Case Study: Balancing Extrusion Gap and Wear Ring Exposure in a High-Pressure CO2 Extraction Application
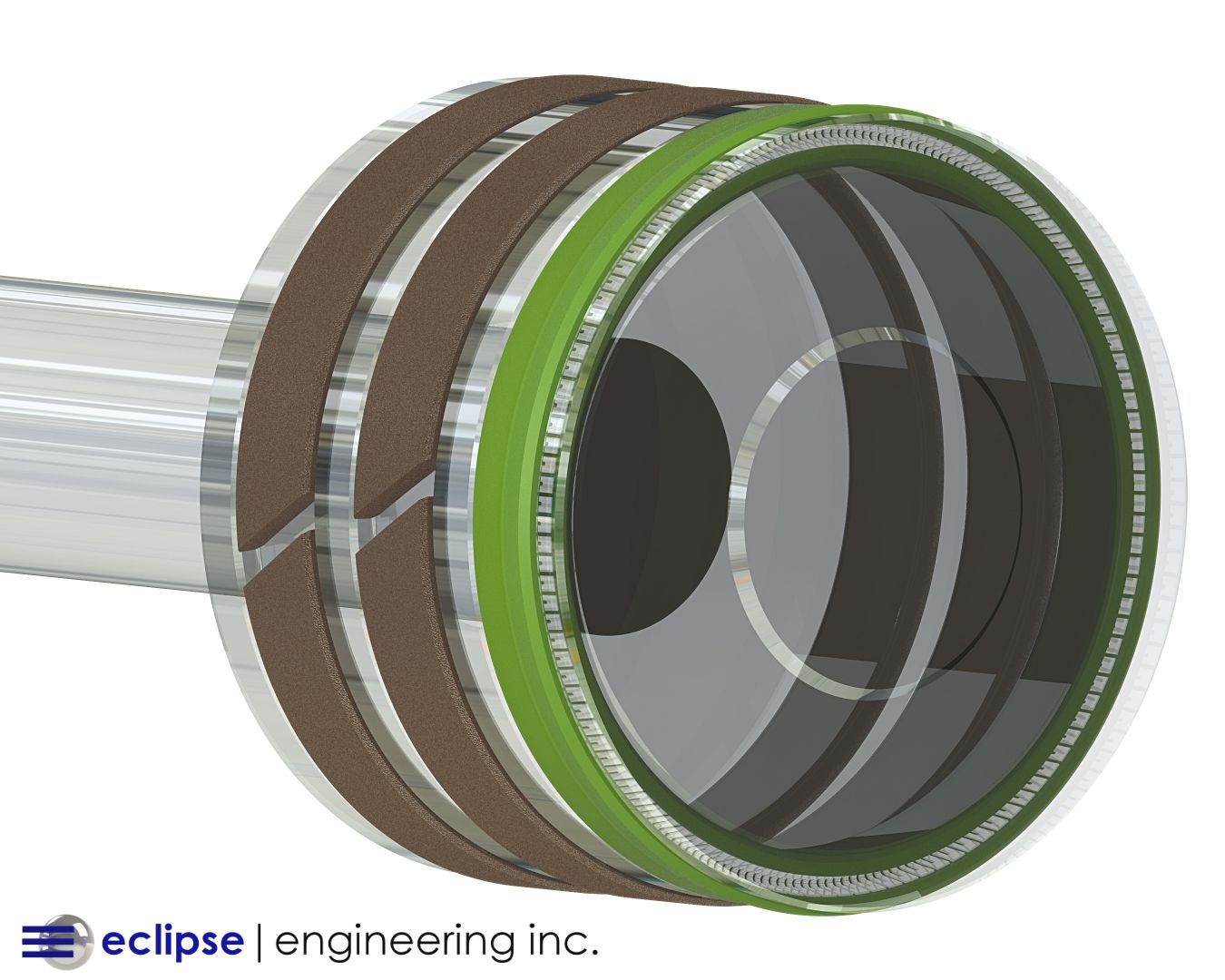
Often, seal designers can seem like they’re caught in constant struggle to balance the demands of sealing application with the reality of physical and material constraints. It is the job of the engineers at Eclipse to understand and weigh these limitations with the goals of the application.
For example, when a customer needs an extremely low friction seal yet very high sealability, there is always a compromise that needs to happen. The magic seal material that has the pliability and excellent seal characteristics of rubber and the low friction, high wear resistance and temperature range of PTFE, simply doesn’t exist.
