Case Study: PEEK Spring Energized Seal in a High Temperature/High Radiation Application
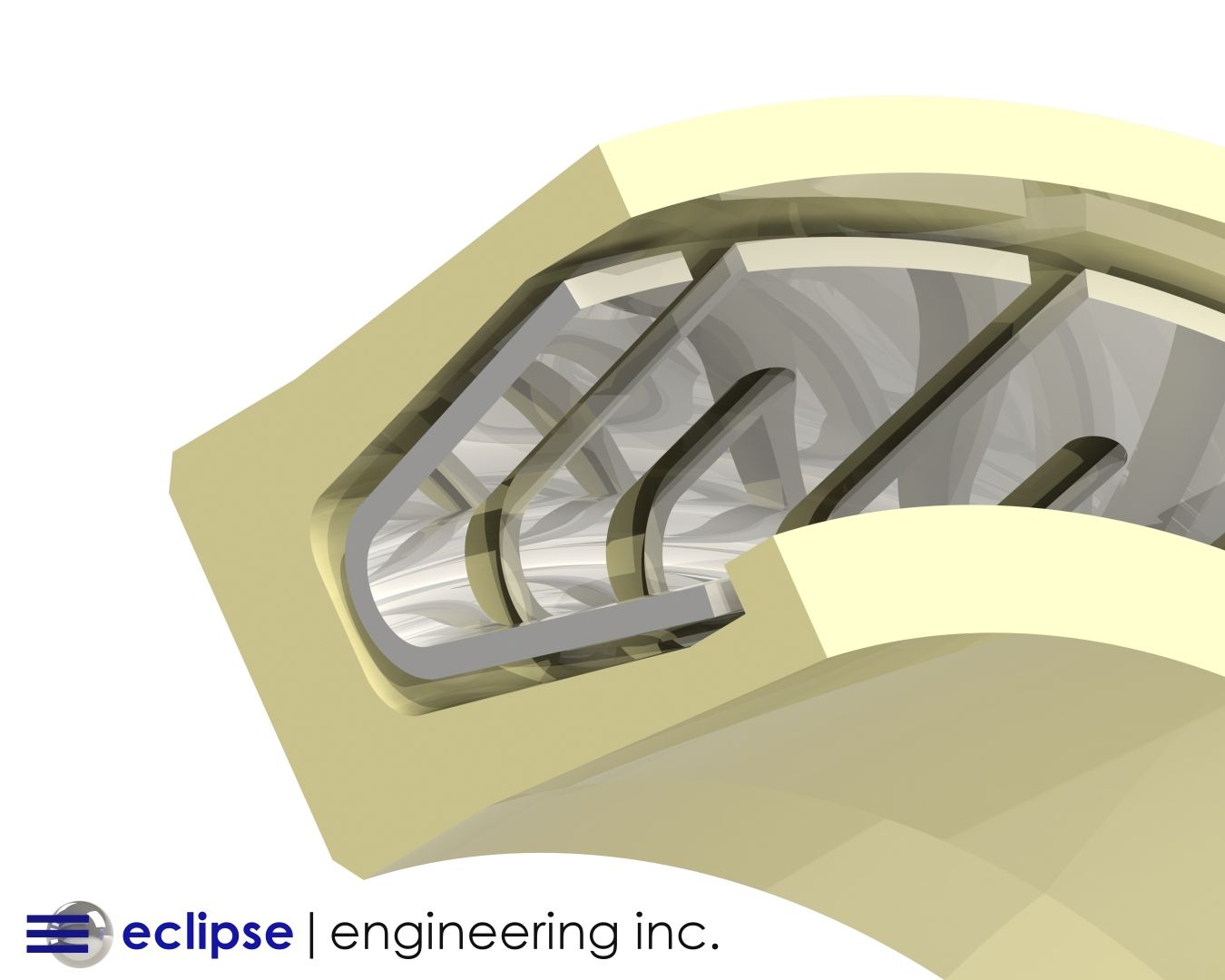
Eclipse has engineered sealing solutions for applications all over the planet and in a plethora of environments. From the bottom of the ocean to orbiting the earth, Eclipse is challenged by the unique conditions in each application. Whether it be extreme temperature and pressure or severely caustic or abrasive media, Eclipse has a solution for most every sealing problem.
