Tips for Successful Seal Installation
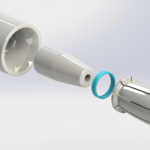
The success or failure of a seal design is often dependent on how the seal was installed. There are many seals that easily slip into glands with simple installation procedures. But when installing seals with any volume, it’s important to have an established method to ensure consistent performance of the seal.
We were recently asked to design installation tools for a 2-011 O-ring. At first glance, we would normally achieve this simply by using our hands. But when faced with 150,000 pieces, installation becomes fatiguing, O-rings get rolled rather than stretched in the gland, and the possibility of spiral failure over a large number of pieces becomes an eminent issue.
In this case, we chose to use a bullet which allowed the O-ring to pass over part of the installation that would tear the rubber. We also used an approved lubricant and a specially-designed pusher tool. The set was designed with ergonomics as a primary consideration to ensure that assembler fatigue did not become an issue.
An O-ring is a very simple case because it can easily be deformed to go into very small rod glands, and fit into most piston glands.
As a seal designer in polymers such as Teflon , Polyurethane, and rigid plastics like PEEK or Torlon require a change in the design characteristics to allow for installation. This can include special tools to aid in insertion, or special seal glands for ease in installation.
We typically avoiding polymers like Teflon because they often create the greatest challenges. As designers, considering installation into solid glands is an integral part in selecting a cross-section, along with the operating parameters of the application.
Specialized Installation Tools for Seals
Most PTFE blends will have elongations in excess of 100%, so using standard bullet tools over the piston along with pusher rings is a standard in the industry. These tools are easily designed and manufactured to allow the operator to push the ring over the OD of the piston.
A resizing tool is necessary to remove most of the stretch induced in the ring, and to re-size the seal so that it can be forced into the bore diameter. Some very thin cross-section rings may be installed in small volume by hand if sufficient care is given to not tear the ring. But a resizing tool is usually necessary to complete the installation.
With any volume, installation tools will ensure the seal is seated in the gland without damage.
Using screw drivers and other such tools will mar or damage the PTFE, so these should never reach the assembly table. In some cases dental floss can be used, if the cross-section is small enough and then resized into the gland.
In the case of Urethane or other polymers that exhibit some elasticity, the seal can often be stretched into the gland. While the possibility of marring the surface is less prevalent, care should still be taken not to damage the sealing surfaces of the seal.
Some of the piston-style Urethane rings may have very heavy cross sections, and the use of installation tools as described above is recommended.
Considerations for Installing Small Rod Glands
Rod glands, especially those with very small diameters, create a different set of installation problems. Looking first at O-rings, if you can reach into the gland, it’s usually very easy to slip one edge of the O-ring in the groove, and for rest of the O-ring to comply.
If the groove is too deep, or the diameter is too small to reach in, then a three-pronged tool can be used to deform the ring into a kidney shape, slide the seal into the rod bore, catch an edge and withdraw the tool. You would then use either an ID resizer tool or plastic probe to insure the seal is properly seated into the gland.
A Teflon ring will generally require turning the part into a kidney shape either in your hand or with the use of a three-pronged tool, and then sliding the seal into the seal groove and withdrawing the tool. In the case of Teflon-style rings, it’s often required that an ID resizing tool is required to gently massage the ring back to it’s round shape removing the bends produced by putting it into a kidney shape.
Tricks to Successful Seal Installation
For polymers like PTFE or Teflon, heat is powerful in softening the material to make it more pliable. The rings usually need be heated up to several hundred degrees.
Boiling water in a microwave is an effective way to soften the ring. The rings will cool very quickly, so application must be done immediately.
Where lubrication is allowed, this can often help the more elastic seals find their way. This can also be helpful even for Teflon. The only issue in the use of lubricants is that your fingers are now lubed as well.
In the process of resizing, we often put assemblies with seals on them in the freezer to help them collapse down, then install them into a bore.
Our Seal Installation Process
We are often asked to aid in developing an installation technique. We normally start with the tricks just to see what’s possible. But in general, the development of a set of installation tools normally ensures a repeatable assembly process, with no damage to the seal.
We normally design a set of tools for one application, and rarely make more than one set. This alone drives the cost of tools and why we often avoid them. However, when you consider the time spent without the proper tooling and the possibility for damaging the seal, it can be an inexpensive solution in the long run.
