The Advantages of Composite Marine Bearings
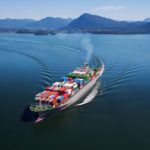
From bushings between propeller shafts and ship hulls and brushings for rudders, marine bearings are a critical component in a range of marine hardware.
As the ship-building industry continues to advance in higher operating efficiencies and enhanced safety performance, ship operators need alternative solutions to reduce costs and extend service periods between maintenance overhauls.
Composite materials are replacing traditional bronze in a growing range of marine bearing applications. These advancements in materials offer ship owners a variety of key advantages, including:
- Lower coefficient of friction
- Higher compressive load capacity
- Self-lubrication
- Suitability for fresh or salt water
- Environmentally friendly
- Easier machining of complex shapes
- Steering and propulsion systems
Composite materials offer many maintenance-free solutions to prevent galvanized corrosion, improve grease and oil systems, and more.
From the ship maneuvering system to deck equipment, here’s how composite materials are enhancing the operation and longevity of marine bearings.
Applications of Marine Bearings
Beyond the under-water applications of marine bearings listed above (bushings between propeller shafts, ship hulls and rudders), there are also many above-water applications for marine bearings. This includes deck hatch covers and roller bearings.
Sizes for marine bearings range from small applications of one-inch diameter up to huge scale applications that exceed 30 inches for large ship propeller shafts.
The Advantages of Composite Materials
Ship owners have a great need to keep maintenance and downtime of their marine bearings to a minimum, while looking for performance improvements. This is where composite materials come in.
Replacing traditionally bronze or wood bushings with composite materials can help alleviate lubricant discharges, prevent galvanized corrosion of dissimilar metals, and more.
Propeller shaft and rudder bearings made from composite materials are ideal for replacing rubber-lined, wood, and bronze bushings.
Composite bearings can also have axial grooves machined into them to provide better water flow and lubrication.
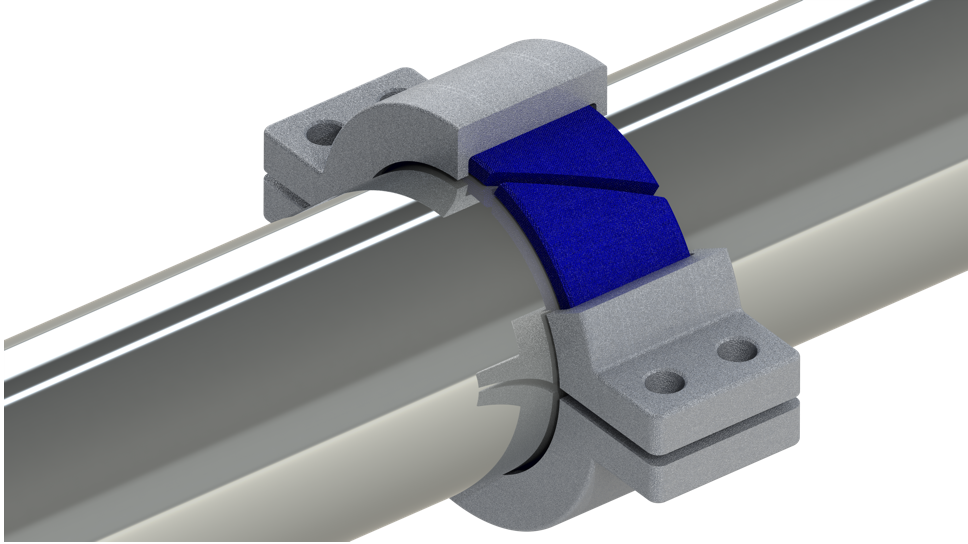
Below are the ship operations which can be improved with composite marine bearing materials.
Ship Maneuvering Systems
Side thrusters are used to make ship docking controllable and safe. They consist of a propeller in a ‘tube’ running from the left to the right side of the hull near the bow.
Side thrusters have traditionally used greased bronze bearings, but water-lubricated composite materials can extend the life of bearings while reducing vibration and promoting smooth quiet operation.
Stabilizer Systems
Lubricant discharges from fin stabilizers have prompted marine operators to look for alternative solutions to grease and oil systems.
Although environmentally acceptable lubricants are tolerated, a better option is to replace grease and oil bearings with water-lubricated composite alternatives.
Deck Equipment
Composites have successfully replaced bronze in a variety of deck equipment applications, and can work above or below the water line without the need for grease lubrication.