One distinct environment presents a particularly challenging set of circumstances for seal design – high radiation. Eclipse’s primary seal material choice for many applications is PTFE and PTFE blends. With all the wonderful attributes PTFE possesses as a seal material, radiation resistance is not one. In high radiation environments PTFE’s properties can degrade to essentially rule it out as a suitable material.
The options for effective sealing materials that are also radiation resistant becomes very limited. The seal designer is therefore confronted with creating a seal that is expected to perform in every way a typical PTFE seal operates, out of materials that are not as favorable to sealing. This is where Eclipse’s engineering experience and expertise in seal design come to the forefront.
The Client's Issue
Eclipse was approached by a customer that was looking for a seal solution for a sensor used in a nuclear application. It would be operating in an environment with both high temperature and high Gamma radiation.
Operating Conditions:
Reciprocating Rod Seal
Rod Diameter: Ø1.000
Stroke: 1.5”
Cycle Rate: 2-4 cycles per minute
Media: Air, Salt Water Mist
Pressure: 100 PSI
Temperature: 70° to 450°F
Gamma Radiation Exposure: 10^6 rads
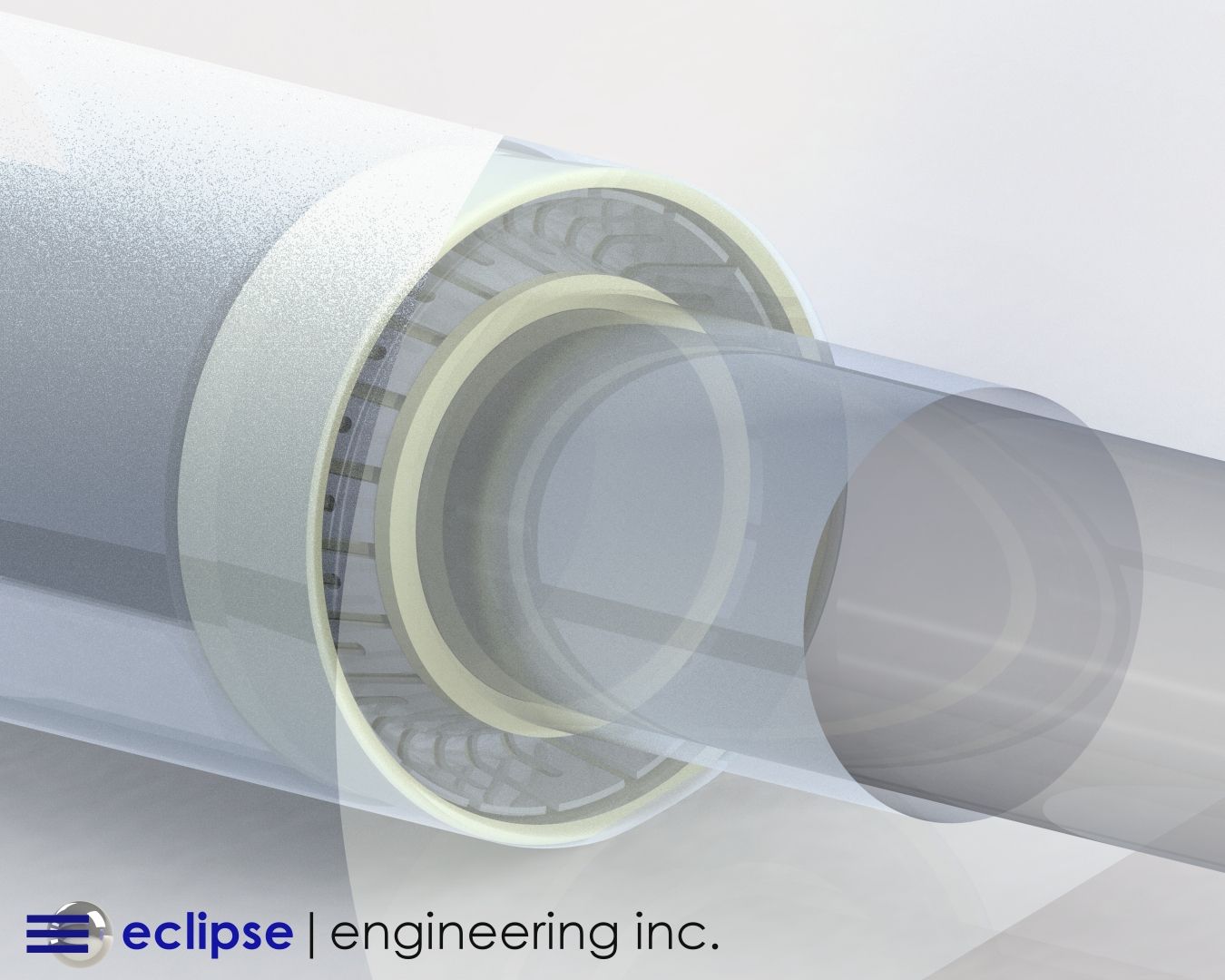
Aside from the radiation exposure, this would be a relatively mundane sealing application for one of Eclipse’s PTFE Spring Energized Seals. But that level of radiation quickly eliminates PTFE as a suitable seal material and greatly complicates the seal design.
