The Role of Seals in the Quest for a Coronavirus Cure
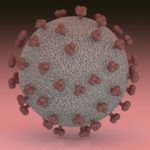
The coronavirus has prompted all of us to do everything we can to protect ourselves from catching and spreading the virus. We are all taking important safety measures to maintain a clean and uncontaminated home environment, and limiting our exposure to a potentially hazardous outdoor environment.
At Eclipse, we’ve been interested in examining the role that seals play throughout the pandemic. The very role of seals is to keep a certain environment in, and certain environment out.
We recently wrote about boundary seals in aircraft and how seals allow the aircraft to be pressurized. In the research lab, a different style of boundary seal is required to keep the outside environment out.
Labs all over the world are working toward preventing the spread of coronavirus. Scientists are working with test equipment to find a cure and a vaccine to prevent not just the spread of this virus, but other viruses which we’ve not yet seen.
When we design seals, we must consider keeping something as small as a single cell from entering a test chamber. Last week, we received a call from a customer building a prototype ventilator to be built in volume to help support patients suffering from coronavirus.
The client requested that our engineering and manufacturing team turn an 8-inch (203mm) seal around from concept, design, and finally produced and shipped in less than 4 hours — and we made it happen.
Keep reading to explore the important role that seals play in research equipment as scientists seek to find the cure for coronavirus and beyond.
Seals in Test Equipment
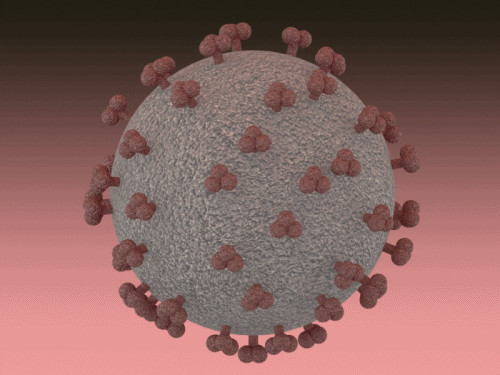
Oftentimes the lab equipment has its own environment, such as an inert gas or some other purging environment to keep the outside world from contaminating the specimen being tested. These types of seals can be static or dynamic.
Static seals are typically used to provide a barrier to the outside world and maintain an environment within a chamber. Dynamic seals, on the other hand, allow for a change in environment by changing the pressure, or allowing the flow of fluids into the environment.
This could include pressurizing the sealed-off environment to allow a further change in how the specimen reacts. The chamber itself may include seals to capture heat and cold for processing the specimen.
When we design for test equipment, we must consider not just the first test run in a chamber but ultimately many tests, so seals must have the capacity to be cleaned or sanitized.
An autoclave is often used to thoroughly clean a test chamber. The seals in the chamber must be able to withstand heat, steam and gamma radiation to insure the next test sample is not contaminated by the previous sample.
Designing and Manufacturing Lab Seals
We take into consideration all of the factors explored above when designing our seals for lab equipment. The number of seals in any order and how they’re going to be installed is considered for the purpose of manufacturability.
Lab-type equipment also often requires seals with extremely small cross section and diameter to ensure that loss of volume displacement is extremely small during testing.
Manufacturing seals to 1mm ID allows for volume displacement during the injection or titration to be extremely small and accountable. We normally use materials like Teflon or PTFE and load the seal with springs, like a Canted Coil spring , which affords us the ability to make small seals in very small envelopes.
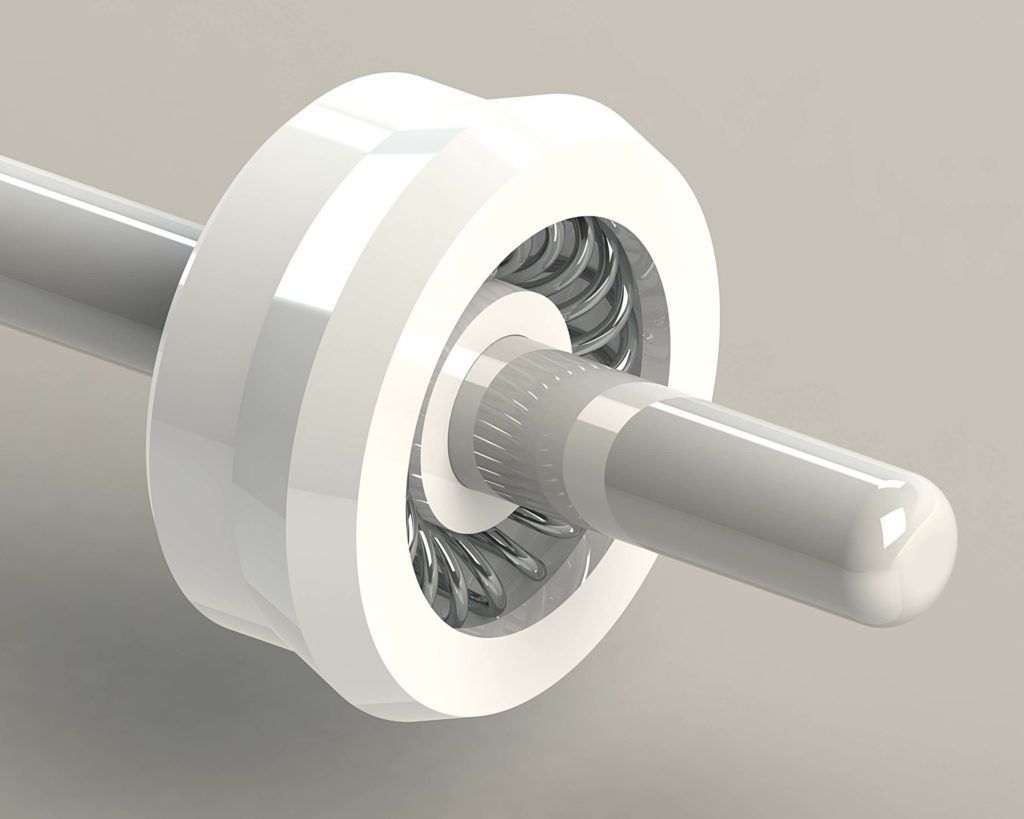
Seals like these are often found in test equipment for High Pressure Liquid Chromatography , or HPLC. These seals are often used with pistons made of ceramic. That means low friction is extremely important, as pressures may reach over 300 bar as the fluid is pushed through a filter bed.
