Which Sealing Materials Meet FDA Compliance?
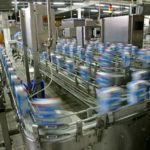
We frequently get requests from customers asking for FDA-certified materials. The FDA doesn’t approve materials, but they do approve a device which contains materials that we make seals from. These materials find themselves on a compliant list from which we manufacture seals.
The FDA doesn’t approve a material for an FDA application unless it’s specifically submitted to the FDA for approval. However, some materials have been tested in applications containing materials from which we manufacture seals.
The short list of raw materials are found to be compliant by the FDA of provided materials because they don’t react in a negative way when used in specific FDA-approved applications. These materials become compliant, meaning they were found to not react in a specific set of circumstances.
When we design a product for a food-grade application , we select materials that fall into this specific category of compliance. The reason the FDA will not “approve” any particular material is because that material may be fine when mixed with, for example, baking soda, but may be found to react violently with soda pop.
However, a piece of equipment with a seal for a soda pop application could be compliant with a totally different piece of equipment that was also being used with soda. The equipment, machinery, and process must all be considered in order to operate in an FDA-compliant fashion.
Testing for FDA approval can be an expensive proposition. Customers usually aim for compliance unless there’s a regulation that requires FDA approval.
As a seal supplier, we defer to the customer with a list of known compliant materials for use in applications that come under FDA compliance guidelines. Our customers provide information on the equipment and processes used, as well as the industry requirements. Ultimately, it’s our customer who takes responsibility for approval to a governing body.
This may seem to be a less-than-adequate position from the customer’s point of view. However, if the customer has knowledge regarding the use for their material, Eclipse can generally do the necessary research to verify compliance in a specific application.
FDA Compliant Materials
Some of the more popularly used and highly published materials that fall under FDA compliance are Virgin PTFE and any grade of unfilled Teflon, Tefzel, and TFM that fall in the fluoropolymer family.
Materials such as UHMW (Ultra High Molecular Weight Polyethylene) are also FDA compliant. Many of these materials fall under a Code of Federal Regulations. Two specific areas are 21CFR177.xxx, and 21CFR178.xxx
There are a number of urethanes, rubber products, and polyester elastomer products that also carry compliance. Most elastomers, like O-Rings , can be made to be FDA compliant.
We often use clean-in-place style seals, or CIP, in food-grade applications.
This often requires we fill the spring cavity with an FDA compliant silicone that allows the spring to continue to work without becoming filled with food substance. CIP seals are a good way to allow the operator to clean a seal without removing it from the hardware.
In rotary service, we design seals that typically are holding lubricant from gear boxes or drive systems away from the product. These seals can be built with multiple lips, keeping product and lubricant separated. Eclipse can also provide seals that are pre-packed with FDA compliant grease.
We use fillers in PTFE to help extend the wear life while not appreciably raising the coefficient of friction. The fillers also have FDA compliance. There are many fillers that work well on soft stainless shafts and provide strong sealing and long life.
The technology for sealing in areas where FDA compliance is required requires a good understanding of the intended application and goal. And while a portion of a system may fall under the compliance regulations, many components that don’t come in contact with the product don’t require compliance in the product side of the application.
Eclipse Engineering designs seals for a variety of environments that require special consideration to materials as it applies to sealing.
Bearings are always a part of any sealing system, and must be considered when designing in these FDA compliant applications. The same materials we design seals from can be used to help support hardware.
The major caveat is bearing placement — it’s important to ensure that if the bearing comes into contact with the product, it can be easily cleaned in order to maintain a contaminant-free environment. Even though a bearing may be solid, the clearances required for installation may still allow the product to migrate under the bearing, so seals must be used to protect the bearing from coming in contact with the product.