PTFE’s Limitations in Radiation
PTFE’s has many benefits as a seal material. It’s noted for its low friction, high temperature and chemical resistance. At Eclipse, PTFE based seals are our primary business, whether it be O-Ring or Spring Energized Seals. With all the many of advantages of PTFE, unfortunately it cannot be utilized in high radiation environments. When compared to other common plastics, PTFE actually is one most susceptible to radiation degradation.
Radiation has an embrittlement effect on PTFE, exposure degrades PTFE’s tensile strength and elongation properties. High enough levels and exposure time can actually casue PTFE to crumble and ultimately be reduced to a powder. Unfortunately, tensile strength and elongation, which dictate a materials flex characteristics, are some of the the most important properties when considering a material for a seal.
The threshold for radiation damage of PTFE is 2 to 7 X 10^4 rads. Depending on exposure time, dosages above this level will likely compromise PTFE’s tensile and flex properties. It is important to note that in vacuum, the damage threshold is about ten times higher. Therefore, in space applications such as in orbiting satellites, PTFE might still be an effective seal material against normal space radiation.
In the case of UV radiation, PTFE is actaully very resistant. PTFE will not degrade or age in longterm sun exposure situations. But with this application is operating in Gamma radiation at 100 times the accpetable limit for PTFE, an alternative material would be necessary. This where Eclipse’s advanced knowledge of seal design and material characteristics come in.
The Eclipse Solution
When PTFE can’t be used as a seal material due to radiation, two materials are often firstly considered. ETFE, which has many of the same properties of PTFE in terms of sealing, is typically the preferred Gamma radiation resistant seal material. It can withstand levels up to 10^7 rads. But unfortunately, for this particular application, the upper operating temperature of 450°F ruled out the use of ETFE which is typically rated only to 300°F.
It would be worth mentioning that ETFE’s market availability can be much more limited than common PTFE and can cost many times more. For very large seal sizes ETFE can potentially be cost prohibitive as a material. Which leads into the other common radiation resistant material, FEP.
FEP again, can act very similar to PTFE in terms of sealing qualities but withstand radiation levels 10 to 100 times greater. While this would get us into the needed range for resistance, the customer was uncomfortable with no safety factor or security margin. Plus, the operating temperature again would be at or over FEP’s normal stated maximum.
So, with both common high radiation seal materials ruled out, Eclipse turned to a familiar, but rather unconventional seal material – PEEK. PEEK possesses one of the highest radiation resistances out of all commonly available plastics. It can withstand exposure in the range of 10^9 rads before any property deterioration occurs. PEEK can also successfully operate at temperatures up to 500°F.
Second only to PTFE, PEEK is frequently being turned in Eclipse’s in-house machine shop. PEEK is typically used for back-up rings, bearings, and structural seal components such as seal carriers and valve blocks. But the material properties for PEEK that make it great for products needing high strength unfortunately also hurt it for being used as a seal material.
PEEK is considered a “high modulus” material, the percent elongation before break for Virgin PEEK is only 25% and hardness is 85D. Virgin PTFE by comparison is 400% with a hardness of 55D. Obviously, a material that is softer and can flex freely would be more desirable as a seal. The more a material can conform to the sealing surface the better the resulting seal will be.
Eclipse’s challenge would be to create a spring energized seal jacket out of PEEK that still flexes and compiles enough to generate an effective seal. This was accomplished by carefully controlling the lip thickness of the jacket and precisely defining the hinge point. A very thin sealing lip would be easy to flex, but this would also compromise wear life and pressure handling ability, especially at elevated temperature. A sealing lip that was too thick would not allow the spring to function properly or provide energy in the correct area.
