What Makes a Part Process-Capable?
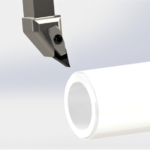
Machining plastics is as much a skill as it is an art form. It takes understanding that whenever you cut a part, it will probably have some motion or energy still within the material.
This is largely because our parts have more rebound than steel in the cutting process. And while plastics are mostly thermally stable, they’re not dimensionally, thermally stable.
Changes in temperature from the time the part is machined, inventoried, and put into service show that our parts are constantly changing in size. PTFE or Teflon suffer the greatest change in thermal instability where we machine the part, around 74 degrees Fahrenheit.
What Makes a Machining Operation or a Specific Dimension Process-Capable?
You might think that if you can make a part and verify that it’s intolerance, then the part is process-capable. But the reality is that a large tolerance range doesn’t make a part process-capable.
At Eclipse, we implement a rigorous process to ensure parts remain process-capable after machining is complete.
By measuring the parts after a run and reviewing all the critical dimensions, we find standard deviation for a dimension. We then can estimate with a high degree of certainty if, during the process, we will have parts with dimensions that will fall outside the tolerance range.
Our experience with this process helps ensure accuracy. But without doing an actual analysis based on real parts that we would run on a job, we can’t know with complete certainty if a particular dimension will be within tolerance.
One thing is certain: If you dimension a plastic part and apply metal tolerances, we will most certainly fall outside the process-capable range for that part.
Certain materials like PEEK will hold tolerance during a machining run far better that Teflon. But there are some dimensions we hold in Teflon which can be maintained to a high degree.
Usually, if we design a part with our standard manufacturing tolerances, it will certainly have a bigger tolerance range than if we design with steel. Most often, making the tolerance range smaller has little to no impact on plastic parts. Under pressure, the parts get pushed around, and are constantly changing shape to some degree.
So why bother with tolerancing at all?
We design to fit the application, so our products have to fit into the required hardware. And depending on the type of elastomer, we may need to hold tolerances on a particular dimension so the seal will perform in the entire range in which a customer wants to use it.
What Is and Isn’t Critical
When we look at why a seal preforms, the wall dimension (cross-section) generally has the most influence on success or failure. This is due to the seal being energized by either an O-ring or a spring , and the impact of the extrusion gap on the sealing system.
The width is usually the second most important factor, as the seal must be able to move freely in the gland. The least important dimension is usually the diameter. We need the seal to sit in the gland so that it can be assembled; but in general, this is the one dimension in which you’ll see the greatest change due to temperature.
Unless the application is operating in a very cold environment, the diameter must allow the seal to sit in the gland and not protrude too much for installation. Tolerances on large diameter seals (over a couple of feet) often are +/-.060 inch. This may seem like a lot, but throw in a little temperature and you find that fluctuation at this scale isn’t impossible.
How Do We Determine Process Capability?
The use of process capability calculations became common for suppliers to the automotive industry due to the large quantity of parts being made, and the need for upper-tier suppliers to know with certainty that they were getting good product.
A process capability study will tell you how likely the process is to make a good part. We won’t go into the statistical formulas in this article, but it’s enough to know that given dimensional data from a run, we can use the equations to find out a number that will indicate how likely we are to meet print tolerances.
The main index that we look at is labeled “Cpk”. The Cpk is calculated for critical dimensions using the tolerance limits and the data from a sample run. The higher the Cpk value, the more capable the process and the likelihood of making good parts.
Industry standards aim for a value of 1.33 for industrial parts and 1.67 for aerospace. In order for a process to reach high Cpk levels, the parts must be made using a small portion of the tolerance range and run at the middle of that range.
Generally speaking, a Cpk less than 1.0 indicates that the process isn’t capable, and is likely to produce parts that are out of print tolerance.
Process Capability Put to Use
How do we make use of Cpk? In practice, the machinery, tools, and processes are all known well before a part is designed. So putting a non-capable tolerance on a print will place undue burden on the inspection required to supply parts to that print.