Another frequent scenario is when the customer needs a seal to accommodate loose or poor hardware tolerances yet has a very small physical envelope to incorporate a seal. The smaller the seal, the smaller the effective deflection range due to the physical limits or an O-Ring or spring. While the application might need cover the range of a 400 series spring or O-Ring, there might only be room for a seal the size of a zero series, which obviously presents a problem.
Similarly, a customer might have the desire for a seal with very long wear life, yet the hardware assembly may be severely limiting in the area meant for the seal. Eclipse has been presented numerous applications where a space for a seal was never even considered in the original design. Without a properly sized seal, wear life has the potential to be restricted simply due to the fact there is less seal material available to be worn away before structural integrity and therefore sealability is compromised.
Another very common problem in sealing applications where bearings are needed, is the balance between the having enough exposure for the wear rings without also causing too large of an extrusion gap to create complications for the seal.
Eclipse was approached by a customer facing this very issue in their high-pressure, supercritical CO2 extraction equipment. Eclipse’s decades of experience meant they came to the right place for the optimal sealing solution.
The Client's Issue
With the growing popularity of Cannabis derived products such as CBD oil, the processes for extraction have come under examination for increased productivity and durability. A customer came to Eclipse looking to redesign the piston seals used in their CO2 SFE extraction equipment.
The customer was looking for improved wear life and longevity of the seals, as well as, improved lead-time and availability of the seals once they needed to be replaced. The customer’s increased production volumes and run-rates where quickly wearing out the OEM seals and they were unhappy with the lead-time and service of the original seal supplier.
With some of the best lead-times in the industry for custom PTFE seals, Eclipse knew it could deliver if an improved seal design could be implemented.
Operating Conditions:
Reciprocating Piston Seal
Bore Diameter: Ø3.250”
Stroke: 6”
Cycle Rate: 35 cycles per minute
Media: CO2
Pressure: 800 – 5,000 PSI
Temperature: 65° to 175°F
The customer was willing to redesign the piston seal gland configuration, but the overall length of the piston could not be changed to ensure correct functionality in the original equipment. With significant side-loading of the piston present, wear rings would be necessary for proper piston guidance and to safeguard against any potential metal-to-metal contact between the piston and bore.
If metal-to-metal contact did occur and the bore was scratched or galled, the customer would face extensive down-time while they wait for a replacement part. This would cost them a significant amount of money from lost productivity, not to mention the cost of the replacement bore. To mitigate this potential risk, the customer was unwilling to eliminate wear rings or reduce their width, thus Eclipse was faced with a design constraint with the amount axial space available on the piston for the seal.
This space constraint presented a challenge because with the importance of proper wear ring exposure in the system, the extrusion gap therefore needed to be sizable. With limited space to either substantially extend the heel of the seal, or incorporate a back-up ring, Eclipse would need to utilize some special design techniques and features to present a high wear life seal.
The Eclipse Solution
Balancing extrusion gap and wear ring exposure is very typical problem in the seal industry. In systems where operating pressures are relatively low this might not be a problem, but when pressures increase seal integrity can quickly become compromised.
In a piston application, wear-ring exposure and seal extrusion gap become the same entity. In most cases, once tolerance stack-ups are performed with both the bearing and hardware dimensions, the resulting necessary exposure dimension will be far beyond the typical maximum extrusion gap recommendation for the seal.
Not given enough exposure on the piston, the wear ring has the potential to be loose in the groove making it ineffective as a bearing. This would place undue side loading on the seal leading to premature failure and/or the piston contacting the bore. In almost every case, this metal-to-metal contact will likely gall or score the bore enough to destroy a proper sealing surface finish, if not more extensive damage.
On the other hand, if the extrusion gap for the seal resulting from the needed bearing exposure is too large, the seal will eventually be pushed into the gap by the pressure and ultimately cause a failure. The higher the pressure of a system, the smaller a recommended extrusion gap will be. Without any other considerations, extrusion gaps are typically suggested to be made as small as possible. This fact is obviously diametrically opposed to the need for bearing exposure.