Eclipse’s experienced design engineers constructed the perfect balance of flexible lip thickness and robust design. Comparatively speaking though, the resultant lip thickness was very thin when sized against a typical PTFE lip design. At only roughly 0.012” thick, Eclipses precision machining ability would also come into play to ensure the necessary tight tolerances were met.
Eclipse chose its EP033: Virgin Grade PEEK for this application. Any material fillers would further degrade PEEK’s elongation properties. Eclipse also upgraded the cantilever V-Spring material to Elgiloy® for improved performance in the stiff jacket and greater corrosion resistance.
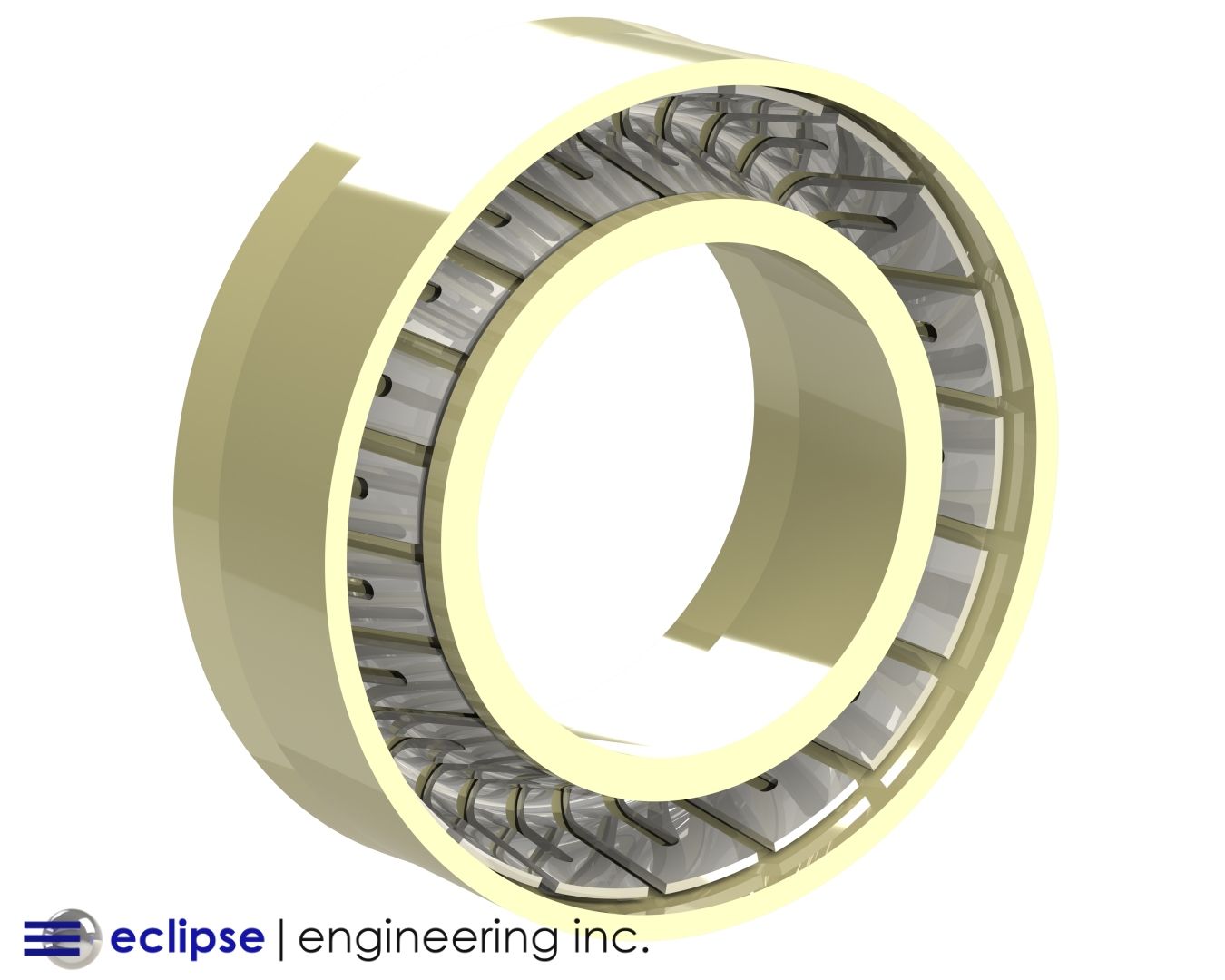
How it Performed
The customer pleased to know they could count on an effective seal at even their worst-case radiation levels. Eclipse’s detailed design and precision machining resulted in a successful sealing solution from the most radiation resistant materials available.
