Crimped Case Seal or Componentized Design?
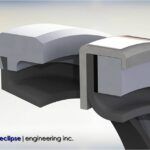
If you have an application with a rotating shaft, you likely need a seal. Rotary shaft seals often take the form of what is commonly known as an “oil seal.”
These usually consist of an elastomeric sealing lip, with a molded-in-metal case to facilitate a press-fit into the hardware.
Oil seals are typically mass-produced, and are usually available from stock in a variety of sizes. They function best in oil-lubricated environments, such as engine crankcases or gearboxes. But in dry running applications, you may need a PTFE-based sealing element.
In addition to not needing lubrication, PTFE lip seals provide a number of advantages over elastomeric oil seals. PTFE’s ability to handle much higher temperatures means higher rotational speeds can be achieved.
High-wear fillers can be added for much longer service intervals when compared to elastomers. Friction characteristics will also be far superior therefore lowering torque requirements.
As more and more modern applications turn to electric motors rather than internal combustion engines, the need for low-friction, dry-running rotary shaft seals is growing.
Most motors require an environmental shaft seal to keep dust, water, and debris from entering the internals.
There are 2 main designs for incorporating a PTFE seal element into a metal case. The first is what Eclipse calls their Crimped Case Seal (CCS). The second is the more traditional componentized design.
Both have pros and cons. Below, we’ll discuss what applications might better suit one design over the other. With the ability to offer either design, Eclipse is here to provide you with the best solution possible.
The Crimped Case Seal
In terms of seal history, the crimped case seal, or CCS, is a relative newcomer, entering the market about 10 years ago.
The crimped case seal’s hallmark design feature is that it can use as little as 2 components: the sealing lip and case. This is in contrast to a traditional design that usually requires 4 components to accomplish the same task.
A CCS functions by having the seal element slip into a small groove in a machined case. The groove is then crimped or compressed to positively engage the PTFE for both internal sealing and element anti-rotation.
This eliminates the need for an internal gasket element, affording maximum temperature handling, and chemical resistance.
The seal lip can be any one of Eclipse’s PTFE blends. Eclipse can tailor the material selection to optimize the goals of the system.
The case can be either Aluminum or Stainless Steel, but Aluminum will provide more size options and typically cost less.
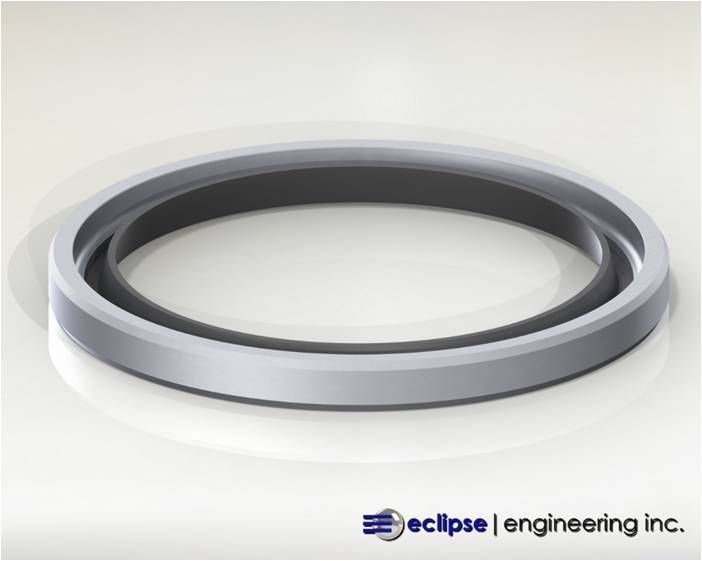
Pros of the Crimped Case Seal
Other than fewer components, the CCS has some key advantages over a componentized seal.
First, the case of a CCS is CNC machined. This means the highest tolerance control and no expensive first-time tooling costs.
This can significantly improve lead-time compared to operations requiring tooling or dies. The crimping of the case is a simple procedure that can be done quickly on a press, rather than a more complicated forming procedure done on a lathe. This can further expedite lead-times and run rates.
The seal lip itself is also machined into its final shape. This allows for precision interference control and eliminates the need for the forming and shipping of the seal on a separate mandrel.