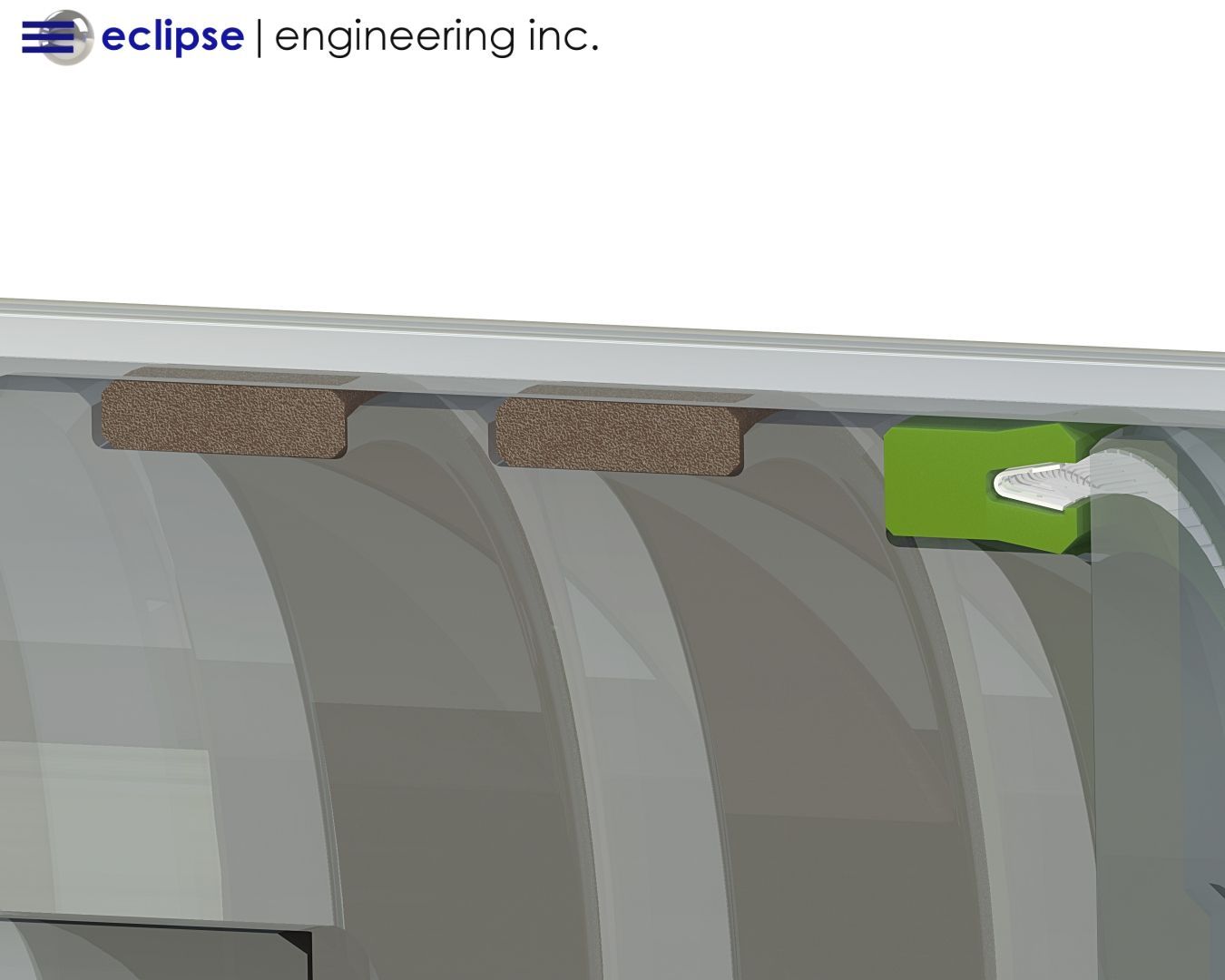
To combat large extrusion gaps, spring energized seals (as in this case) can be made with an extended heel design. This physically puts more sealing material behind the seal that can be deformed into the gap without affecting the critical area of the seal. The other common solution is to incorporate a back-up ring behind the seal. A back-up ring can be designed to basically reduce the size of the extrusion gap the seal is exposed to.
However, both of these solutions would require additional axial space on the piston, which Eclipse did not have the luxury of working with. Eclipse started by using a smaller spring series than the hardware cross-section would typically call for. The smaller spring would effectively allow the heel of the seal to be extended, aiding in the extrusion resistance of the seal. This also means the sealing lips would be thicker than normal.
