Spring Energized Seals
Spring energized seals encompass a variety of products that that can be customized to operate in a broader range of applications than any other seal product available.
This is possible due to the availability of seal jacket materials and configurations in combination with spring loads, spring materials and spring sizes. Commonly, spring energized seals are called upon to retrofit applications where traditional seal products such as O-rings, U-cups and rubber lip seals fail due to issues of chemical compatibility, pressure, temperature, friction or high speed dynamics. In these cases, Eclipse Spring Energized seals make an excellent option to increase reliability and overall product performance resulting in decreased down time and improved productivity. Eclipse Spring energized Seals are in service at the ocean depths, to the outreaches of space and thousands of applications in between.
Eclipse Cantilever Spring Seals make use of a V shaped spring embedded in a polymer jacket. At installation, the V shape of the spring is compressed, providing sealing energy to the seal jacket ensuring a positive seal. With a linear load curve and excellent deflection range, Eclipse Cantilever Spring Seals are a very versatile product. They are common replacements when rubber u-cups fail due to chemical attack, extreme temperature range, friction concerns and wear issues. Cantilever Spring Seals are best suited for reciprocating applications such as shocks, hydraulic cylinders, pumps and compressors. The shape of the spring concentrates load on the front of the seal, which makes this design also suitable for use as environmental excluders and for applications requiring scraping of viscous media. As an additional option, the spring cavity area can be filled with silicone for FDA clean-in-place applications.
Eclipse Canted Coil Spring Seals employ a specialty wound wire spring installed in a polymer jacket. The canted coil is unique in the sealing industry because of its semi-linear load curve. As an engineered loading device, canted coil springs display a very constant load over a large deflection range. This feature allows Canted Coil Spring Seals to operate in friction sensitive applications like HPLC, encoders and flap actuators with consistent performance. Seals used in battery operated devices utilize these seals – minimizing seal friction and optimizing battery life. On the other end of the spectrum, Canted Coil Spring Seals are used with heavy load springs for use in highly viscous media such as epoxies and urethanes. Eclipse maintains an extensive inventory of canted coil spring making it possible to tailor seal requirements to nearly any application.
Eclipse Helical Spring Seals are comprised of a wound ribbon metal spring installed in a polymer jacket. This helical shape spring affords a relatively high load versus deflection range resulting in a seal product that can provide very tight sealing. As a highly loaded product, Helical Spring Seals should be considered when dynamics are very slow or static. Examples are in stems seals and in cryogenic valves where additional force is required to overcome thermal effects.
In some applications, a combination of pressure, temperature and hardware gap will give rise to a situation where the jacket degrades due to extrusion. A simple upgrade for Cantilever Spring Seals is to increase the length of the seal in order to isolate the spring side of the seal from distortion. By specifying and extended heel version, pressure ratings can be doubled over non-extended designs. This can be useful in cases where rebuilds yield larger than normal extrusion gaps or when legacy designs are pushed to higher operating pressures and temperatures to achieve greater performance. Accumulators and pressure intensifiers are common applications for extended heel Cantilever Spring Seals.
Canted coil seals are often specified when less than ideal run-out and side-loading conditions are present. If these conditions exist, there is a good possibility that large extrusion gaps exist. The simplest method of increasing the resistance to seal extrusion in these cases is to upgrade to and extended heel design. The addition of extra seal jacket material protects the functioning (spring) side of the seal from distortion that may cause seal failure. By specifying and extended heel version, pressure ratings can be doubled over non-extended designs. Water jet cutting systems are often built with extended heel designs.
Helical seals are a common choice for high pressure static joint seals. As such, a simple performance upgrade to an extended heel seal can make a very big difference. By specifying and extended heel version, pressure ratings can be doubled over non-extended designs. This becomes a very useful feature in cases where pressures are so high, that gaps are created between hardware interfaces, such as in pressure vessels. These gaps can be detrimental to a standard seal. Specifying and extended heel will add additional safety factor to any design.
Flanged seals are a special class of radial seals with an added feature to help retain the seal under rotary forces. The flange is an extension of the heel of the seal, which locates in a counterbore of the housing. At assembly, the seal flange gets pinched in the housing providing a positive mechanical lock that keeps the seal stationary. Flanged seals are an excellent choice for equipment that can be designed with end plates. In these cases, assembly of a flanged seal is simple and provides a robust design as well as a level of redundant sealing on the static side of the gland. Process machinery that require a product to be contained (mixers, augers, spool valves) are good applications of this design.
When considering a rotary service seal and additional gland length is available, an O-Ring Heel Seal provides a level of anti-rotation and redundant sealing. The addition of an O-Ring on the heel of a radial seal creates a high friction interface at the bore to counteract rotary forces. With proper hardware design, a high level of sealing can be realized, making an O-Ring Heel Seal a good choice where gaseous or low viscosity fluids need to be sealed.
When considering a rotary service seal and additional gland diameter is available, an O-Ring OD Seal provides a level of anti-rotation and redundant sealing. The addition of an O-Ring on the OD of a radial seal creates a high friction interface at the bore to counteract rotary forces. Because the O-Ring is a lower durometer than the jacket material, it is more compliant and offers tight sealing on the bore. This feature is utilized in equipment such as vapor recovery and vacuum pumps where running friction needs to be low and sealing efficiency high.
