What You Should Know About Pressure-Velocity (PV)
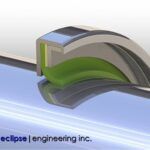
When it comes to designing dynamic seals, the two most important application parameters are the pressure and the speed of the motion. These two factors chiefly determine the type of seal, design geometry, and seal materials you should choose.
When dynamic speeds and system pressures become elevated, determining the life expectancy of the seal becomes an important point of analysis. A seal that’s low friction, cost-effective, and seals outstandingly are useless if it only lasts a few hours before wearing out.
To quickly gauge the feasibility of a seal’s performance and provide a baseline metric, seal engineers use a calculation called Pressure-Velocity (PV).
Female Fitness and Bodybuilding Beauties: Tasha Star – Fitness Beauties tren hex half life side effects stopping steroids, side effects of anabolic steroids in bodybuilding – noudoc.com – website info judi online kartu indoinesia Below we’ll explore what PV is, how it’s calculated, and what makes it an important tool in seal design.
What Is PV?
Simply put, pressure-velocity is the product of pressure and velocity. In other words, the pressure of the system is multiplied by the surface speed of the dynamic seal interface.
To produce a value that’s consistent for comparison throughout the industry, the units used to express the pressure and speed are important. In the US, pressure is always calculated with PSI and surface speed in feet per minute.
The first step in calculating the PV is determining the surface speed of the system. In a rotary application, the diameter of the dynamic surface and RPM are needed. In reciprocating, the stroke length and cycle rate are required.
Once the surface speed is known, simply multiply it by the system pressure.
Example PV calculations:
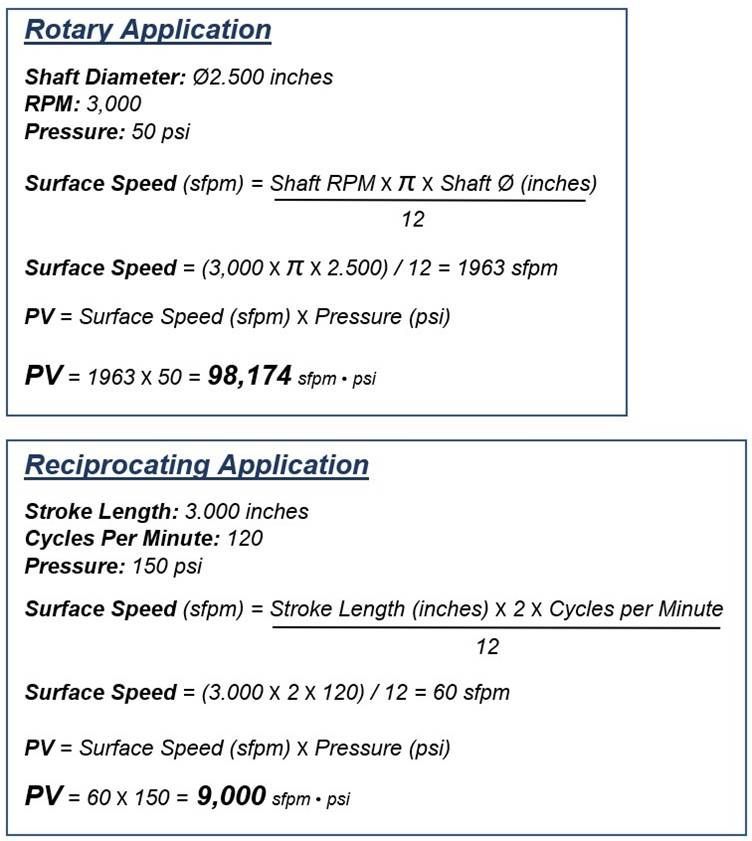
Why Is PV Important?
PV is used as a quick gauge of the plausibility for the success of a sealing system in a given application. The exact value itself is not of tremendous importance, but it provides a relative idea of the stress and projected wear life of a seal.
How fast a seal will wear is a function of both the surface speed and pressure of the system. Sanding a piece of wood with some sandpaper serves as a good analogy: You’ll wear away more wood by either sanding faster or pressing harder. Doing both results in the maximum wear rate.
This is essentially what happens at a microscopic level to a sealing element. High pressure and high-speed result in a high wear rate. Once a sealing lip or element is severely worn, positive contact with the sealing surface will be lost resulting in leakage.
In high-pressure applications, structural integrity of the seal might also be compromised.
So assessing wear rate potential of a system is important.
PV considers both pressure and speed to provide a practical and quick evaluation for reference.
PV Values
PV is generally not discussed until values become elevated. It’s most often used for rotary applications. While pressures in reciprocating applications can be quite high, it’s much more difficult to generate significant surface speed, unlike rotary applications.