Contact Eclipse today if your high radiation environment is causing sealing problems or a new seal design is needed >
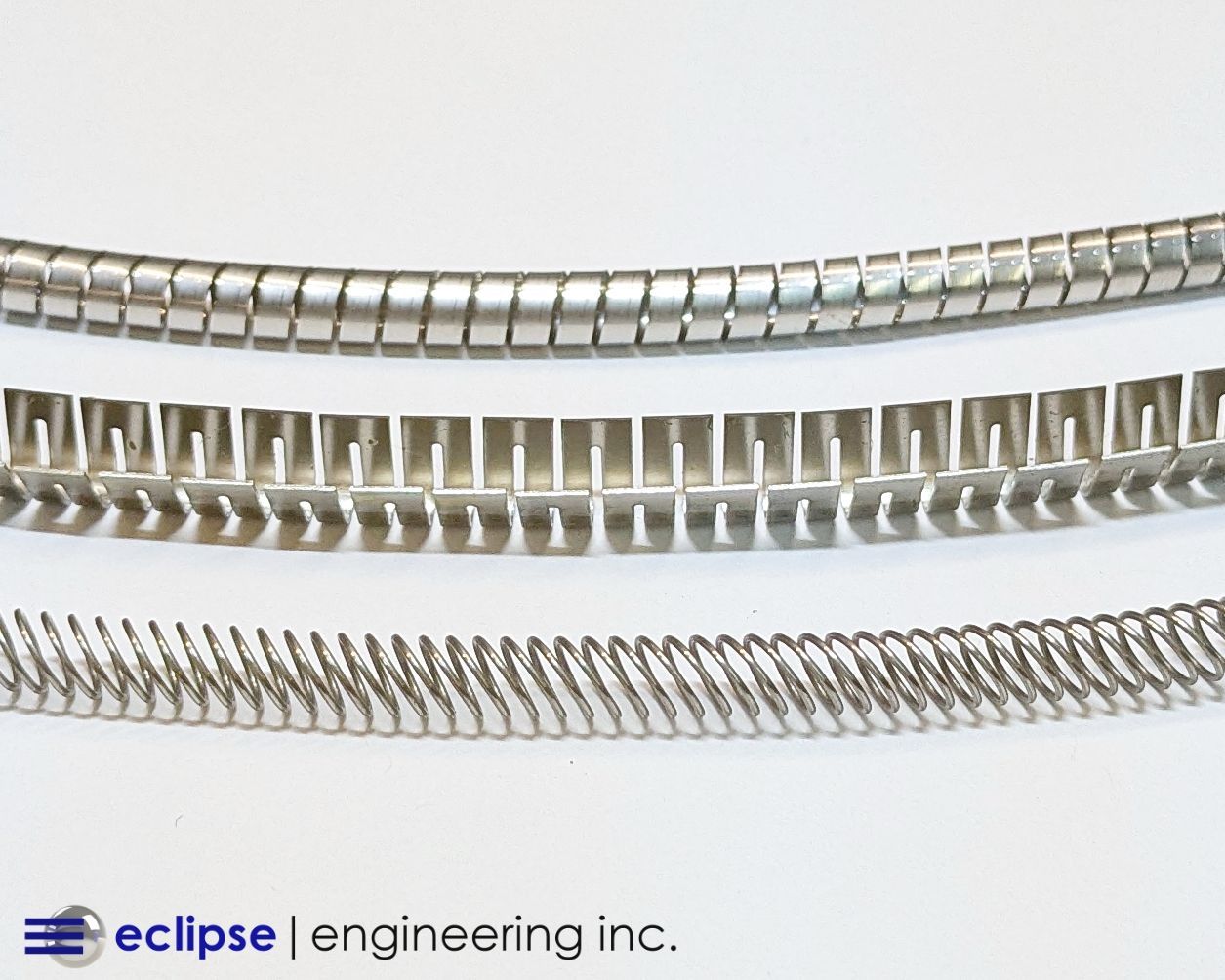