There are some limitations to the CCS though. While there are some great advantages to machining the seal case, this can also be a drawback in high volume applications.
The componentized design will have the option of stamping or rolling, forming the metal constituents from sheet stock, which greatly reduces unit cost.
Cons of the Crimped Case Seal
There are some size restraints to the CCS as well.
It’s not possible to install a lip into a case much smaller than 1.5.” On the upper end of things, it’s difficult to find raw metal tube stock in diameters above 12 inches with limited options above 6 inches. It might not be practical to machine a case with an OD in this range.
With these aspects in mind, the CCS is best suited for low volume, and/or quick turnaround applications with shaft sizes from 1.5 to 5 inches. Eclipse also successfully employs crimped case seals in very torque and friction sensitive applications, such as robotics.
Precise control of the lip profile and interference is necessary to provide smooth and accurate movement and seal volumes are relatively low. Prototyping seals without tooling costs is also a plus for numerous design iterations.
The Traditional Componentized Design
The traditional lip seal design has been around for decades and has seen service in countless applications and industries.
In the most basic form, it consists of are the outer metal case, the PTFE sealing lip, a thin elastomeric gasket, and a spacer ring.
The components are stacked and a small portion of the outer case is rolled over, usually on a lathe, to compress and permanently hold everything together.
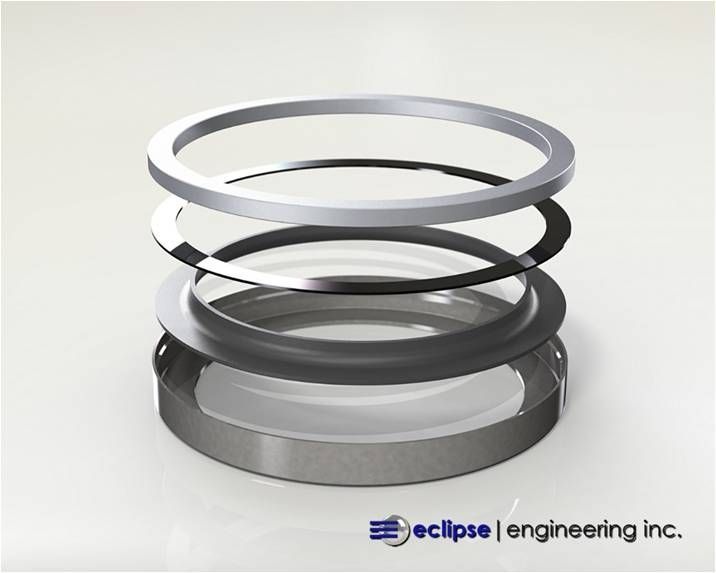
The sealing lip can be any of Eclipse’s PTFE blends. It’s machined and assembled simply as a straight, flat disk. This means quick run-rates during machining and minimal raw material usage aiding in low unit costs.
The lip must be formed after assembly. Typically, this is done by pushing it on a cardboard mandrel that is just under the shaft diameter.
Cases and spacers can be Aluminum, Stainless Steel, or cold-rolled steel. Stainless steel is the most commonly used outer case material, and Aluminum is typically used for the spacer.
The gasket serves to provide some spring force to compress and hold the components, but also internally seals the inside of the case. It’s usually made of standard O-Ring-like materials, such as NBR and FKM. The use of specialized high-temperature reinforced NBR is also common.
Pros of Traditional Componentized Design
The chief advantage of this design is the ability to economically mass-produce the components. In particular, the metal components can be stamped from sheet metal.
This of course requires die tooling, which can cost thousands of dollars. But at higher volumes, the tooling costs are usually easily amortized, and the resulting unit costs are a small fraction of a machined component.
For slightly lower volumes, spin forming the case and spacer is an option. This involves forming a flat disk of sheet metal over a mandrel while be spun on a lathe.
While still requiring tooling, it’s often much less expensive than stamp die tooling. Spin forming is often used to form large-diameter cases, where raw billet stock is not available or practical for machining.
Eclipse Has You Covered
Both the CCS and traditional rotary lip seal have advantages and disadvantages, and specific application parameters will determine which design is best. The volume of seals needed will be one of the largest deciding factors in which is best for your specific project.