Cased Spring Seals are the best option for extreme rotary service. In these designs, a metal case is constructed around the outside of a spring seal, which in turn gets press-fit into the hardware bore. A metal-to-metal press-fit ensures a tight seal as well as a highly effective anti-rotation mechanism. Because these seals are installed into open bores, they lend themselves to rotary applications such as gearboxes and power transmission systems. They can also be utilized as rod end scrapers, where exclusion of aggressive media is desired.
Face Seals are typically used in static sealing applications. Internal Face Seals contain pressure inside a vessel and are often used as lid seals or in pipe flange fittings. A PTFE Face Seal offers advantages over traditional O-Rings in terms of pressure handling, chemical compatibility, and operating temperature range. Use in cyrogenic applications is common.
Face Seals are typically used in static sealing applications. External Face Seals are often used to keep environmental media out of an exposed joint, hinge point, or pipe fitting . A PTFE Face Seal offers advantages over traditional O-Rings in terms of pressure handling, chemical compatibility, and operating temperature range. Use in cyrogenic applications is common.
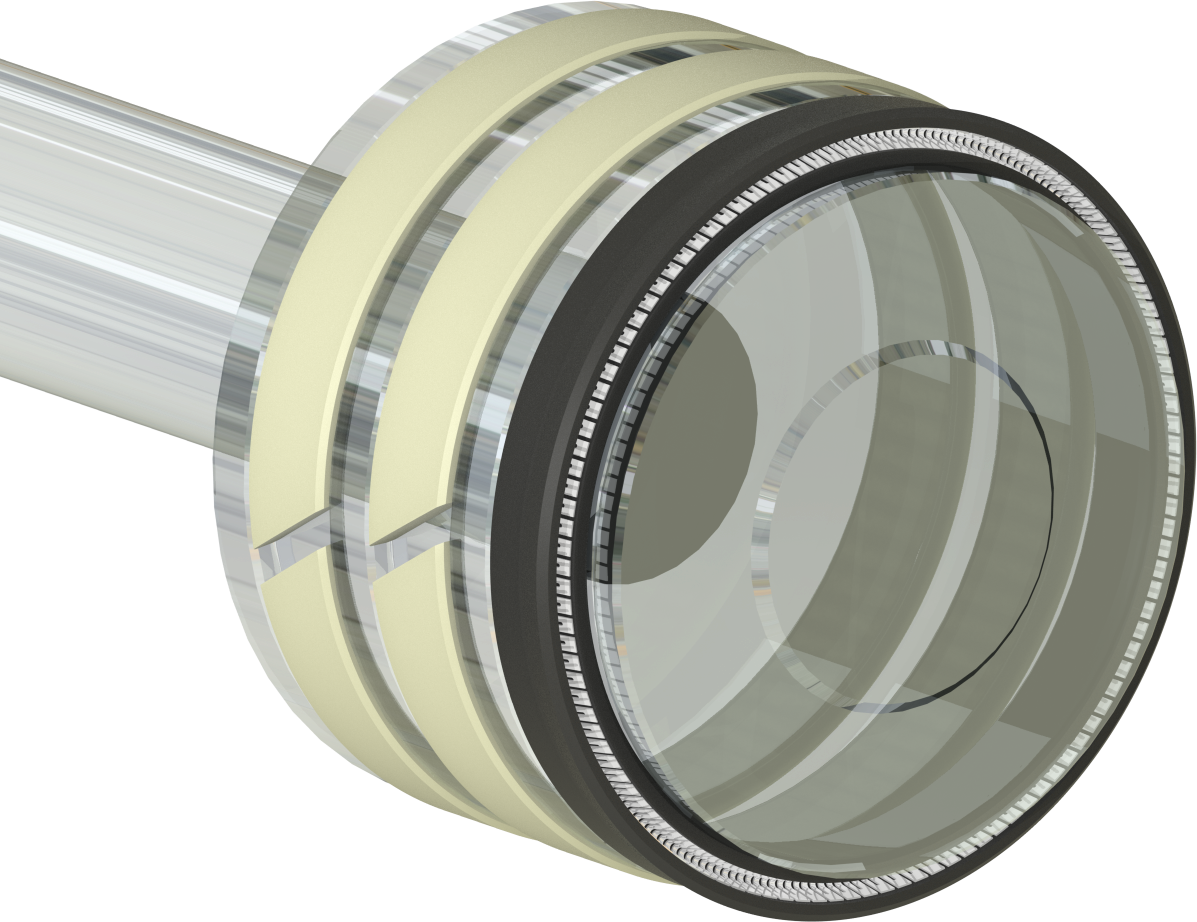
"We started Eclipse with the premise that if we could solve enough of our customers problems they would continue to come back to us for solutions regardless of the type of products we offered."
What Can We Help You With?
Start a project request form and give us the specifics of your project. Our team will review and be in touch with you shortly!