The Challenges of Rotary Sealing
Eclipse serves a highly diversified customer base from almost every sector of industry. From medical to mining, aerospace to deep-sea, each application presents its own unique set of challenges and hurdles to overcome.
Seal applications are typically classified by the type of dynamic motion the seal is experiencing. The general categories are rotary, reciprocating, and static. While each category can lend itself to difficult sealing conditions and stringent goals, we’ll see that rotary applications often present some of the most challenging set of circumstances for a successful sealing solution.
Static vs. Reciprocating vs. Rotary
In the world of seal applications, static seals have it relatively easy compared to their dynamic counterparts. With no relative motion, there is nothing to wear out. And without friction being a concern, the seals can be much more heavily loaded, promoting better sealing. That’s not to say that a static application can’t be challenging. Eclipse sees many high-pressure gas sealing applications at cryogenic temperatures. While being static, these seal designs are not trivial, often requiring special materials and finishes.
Reciprocating applications add linear motion to the mix. Classic reciprocating sealing application would be a hydraulic cylinder found in everything from bulldozers to factory presses. Reciprocating applications typically consist of a piston and rod configuration requiring seals in both places. Media can be anything from hydraulic oil to air, abrasive epoxies to food products. Seals need to withstand the wear, friction, and media impingement created by the dynamic motion.
In most cases, rotary seal applications involve sealing on a spinning shaft or rod. There are rotary configurations where a stationary seal is sealing against a rotating bore, but these are less common. There are few rotary applications that don’t require any sealing elements. Even if the equipment/machinery does not contain pressurized media, seals are still likely needed to retain bearing lubrication or exclude outside dust or debris.
The Added Difficulty of Rotary
High Pressure-Velocity
PV or Pressure-Velocity is a quick metric to determine the strain on a seal in a dynamic application. A full article explaining PV can be found here: What You Should Know About Pressure-Velocity (PV). In short, the speed and pressure of a system will combine to accelerate the wear of a seal.
Rotary distinguishes itself from reciprocating applications by its relatively easy means of creating high surface speeds and a resultant high PV. A simple electric motor can turn a shaft greater than 10,000 rpm, while it would take heavy machinery to create a high frequency, long stroke reciprocating motion at the same surface speed.
While there are few applications that require high speed, long stroke reciprocating motion, the number of industries requiring high-speed rotary seals is large and increasing. The progressive electrification of automobiles is an example. With high torque motors spinning upwards of 20,000 rpm, with no internal lubrication, seals for electric car motors present a sizable challenge for seals.
Shaft Runout
Along with high-speed rotary comes the inevitable problem of shaft runout. Runout is a mechanical specification that dictates how much a shaft can deviate from true circular motion. In essence, it can be thought of as how eccentric a shaft is moving. Some amount of runout is present in any mechanical system. The severity is dictated by component tolerance control and bearing arrangements.
Runout becomes a major problem for rotary seals as speeds increase. The seal is being asked to conform to a moving, non-circular shape as the shaft rotates around. At a certain speed, the lip will not react fast enough to stay in full contact with the shaft and leakage will occur. Seal wear will greatly be accelerated in high runout applications.
The addition of spring energizers is often mandatory if runout is excessive to help keep the lip in contact with the shaft. This adds cost, increases friction and heat build-up, and ultimately reduces the wear life potential of the seal.
Runout is something that reciprocating applications obviously won’t have to deal with.
Anti-Rotation Requirements
Another additional aspect rotary seals must contend with is the need for an anti-rotation element. While in many cases, reciprocating seals can essentially be “drop in” as far as seal installation, rotary seals need further gland considerations.
Especially at high speed, seals need to be secured on the non-dynamic side to ensure the seal does not start rotating in the gland. Seal failure will quickly occur if this happens as the seal will be wearing on surfaces not meant for dynamic motion and in an uncontrolled manner.
There are a number of means to provide anti-rotation. At lower surface speeds, an O-Ring interface on the static side of the seal can be sufficient. Seals such as Rotary Seal Rings and O-Ring OD Lip Seals utilize this functionality. This design works based on the fact that the coefficient of friction between the O-Ring and hardware will be much higher than the polymer seal and dynamic surface.
A Flanged Spring Energized Seal accomplishes anti-rotation by physically clamping the flange of the seal in the hardware. This configuration ensures positive anti-rotation, helps in static side sealing, and facilitates easy seal installation and replacement. The downside is multiple hardware components and relatively complicated and detailed groove design.
At higher surface speeds, seals are typically a
Cased Lip Seal design. This design counts on a press fit of a metallic outer cased in the hardware to ensure anti-rotation. Much like standard oil seals, the press fit allows use of the seals in an open gland without a need for addition methods of seal retention.
Single-Point Wear and Loading
The last unique challenge of rotary sealing is the fact that wear is focused on a single point on dynamic sealing surface. Unlike a reciprocating application where the seal is riding against the whole length of the rod or bore during the stroke, a rotary seal will be wearing on one point of the hardware for the life of the seal.
This combined with the possibility of very high surface speeds lead to accelerated wear of both seal and hardware. To combat seal wear in highspeed rotary applications, Eclipse has numerous filled PTFE blends designed with extending wear life specifically in mind.