Eclipse can design and manufacture either seal from volumes of one to tens of thousands. We have full design and manufacturing flexibility in whichever option fits your needs.
Unlike some suppliers, Eclipse won’t obligate you to choose only one solution. We have many customers with legacy applications that use the traditional componentized design, but they may only need a handful of seals every year.
We’re happy to machine every component, and to avoid any tooling costs. Contact us today with your rotary lip seal needs >
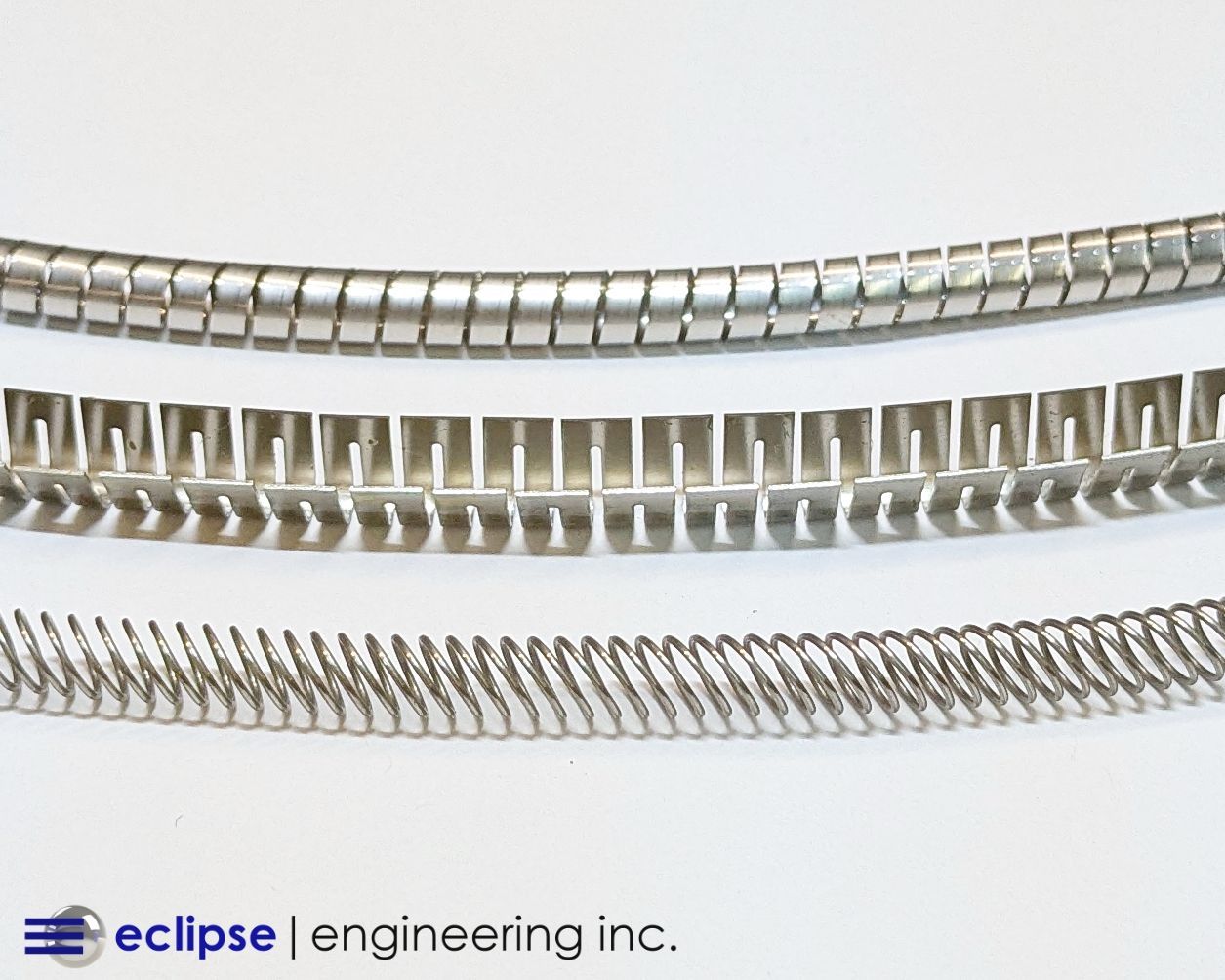