Why Do PTFE and Other Plastic Seals Need Energizers?
As the operating parameters of industrial technologies and manufacturing processes get more extreme, the need for optimal sealing solutions become that much more important.
Elevated temperatures and pressures, higher speeds, extreme environments, faster gas decompression, and aggressive medias all make sealing more critical. This extends right across static, reciprocating, rotary, and oscillating applications.
This challenge has been met very effectively by the inventive addition of energizers to seals. Energized seals give the ultimate performance in the most demanding conditions and critical applications.
Spring or o-ring energizers can extend the normal limits of PTFE and plastic materials to deliver durable ultra-tight sealing capability. Here’s a rundown of how energizers work and how they can elevate your next sealing challenge.
How Energizers Work
PTFE has highly effective physical characteristics for seals, including low friction, heat tolerance, and chemical inertness. However, PTFE also has limited flexibility and elasticity.
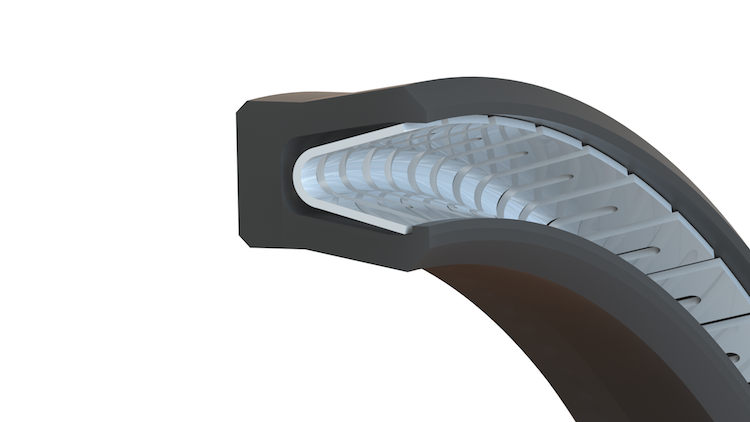
Cantilever spring seal
The addition of a spring or o-ring behind a PTFE seal lip adds a persistent ‘springy force’ or ‘energy’ to press the lip against a metal surface such as a rod or cylinder.
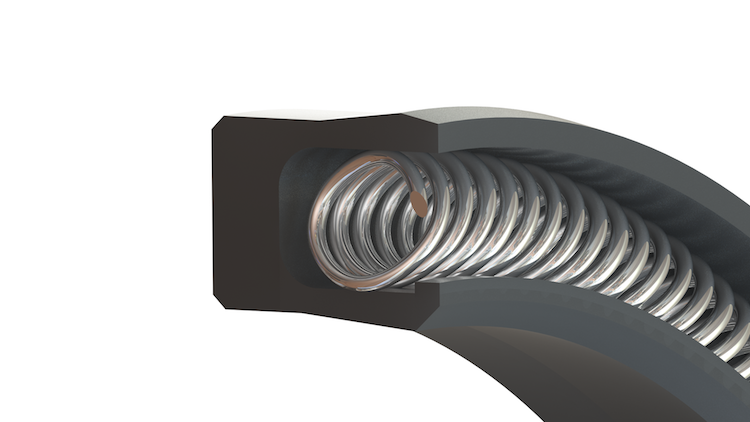
Canted coil seal
When a seal is installed into a gland/cavity, the seal lip and spring (or o-ring) are compressed radially – providing a resilient pressure against contacting surfaces. This creates a tight and consistent seal, preventing leakage of fluid or gases.
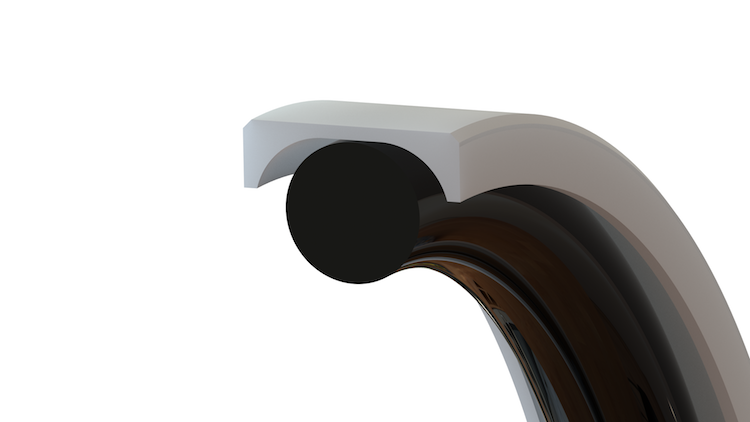
Channel seal – piston
Benefits of Energizers
The resilient pressure of an energizer compensates for and overcomes several practical problems, including the following:
Lip pressure
Even after the lip material wears down over time, the energizer continues to push the lip tightly – otherwise the seal would become loose and leaky.
Adaption to deformation
With deformation of metal components contacting a seal (rods, shafts, cylinders, housings), energized lips adaptably fit around ‘humps and hollows’ to maintain sealing.
Adaption to misalignment
When components are misaligned, such as with eccentric deflection, energized lips dynamically move in and out to maintain close contact.
Picking up the slack
Manufacturing tolerances and clearances are not critical, as energized lips can ‘take up the slack.’ Thermal expansion and contraction can be likewise accommodated
Optimal Performance at All Pressures
The radial pressure maintained by a spring or o-ring keeps sealing lips in contact with mating surfaces even before fluid or gas pressure is applied, providing good low pressure sealing capability.
When system pressure is applied, energizer action is intensified – increasing the force on lips to make a tighter seal. The radial pressure is always higher than the pressure of the fluid or gas to be sealed.
Energizer Options to Meet Your Needs
Eclipse offers a wide range of high-performance spring and o-ring-energized seals to meet rigorous demands. Contact us to find out how energized seals can cost-effectively serve your critical applications.