ET019 and EZ032 are high fill blends intended for the most demanding wear conditions, whether it be abrasive media or high PV rotary. These blends require a fully hardened (55+HRC) dynamic surface otherwise they will quickly deteriorate hardware.
Single-Point loading also creates the problem of localized heat generation. Friction from the seal acting on a small area can lead to significant heat buildup. This is unlike reciprocating applications where the seal is acting on a different point of the hardware over the course of the stroke. This distributes the heat due to friction and gives each point time to cool between cycles.
A seal material such as UHMW-PE can work fantastic in a reciprocating application but is almost never used in rotary because localized heating can push it beyond its upper temperature limit. Adding in system ambient heat can limit the seal material options to high temperature PTFE blends.
Conclusion
Out of all the various seal applications and sealing configurations Eclipse designs and manufactures solutions for, rotary is often the most challenging. It presents some unique conditions where only specialized seals are up to the task. Many Eclipse projects have started with someone first trying O-Rings or off-the-shelf seals in a rotary application only to find immediate problems.
Eclipse is here with decades of experience in rotary applications of all types to design and manufacture a sealing solution to your challenging project.
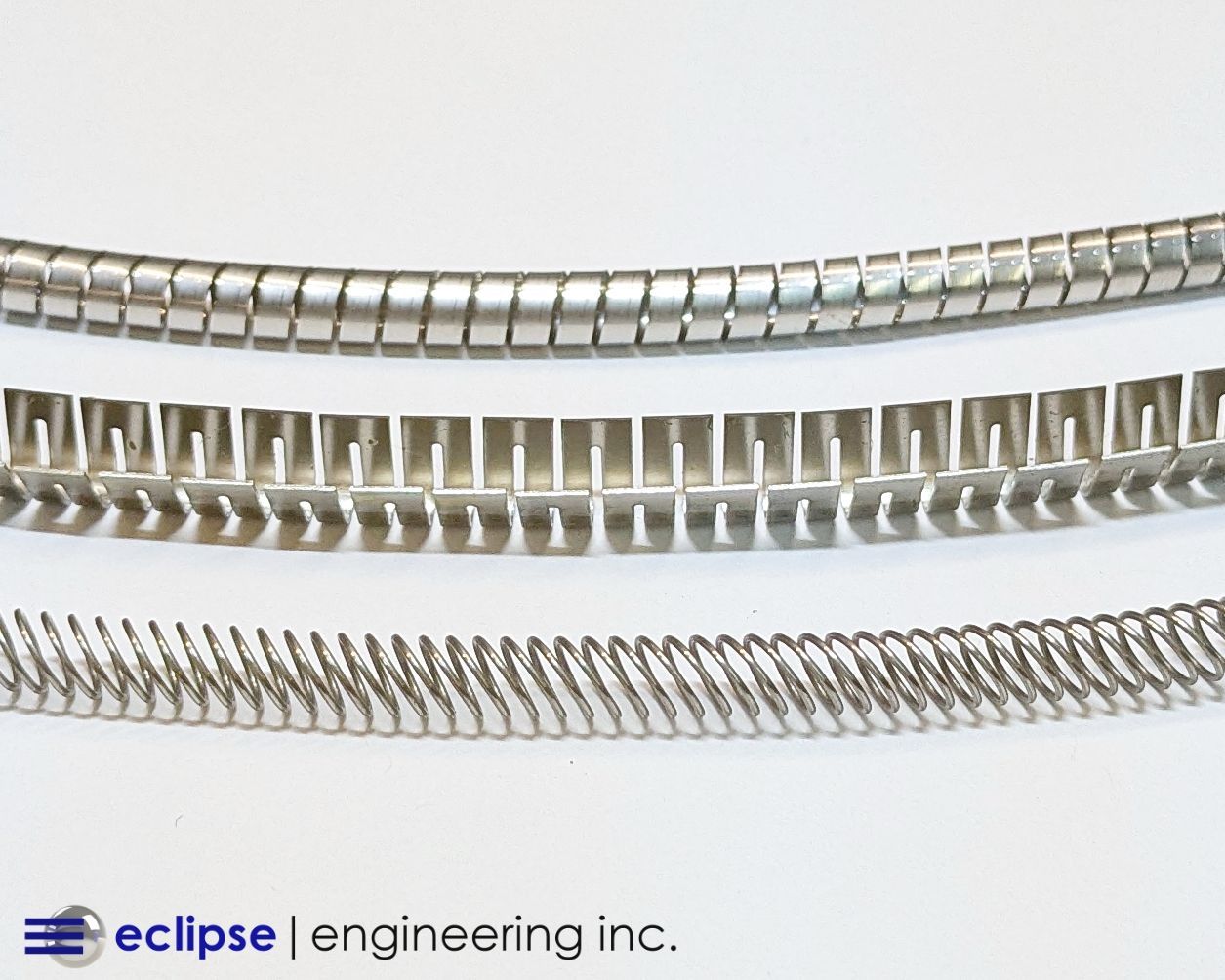