A much better approach is to consider the capability of the process first, allow for that variation, and then design the part to accommodate the required tolerance. Having run Cpk on all our processes, Eclipse has an excellent understanding of what is process-capable and uses that knowledge to design and manufacture seals accordingly. In the case of customer-designed parts, we offer process-capable tolerancing in our quotes.
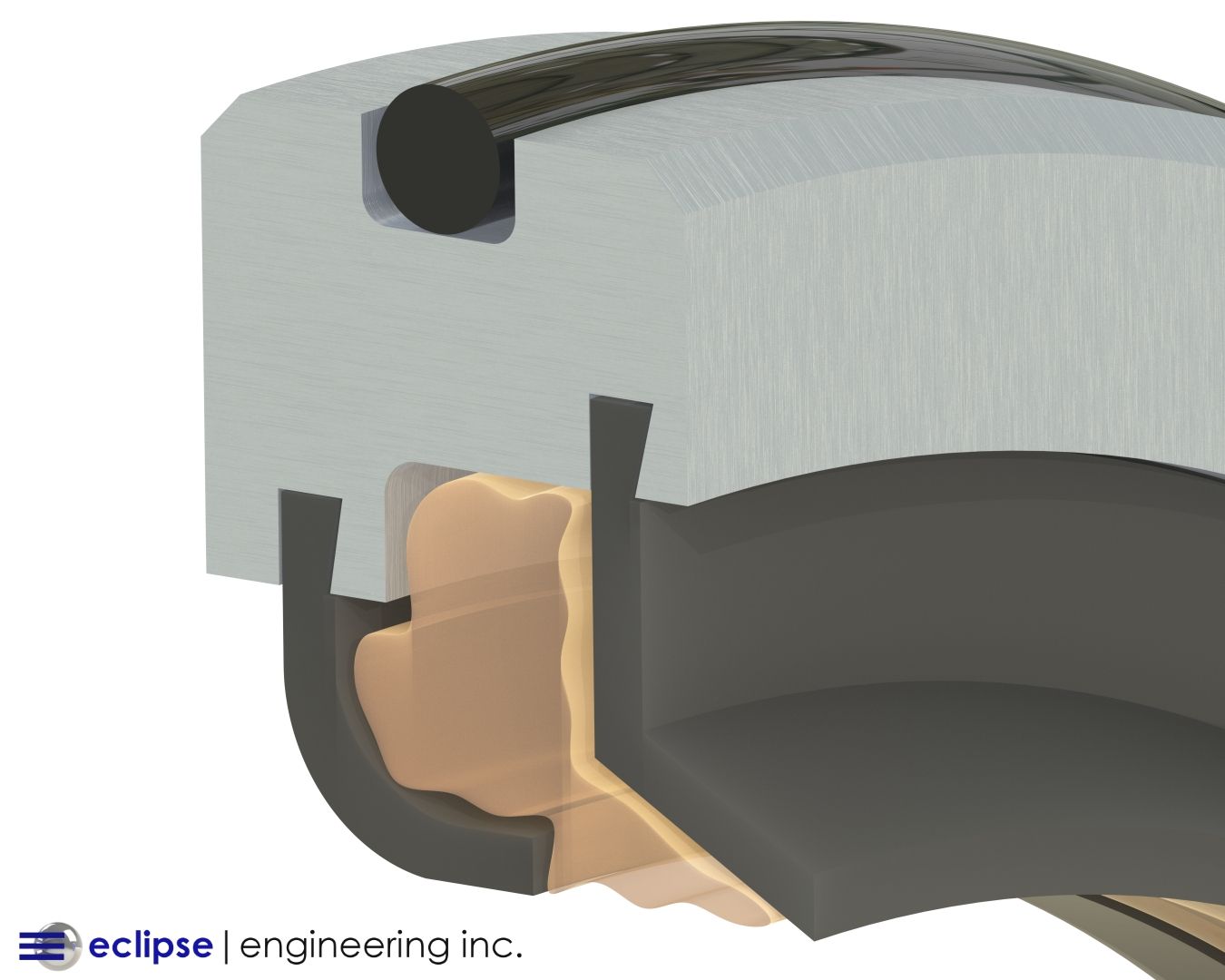