Seals Made Overseas: Is the Savings Worth It?
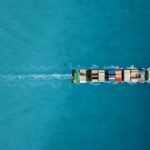
We’ve been getting quite a few calls from customers who traditionally order their seals and bearings from oversea suppliers, such as China and India. This is likely due to the manufacturing industries in these countries continuing to be impacted by the coronavirus pandemic.
We’re getting a shot a business we’ve never had before, and we’re hoping customers review the full impact of “Made in America” and how it affects their company’s bottom line — as well as all the potential issues that come with any product purchased overseas.
Is it Really Cheaper to Order Your Parts Overseas?
There’s no question that piece part pricing from overseas can generally be lower than parts made in America. That is, until you figure in transportation, duty, lead time, and the frustration that goes with encountering any problem with the part.
If you look at the landed cost at our customers’ door, we can generally compete with a higher level of quality, delivery, and technical support compared to anything coming across any border. In the end, the overall costs of ordering parts made in America is comparable.
Taking Care of Our Customers During the Pandemic
Throughout the pandemic, Eclipse Engineering continues to be fully staffed and in production. Our Engineering department has been busy working on issues that had been on the back burner in the past.
Many of the programs we’re seeing are all about a higher level of service, with deliverables tailored to our customers’ needs. Some are all about product improvement, and others are cost driven.
We’re in business to supply product made in America on your time frame. With blanket orders, we’re happy to hold inventory to handle the fluctuations in your changing manufacturing schedule. And delivers can be handled in days, not weeks or months.
How We’re Protecting Our Employees
Like the rest of the world, many of our employees telecommute. But as a manufacturer, folks need to be in the building. Their safety is always of the highest importance, especially now.
At Eclipse, we’ve always taken care of our employees by utilizing varying shifts, operating 7 days a week, and staggering hours to ensure the safety of all those involved in the manufacturing process.
The current pandemic has made us more aware than ever that taking care of our employees means we’re able to continue to support our customers’ needs — something we’ve been succeeding at as long as we’ve been in business.
We’re asking you as our customers to consider the value of having a supplier in your own back yard. For the many customers we have overseas, our doors are open for business, and we look forward to continuing to supply your product on time and at a marketable price, with the value of technical support a phone call, email or text away.
Thanks, and stay healthy out there.
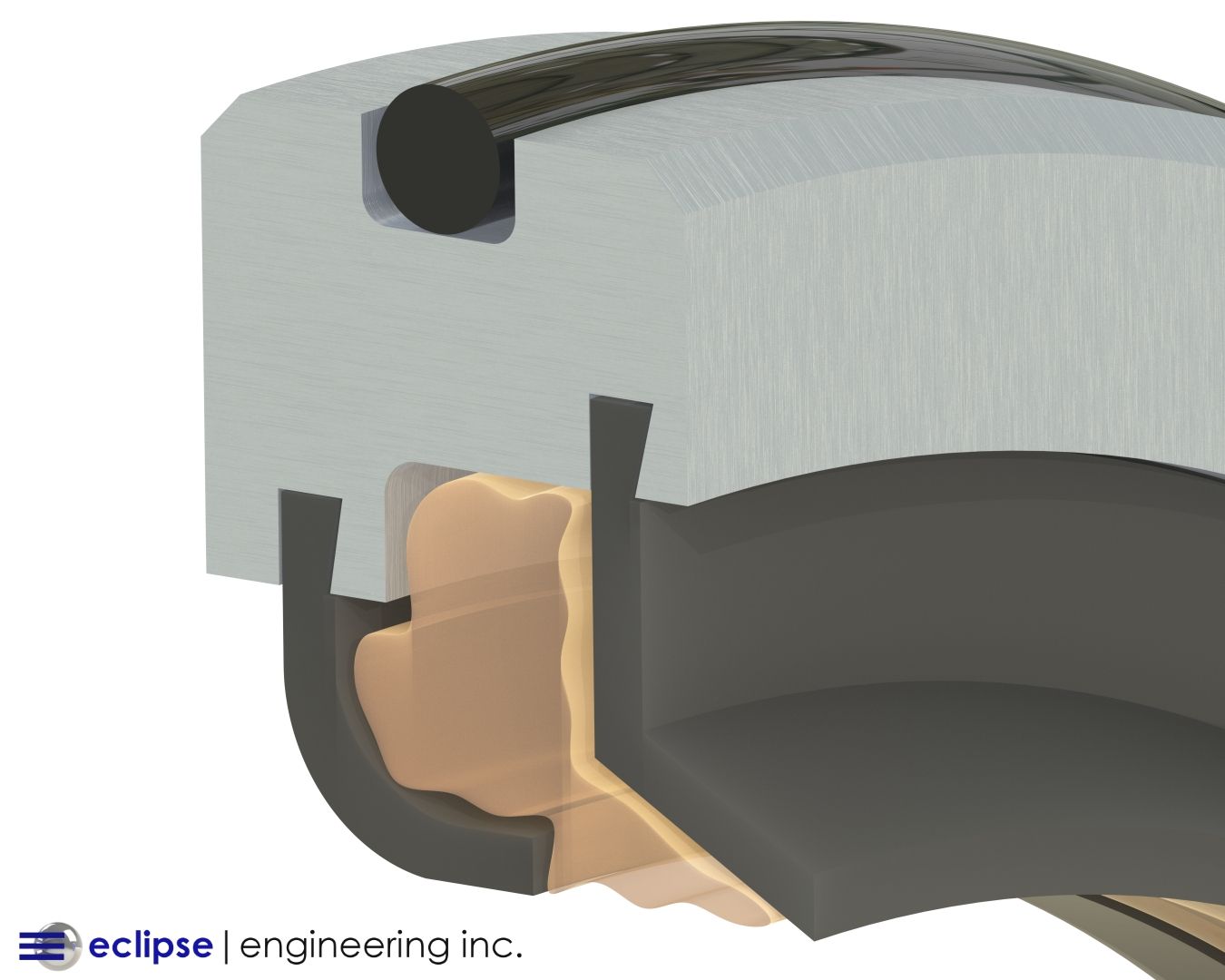