How We Design a Seal from Start to Finish
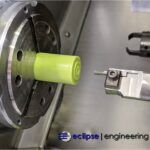
We recently wrote about processing PTFE, or Teflon, from the drum of raw material to a finished rod or tube. But what’s involved in creating a seal from inception to completion?
We receive literally hundreds of requests a month for a seal or related product. Some never get past the inquiry stage, as the clients’ need doesn’t fit our specific products. In those cases, we may locate a source or suggest an alternative to what they’re looking for.
But there are many other cases in which we have the capabilities to fulfill our customers’ specific needs.
Below, we’ll outline the steps we take to turn our customers’ ideas into a finished part, along with the unique challenges brought on by COVID-19 and the adjustments we’ve made to stay on schedule.
Step 1: The Sales Department
A typical request will start out in our sales department, where the salesperson determines the best course of action based on the information the customer has supplied.
The better the information, the higher the probability that the first designed product works for the client.
Step 2: The Engineering Department
The idea then travels to our engineering department, where the idea is put on paper (electronically speaking). A price is generated based on annual usage, along with prototype pricing.
This package is then presented to the customer for evaluation. Customers generally have many questions at this stage, which are generally handled by the salesperson and/or the engineering staff.
Step 3: Ordering the Prototype
Once the package has been approved, it’s time to order the prototype. Our goal is to keep the part as close as possible to a production part.
On a machined part, this is usually a simple task. But for a part that may require tooling in production, we’ll often machine a part that may get stamped in production. This keeps cost down, but doesn’t exactly mirror production.
At this stage, we prepare the final manufacturing drawings, along with production routing to ensure we mirror a production process. Materials may need to be specially ordered to fill the prototype order.
Lead times are then set, and the job traveler is printed with all the required steps. During this process, a quality audit is conducted to ensure the sales order is complete, and correct documentation for the order is staged while the order is being processed.
Step 4: Receiving Raw Material
Once we receive the raw material and verify the quality records, the material then goes to the floor where it’s matched up with the job and traveler.
The job is placed in que with the material and any special tooling for the job. When the job comes up, it’s matched with the material and flows to the floor for production.
We review the quality paperwork to ensure we have all the data we need to properly process the product. Finally, we set up the machine and run the first article, along with paperwork validating conformance to the customers’ requirements.
Step 5: Running the Job
At this point, we’re ready to run the job and create the product. We complete any final paperwork (including any inspection paperwork), and parts either go to shipping or to second operation for the addition of coatings, a spring, etc.
The same quality paperwork is completed at each process to ensure each step is complete.

Step 6: Shipping
The finished product moves into shipping, where we once again complete the proper quality paperwork, along with a review of required customer documentation.
We may need to consider special packaging needs as the product is prepared for shipment, per the customer’s requested method. The package is equipped with a shipping label, a packing slip, and any other documents required by the customers receiving department.
Step 7: Invoice and Scanning
Finally, the order moves to accounting for invoice and scanning.
Scheduling Issues During COVID-19
Since the onset of COVID-19, we’ve had to deal with many scheduling issues due to our employees being exposed to the virus, or their children’s schools going virtual (requiring employees to stay home and look after their kids).
This year, we’ve also received an increase in expedited orders from customers at a rate we’ve never seen before! While our doors are rarely closed, the challenges around navigating the virus in addition to extra expedites have tasked us with finding ways to stay on schedule for our clients.
Changes to Expedited Orders in 2020
We always leave room in our schedule for expedites, as we understand some jobs are more critical than others.
There are 2 major components to expediting a job:The first is that we must receive the raw material quickly. The second is that all the other jobs that were in place prior to the expedited order are shifted back.
To stay on schedule, we’ve been working overtime to keep all our clients’ orders moving forward.
We’ve been employing machines that are more cost effective to run for particular jobs. Running on a machine that is less specific usually slows the run rate, thereby increasing cost of the part.
Keeping Our Customers Up and Running
Our goal is to always ensure our customers’ equipment continues to operate without interruption.
When a production order arrives, the job has already been planned, programed and routed. All that’s left for a long running job is raw material and scheduling.
In a perfect world, we would run the prototype exactly the same as the production part, using the same equipment to run the job. But a new customer requires a slightly different cycle, as there’s usually some accounting on the front end to open an account. And more importantly, there’s more time spent on the back end when it comes time to ship.
Learning the habits of a new customer generally takes a few cycles. We understand that by properly packaging and shipping your product, we can make the acceptance of your parts to go much smoother.
