats would need to be carefully controlled.
Operating Conditions:
Ball Valve Seat
Ball Diameter: Ø2.500”
Media: Petroleum Processing Gases
Pressure: 100 PSI
Temperature: -40° to 175°F
The Eclipse Solution
The typical PTFE ball seat can provide many years of service over many cycles and still retain positive sealing. Over time, unenergized PTFE will wear and leakage will eventually occur. While there are valve designs that incorporate external springs to energize the seats, the customer was looking to retain a simple hardware design without adding mechanical components and increasing the physical size of the valve.
Eclipse knew a spring energized seal would be the answer. Eclipse designs and manufactures thousands of spring energized seals every year, all which provide the sealing characteristics the customer was desiring here. The concept, design, and functionality would certainly be nothing uncommon to Eclipse, but the packaging within the constraints of a typical ball seat would provide the challenge.
In order for the spring to function properly, as in a regular radial seal, the spring would need to be oriented at an angle that would match the contour of the ball. While contact could be made with the ball using a standard face or radial spring orientation, the effectiveness of the spring would be greatly reduced since the compressive force would not be acting in the correct direction. Consequently, deflection range and therefore wear life would be compromised.
For the spring seal to function at its full potential, the angle at which its containment groove is machined within the seal would need to match the angle of incident of the ball. This presented a manufacturing challenge as the necessary angle would certainly be non-standard to any available lathe tooling.
Eclipse designs and many times fabricates all the necessary lathe tooling in-house. Grinding and sharpening tools is a normal and frequent operation performed by Eclipse’s skilled machinists. This allows Eclipse to frequently machine complex or custom shapes and spring grooves. But in this case, the angle at which the spring groove tool would need to be made would be impossible to produce with conventional tool grinding equipment.
In such instances, Eclipse turns to EDM (Electrical Discharge Machining). EDM allows geometries that normal would be impossible to grind such as nearly sharp inside corners and back angles. Eclipse’s environment of an integrated relationship between its production and engineering staff allowed the necessary CAD model files to be designed to facilitate the production of the EDM tools.
The final step would be to fabricate a custom tool holder to mount the EDM tool. With that, the necessary steps to machine a spring groove at the unusual ball angle would be complete. A simple seal design concept can take the efforts of multiple engineers, machinists, and manufacturing techniques to achieve. Eclipse thrives in these situations and prides itself in its innovative manufacturing methods and solutions.
Turning back to the seal design, Eclipse chose it’s EZ038: Graphite filled Modified PTFE as seal material. The benefits of Modified PTFE would greatly be utilized in this application. It’s improved resistance to cold-flow compared to conventional PTFE would help ensure long life. It’s superior permeability resistance and the ability to achieve an excellent seal surface finish combined with the graphite filler, make it ideal for critical gas sealing.
How it Performed
The advantages and benefits of spring energized PTFE seals are realized everyday in applications across the world. These are usually limited to either rod or piston seal configurations. Adapting this design to work in a ball seat arrangement presented some unique manufacturing challenges. Eclipse’s team of experienced engineers and machinists welcomed the opportunity and successfully designed and fabricated the necessary tooling.
The spring energized ball seat was able to extend the wear life and service interval of the valve. The spring is able to keep constant energy on the sealing lip contacting the ball, even as the lip wears. While extending the life of the seal, the spring energizer also facilitates predictable and consistent actuation torque by carefully controlling seal friction. The customer was ensured the remote motor actuation would always function as intended.
The customer was very pleased with Eclipses custom design, engineered and manufactured ball valve seat. Contact Eclipse today with your challenging sealing application.
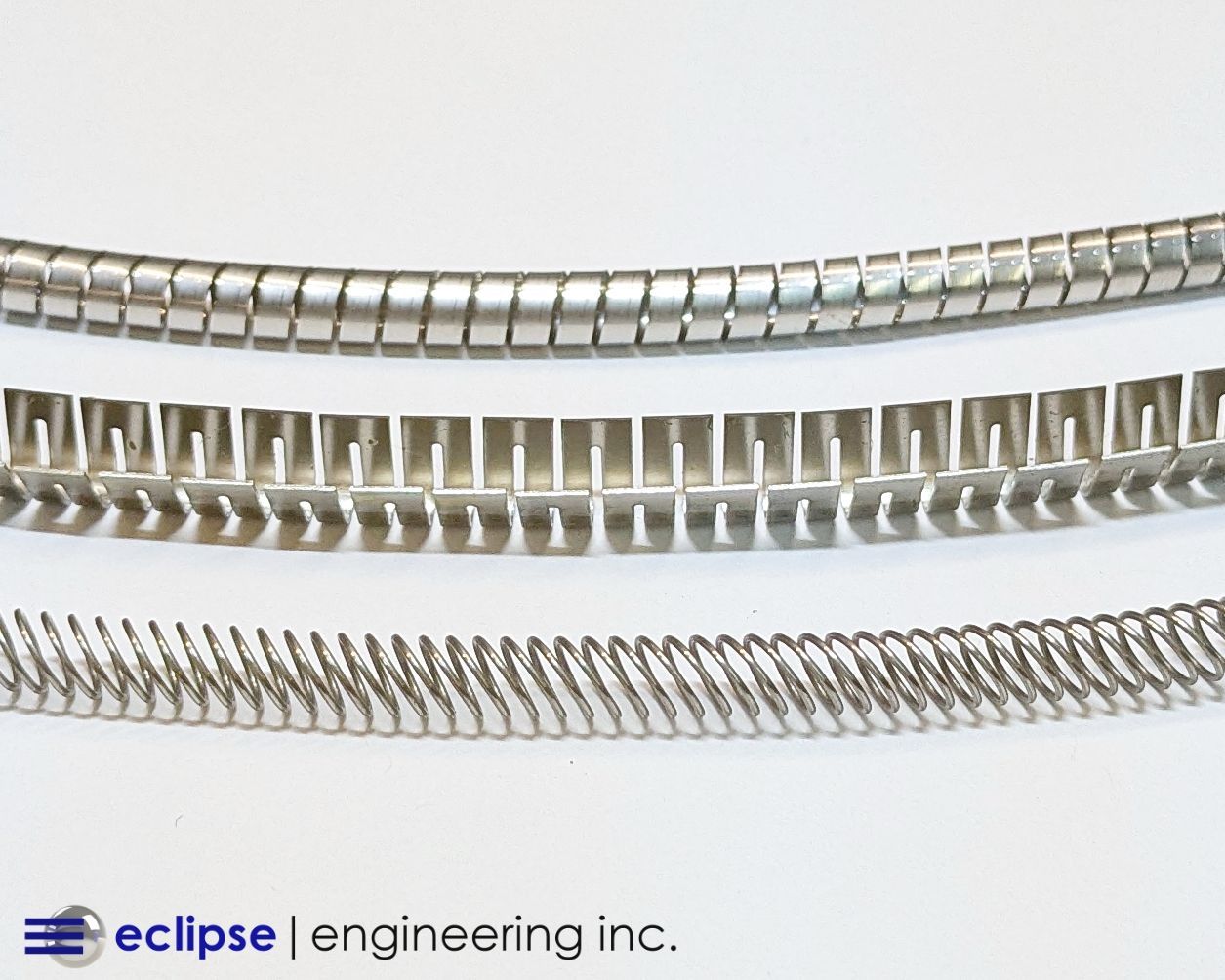