We didn’t discuss installing Spring energized seals in solid glands because this is rarely done due to how easy it is to damage the lip or deform the cross section. This can be done in rare cases, but typically the seal is installed into two-piece or stepped glands.
Eclipse designs and manufactures installation tools for most seal applications, as well as taking a customer’s hardware and designing methods for installation. We are constantly improving tools and methods for installation.
We are also always looking for ways to improve our customer service and lead-times. Discover how we maintain minimal lead time with every seal »
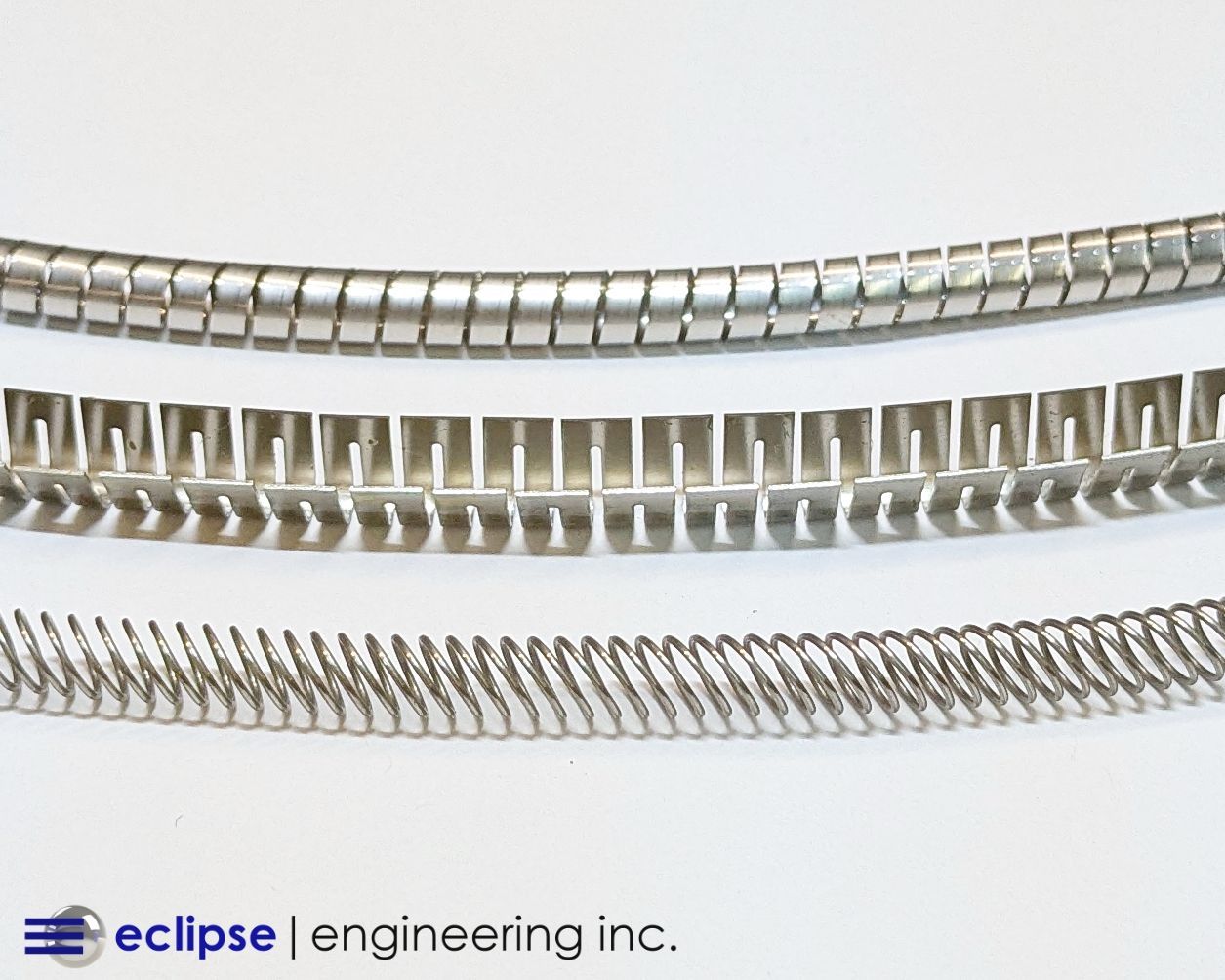