Improving Our Production Processes
On top of all the challenges of 2020, we’ve been working to improve our production processes with better techniques and special equipment meant to help run a particular job.
And in the background, we have a staff ensuring we comply with various regulations and with ISO 9000, which was implemented over 10 years ago.
Our entire system is based on what we can do to make the entire seal design process as seamless as possible.
Over 20 Years of Seal Design Experience
Design is at the center of everything we do here at Eclipse Engineering. We realize parts don’t simply fall into your hardware.
When your parts do arrive in the mail, we’re ready to help with installation, including designing specialty tools customized to meet your hardware needs.
We’re often on the front line explaining what we feel is the most cost effective method to install in production. If you ever have any questions about your parts or design, you can always give us a call.
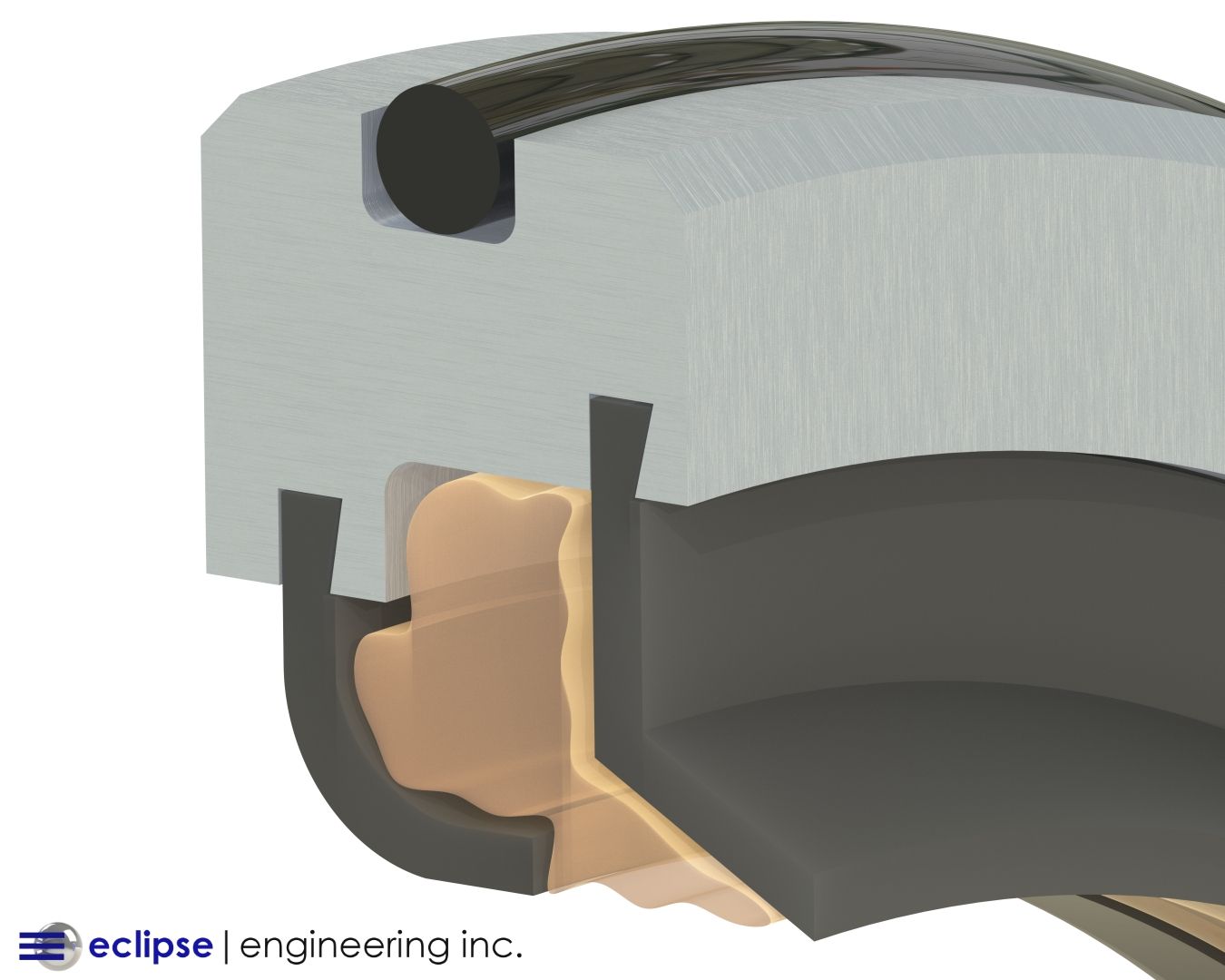