They can offer maintenance-free solutions that isolate dissimilar metals, preventing galvanic corrosion and providing electrical isolation of deck components.
Applications include fairlead rollers, winches, capstans, stern rollers, A-frames, davits, cranes, skidding pads, and hatch covers.
Eclipse offers high quality solutions for composite bearings optimized for a range of marine applications. Find out how you can get better performance and longevity from your marine bearings to improve your operational efficiency today >
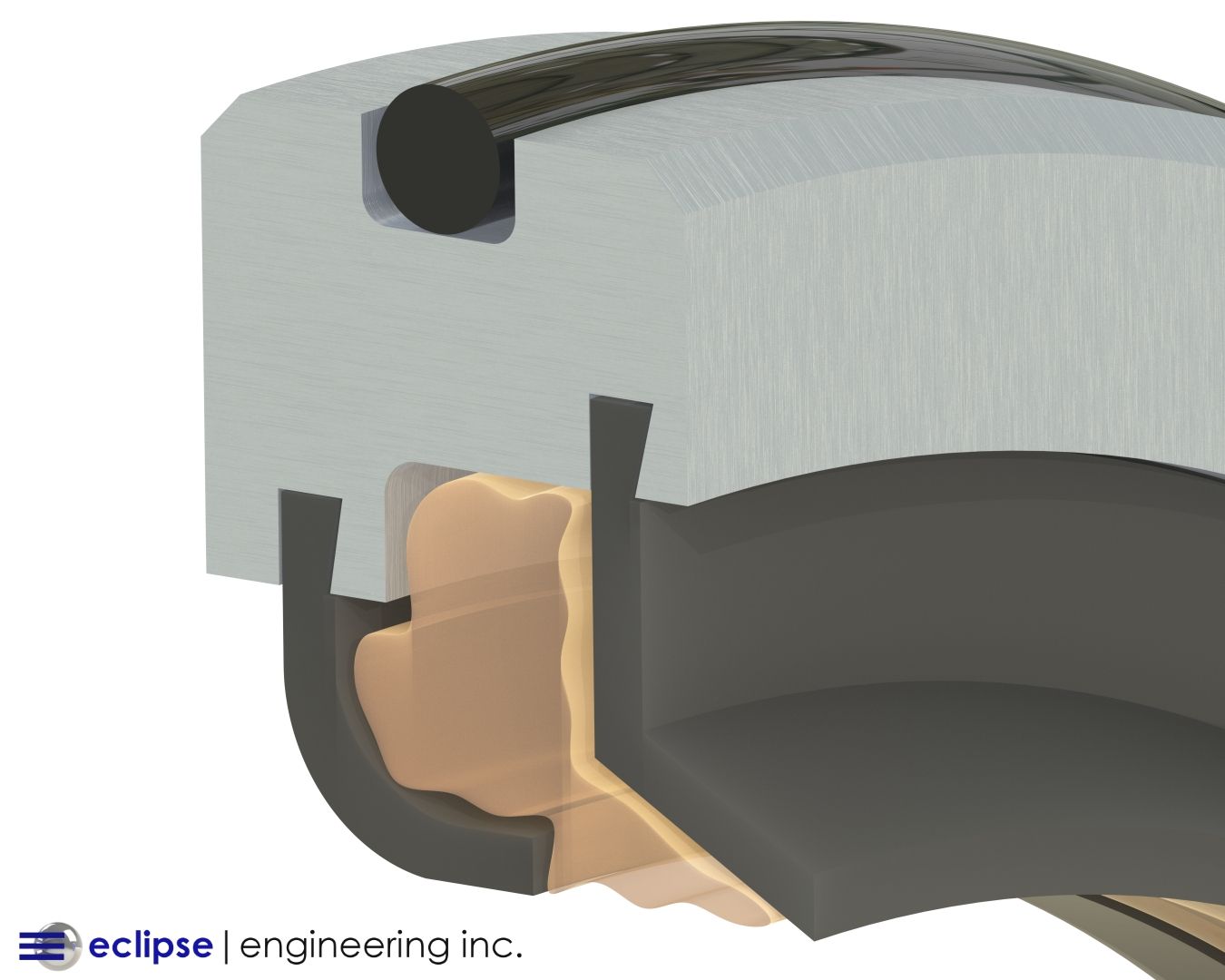