Eclipse Engineering designs and manufactures seals and bearings in environments that must meet federal guidelines or FDA compliance. Contact us to discuss your sealing application needs »
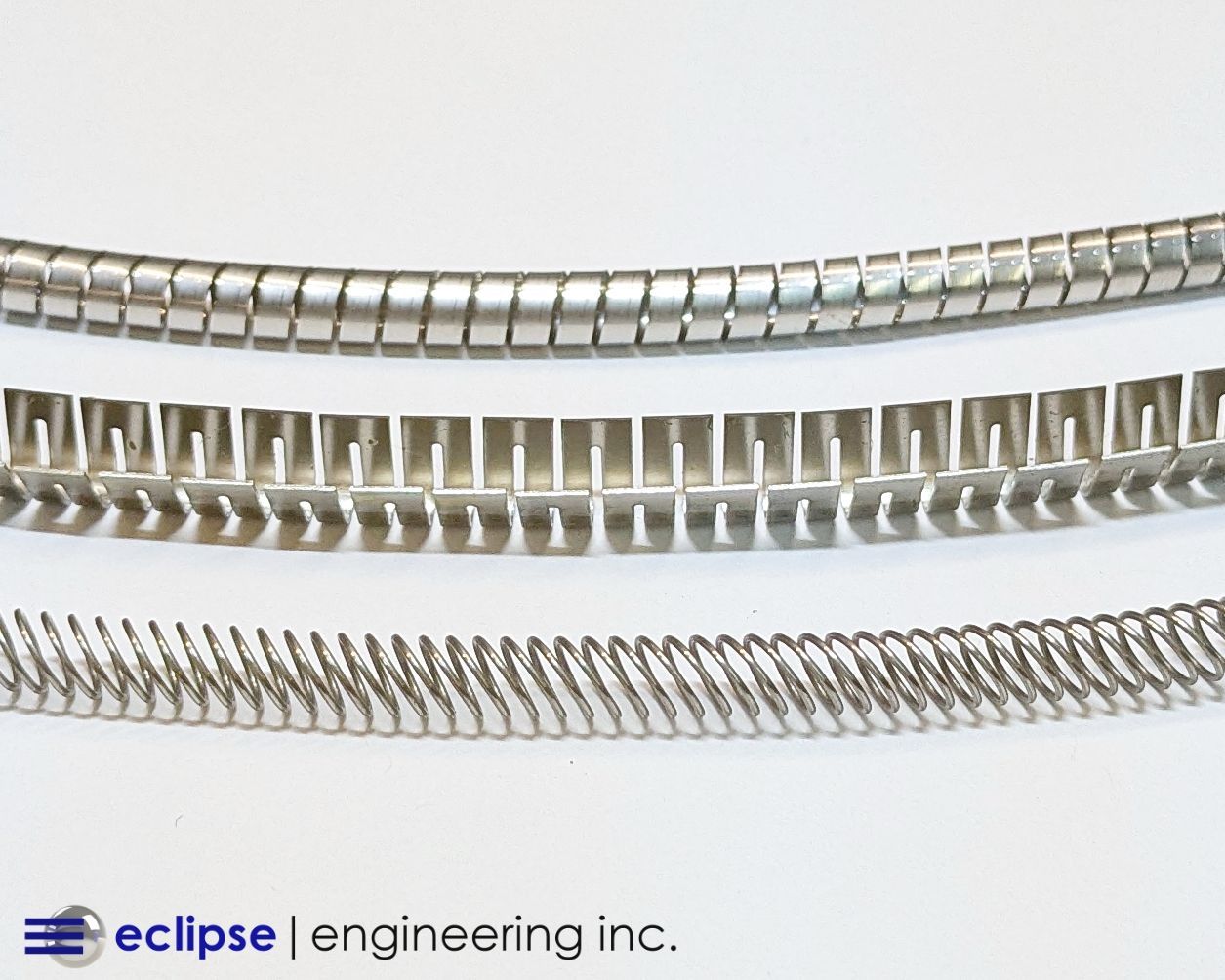