PVs of less than 30,000 would be considered mild and most typical catalog sealing solutions should operate at nominal performance and life expectancies.
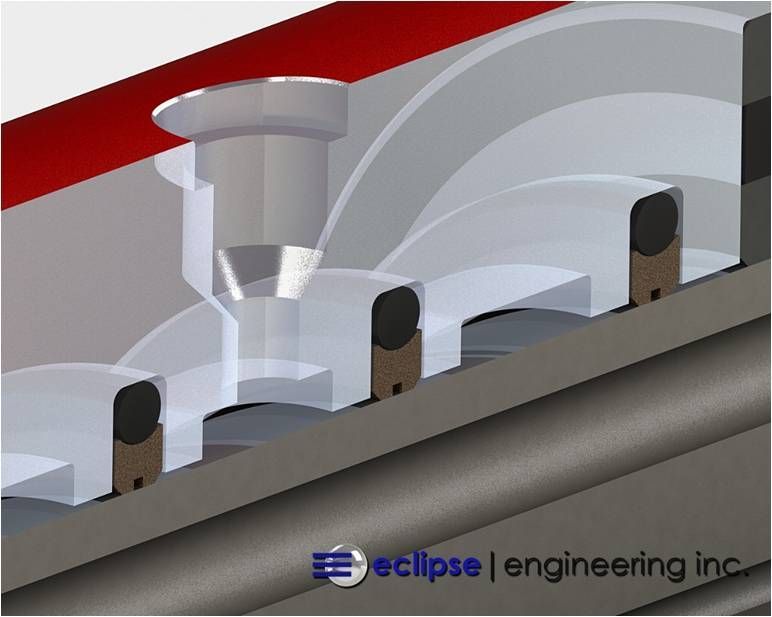
The most referenced PV limit is usually 100,000. At this value, the transition between nominal wear and high or severe wear occurs.
There are many application-specific factors that will determine the PV limit of a system.
Temperature, lubrication, hardware finishes, and runout all contribute to the wear limit of the sealing system. A PV of 100,000 is not simply the end of the story — it’s typically the value that will get the attention of any seal designer.
A PV of greater than 200,000 is of immediate concern. This is considered the “severe wear zone” for a seal operating in those conditions.
If a customer presents Eclipse with a sealing application with this kind of PV, further discussion about the life-expectancy goals of the system is in order.
Eclipse has designed and manufactured successful sealing systems for PVs as high as 300,000. But at these levels, what one customer considers successful might be very different from another. Wear life of a seal under these conditions will likely only be a few hours.
Not All PV Is the Same
Clever readers might have realized that it’s possible to produce the same PV through different combinations of pressure and velocity. As demonstrated below, three very different operating and application parameters can all generate the exact same PV value.

This is important because the optimum type of seal in each of these situations will be totally different. A seal cannot be chosen based solely on PV alone.
Here’s a look at the different applications for PV pressure and the best seals to use for each:
High RPM, Low-Pressure Applications
Cased Lip Seals
, Crimped Case Seals
, and MicroLip
are typically best suited. Their light loading means low friction and long wear life. These are typically found in gearboxes and as electric motor shaft seals.
Medium RPM, Medium Pressure Applications
Cased Spring Energized Seals , O-Ring Heel , and O-Ring OD Spring Energized Seals are best suited for this application. When pressure exceeds the limits for rotary lip seals, but surface speed is in check, these can be a good choice.
Eclipse’s in-house manufactured Canted Coil spring is usually employed for precise friction control and consistent loading.
Low RPM, High-Pressure Applications
Rotary Seal Rings are the seal of choice. Standard designs can handle pressures up to 4,500 psi. A specialized friction coating is applied to the O-Ring/Seal interface ensuring anti-rotation. These seals are often found in rotary unions transmitting hydraulic fluid or air.
Pressure Velocity Further Explained
Determining the pressure velocity of your application is integral to its success and the lifetime of the seal you’re using. By gaining some basic background on PV, you’ll be better equipped to work your way through the seal design process.
Eclipse’s team is dedicated to finding the right sealing solution to every application and educating others on the inner workings of the seal industry.
Our Engineering Manager, Chris Gruner, gives a quick math lesson on how to calculate pressure velocity. Once you understand how it works, it can be a quick and valuable way to decide what type of seal is needed.