Again, contamination of the sample is of utmost importance, so static boundary seals around the test chamber are critical to ensure the validity of test results.
Best Material for Lab Seals
These boundary seals are often made of rubber. However, when we consider the cleaning fluids, autoclave, or gamma radiation, this often makes standard rubber boundary seals unusable.
Spring energized seals can be a promising answer. Spring energized seals have extremely low porosity, and allow for metal springs which will maintain a constant force against the outside environment. Plus, these seals have no problem tolerating the operating environment along with the rigors of cleaning.
These seals are often custom-designed to support the optimal design of the test equipment. Seals can be manufactured to easily be extracted and replaced without damage to the test equipment or other seals in proximity.
Eclipse Engineering custom-designs seals for virtually every application under, on, and off the planet. But today, we’re dedicated to helping scientists all over the world find a cure for coronavirus.
Eclipse Engineering is engaged in keeping those segments of our economy such as food, pharmaceuticals, and chemical processing in place for our everyday lives to continue safely. When called to action, we’re here to support your needs.
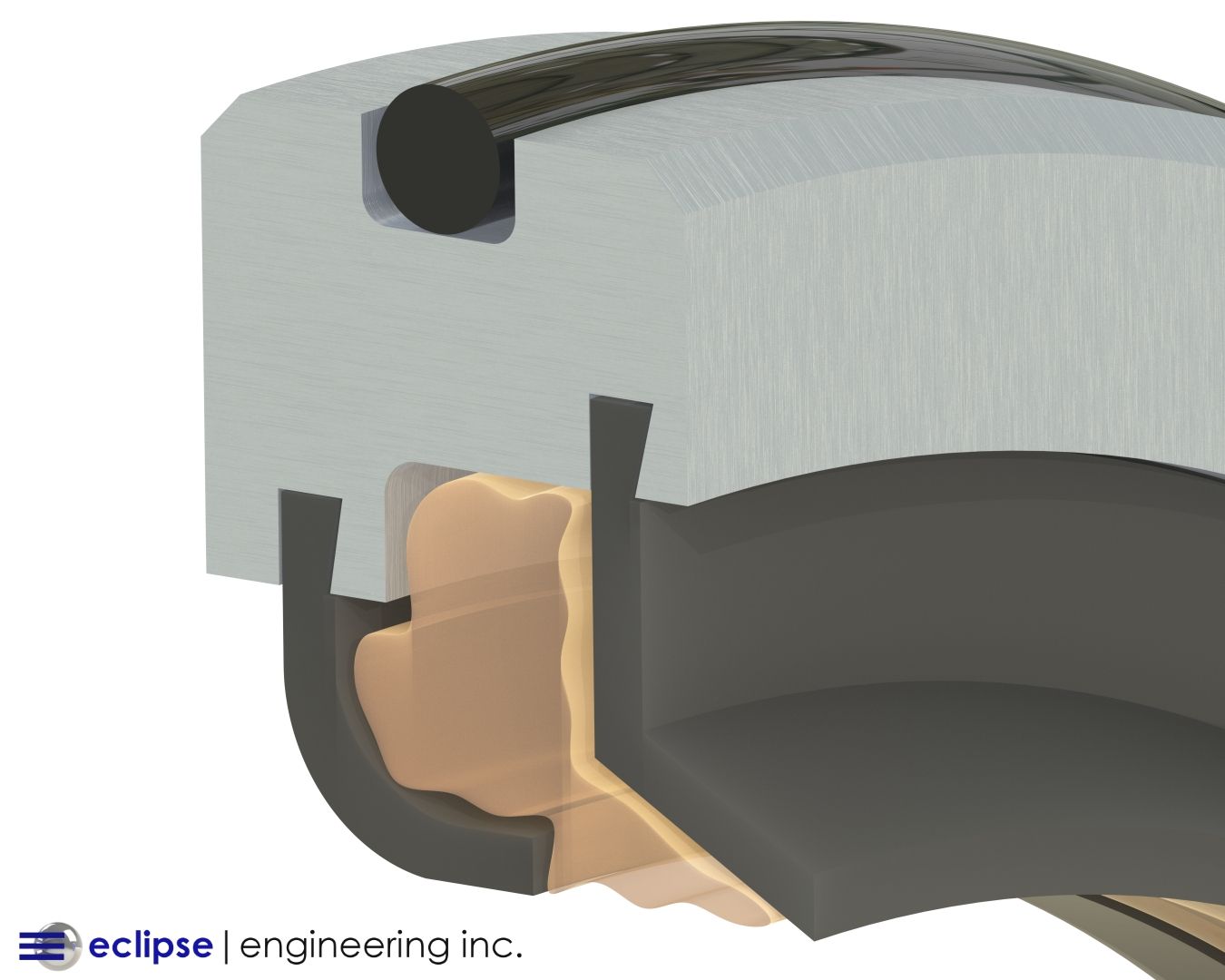