Eclipse utilized this extra material in the lips to modify the seal geometry to further fortify against high pressure failure. The ultimate failure mode of a spring energized seal due to extrusion is usually when deformation of seal reaches the hinge point of the spring cavity. To guard against this, Eclipse offset the location of the spring groove to thicken this vulnerable hinge point.
Eclipse chose its ET040: Polyimide/MoS2 filled PTFE for the spring energized seal jacket. While not the most extrusion resistant material Eclipse has to offer, the customer’s stainless-steel bore material was limiting on how aggressive the seal material could be. ET040 would provide a good level of toughness without wearing the bore. The added internal lubricity reduces friction and the fine particle size of the Polyimide improves sealability while sealing gases such as CO2.
Eclipse chose its ET010: Bronze filled PTFE for the wear rings. This industry standard bearing material would fit well within the design objectives of the project.
How It Performed
With Eclipse’s revised seal and piston design, the customer saw increases in seal life and reliability. This allowed them to run their production processes for longer intervals between scheduled maintenance. The reduced down-time increased plant productivity positively affected the customer’s bottom-line and allowed them stay on top of shipments of their high demand product.
The customer was also very pleased with Eclipse’s comparatively short lead-time and reliable delivery on replacement seals. Their moderate investment in redesigning their piston configuration to use Eclipse seals proved to be profitable choice.
Contact Eclipse today if your sealing application could potentially benefit from Eclipse’s custom designed and manufactured seals.
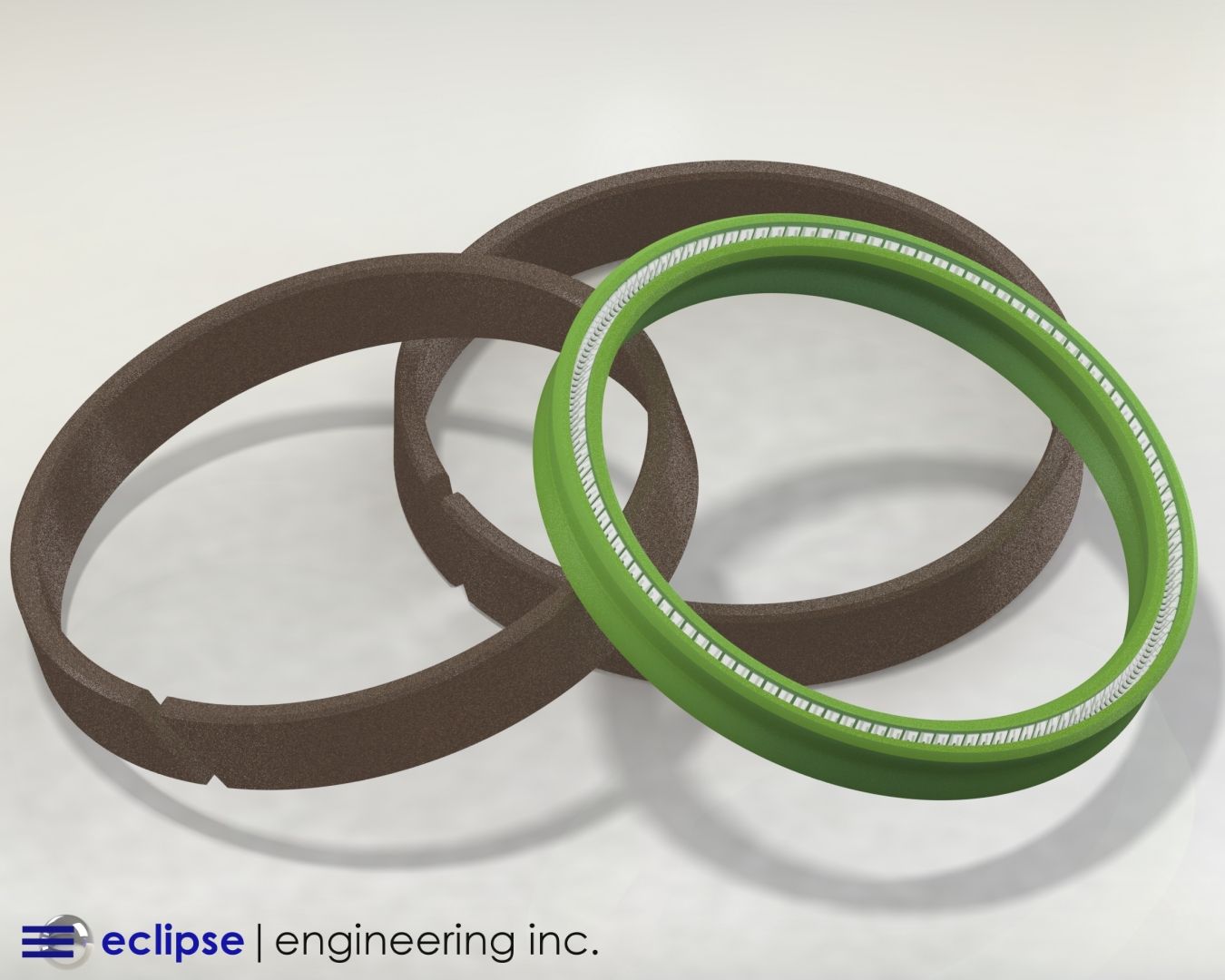
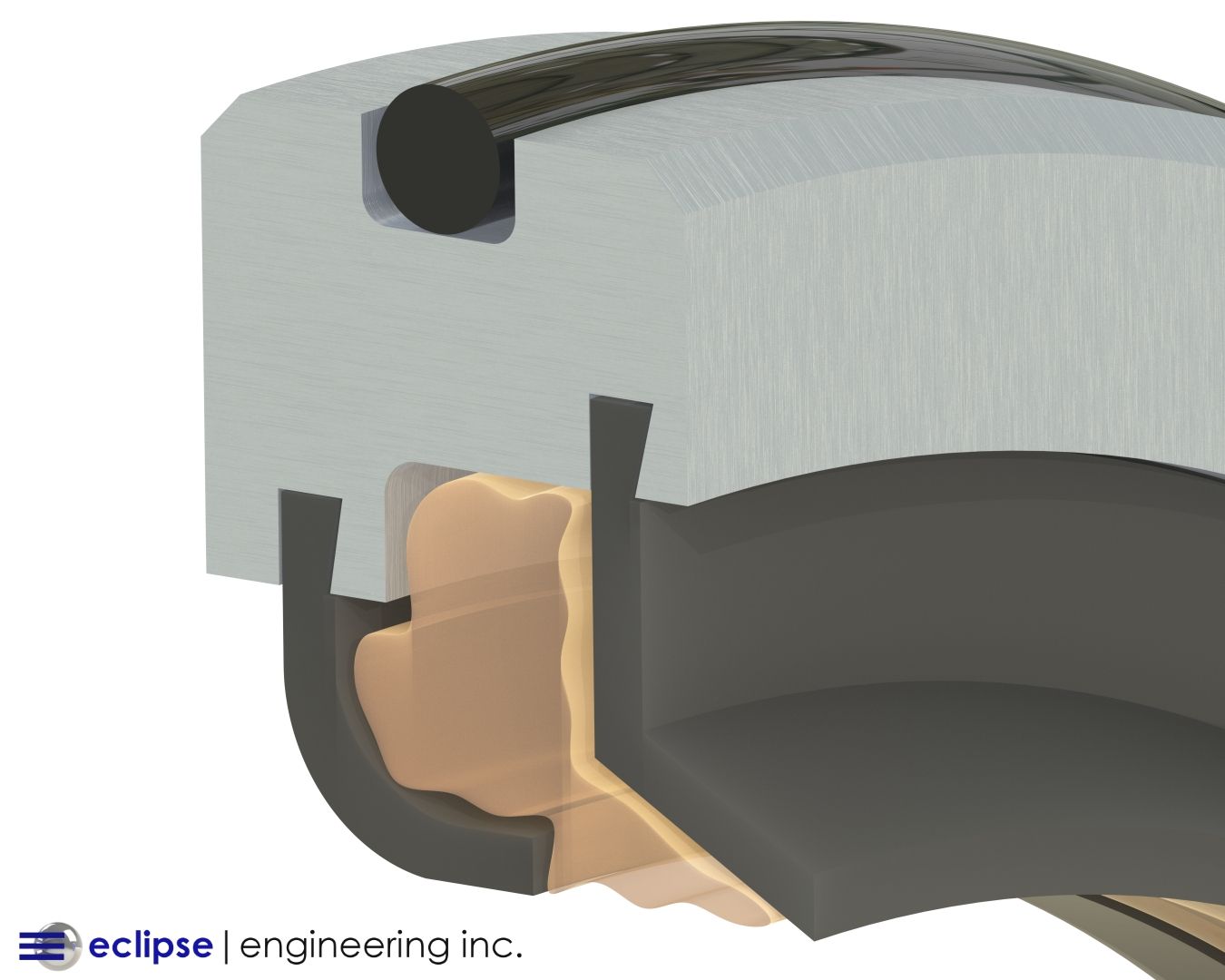
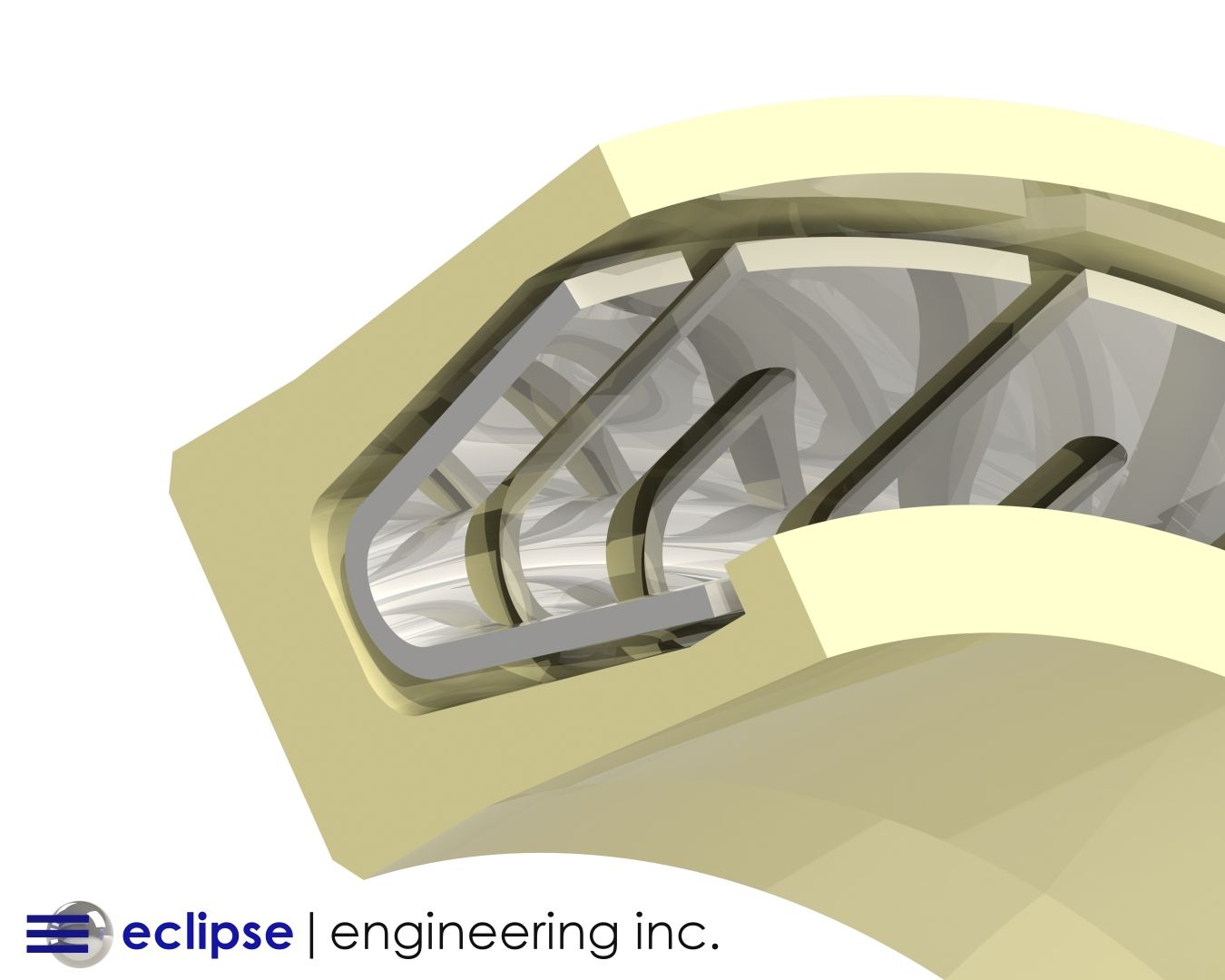