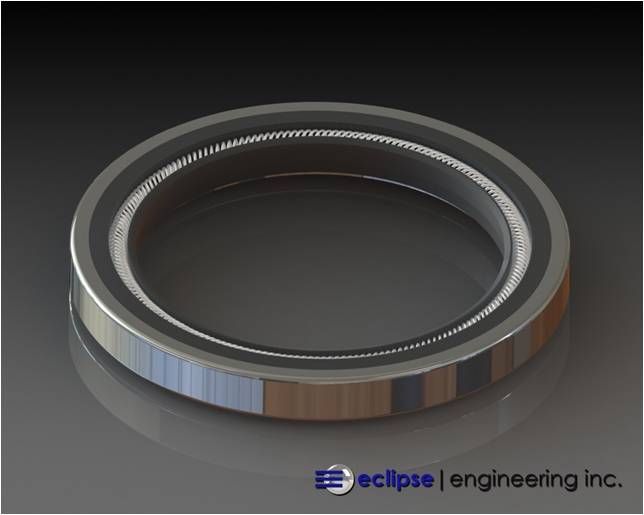
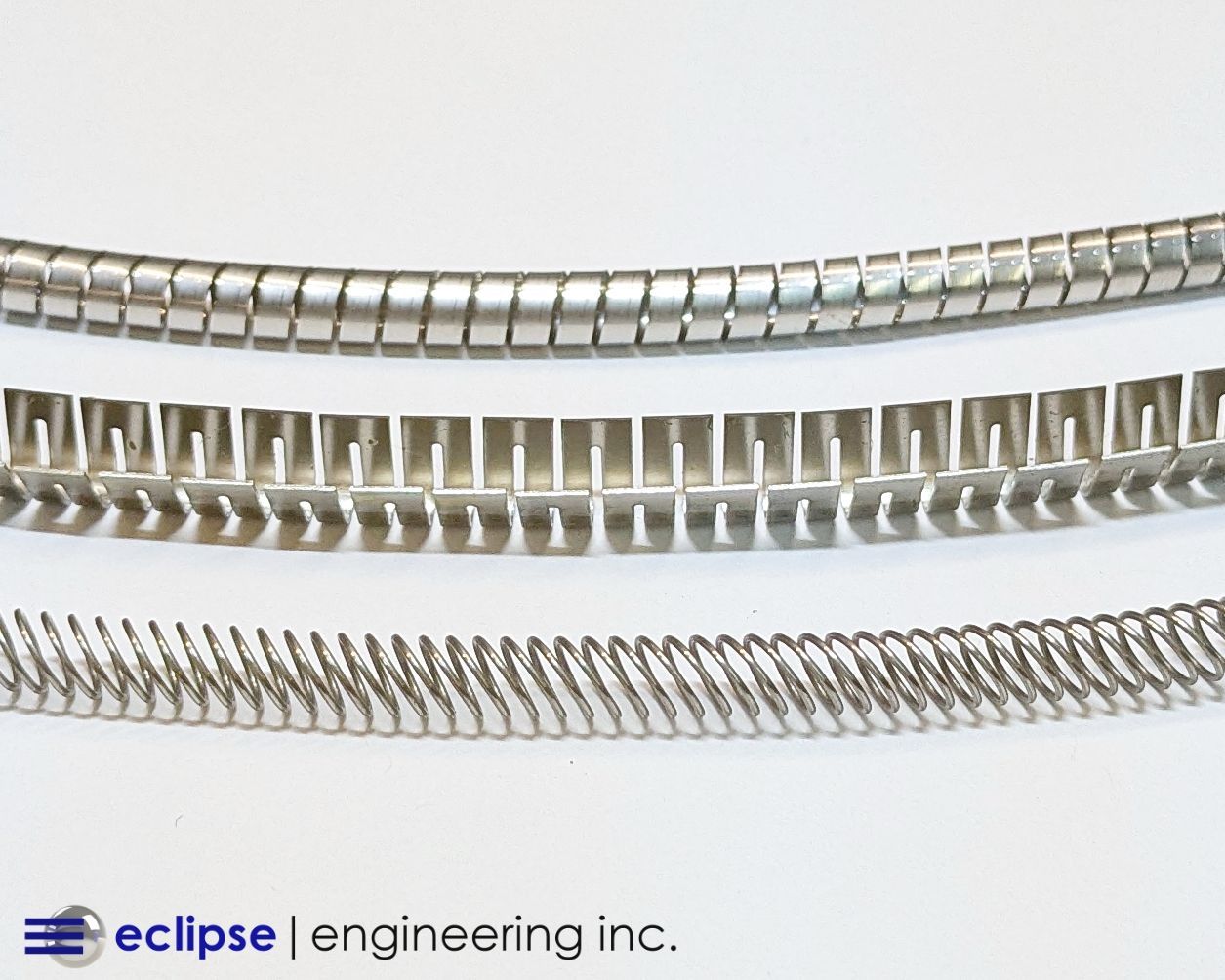