How Surface Finish Affects Sealing Performance
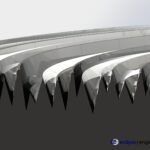
Picture this: You have an application using a standard O-Ring. The O-Ring seals great, but is wearing out very quickly, and friction is far exceeding the goals of the system.
You retrofit a fancy PTFE spring energized seal that costs 1000 times more than the O-Ring…only to find out it leaks!
Did you get a defective seal? Is the seal designer incompetent? Is the raw material bad?
Actually, everything about the design and manufacturing of the spring energized seal could be perfect, and you could still find yourself with leakage.
While blaming the seal might be your first instinct, the leakage in fact, could have nothing to do with the seal itself, and everything to do with the surface finish of the hardware it’s trying to seal against .
How is Surface Finish Defined?
If you’ve seen an image of a seemingly-smooth surface under a high-power microscope, you know that what looks flawless to the naked eye can actually be full of peaks, valleys, cracks, and imperfections.
These microscopic features of any surface are particularly important to sealing performance. Surface finish is a complex and in-depth subject that has many facets of analysis to describe the texture or topography of a surface.
In the world of seals, surface roughness is typically used to describe the finish condition of a sealing surface. The Roughness Average ( Ra ) value is most commonly used parameter, expressed in micro inches or micrometers. The lower the value, the smoother the surface.
Ra is generally used for historical or traditional purposes and not for merit as it doesn’t do the best job of fully defining a surface. It leaves the possibility of a surface with high peaks and low valleys to still average out to a reasonable number. (Though it might be implied within most modern finishing techniques that this would be an undesirable and unacceptable condition.)
These peaks and valleys are really what matter to the sealing performance, especially when using polymer-based seals. These are the microscopic gaps that the seal is responsible for closing off.
Why Surface Finish is More Critical for Polymer-Based Seals
If you’re accustomed to using O-Rings or elastomeric-type seals, hardware surface finish might be considered an afterthought. In many cases, a “as machined” finish will be perfectly fine for an O-Ring to seal against.
An O-Ring is much softer and more compliant than PTFE and most other polymers. A rubber like material can easily conform to rough and uneven surfaces to provide effective sealing.
While PTFE might be considered a relatively soft plastic, it’s still many times harder than most O-Ring materials. Rather than “squishing” into a microscopic gap in the surface to seal it, a harder material will merely bridge the imparity creating a leak-path.
In most cases, surface finishes intended for an O-Ring will result in unacceptable leakage when used with a PTFE or Polymer based seal.
What Surface Finishes are Recommended for Polymer Based Seals?
Surface finish requirements will largely be dependent on the media to be sealed and the dynamics of the system.
Recommendations for a static seal that’s meant to work in peanut butter will be very different from a reciprocating valve sealing liquid oxygen.
Below is a table with standard recommendations based on some common media and dynamic situations. These recommendations should provide a general idea of the surface finishes needed, but please consult us for application-specific suggestions .
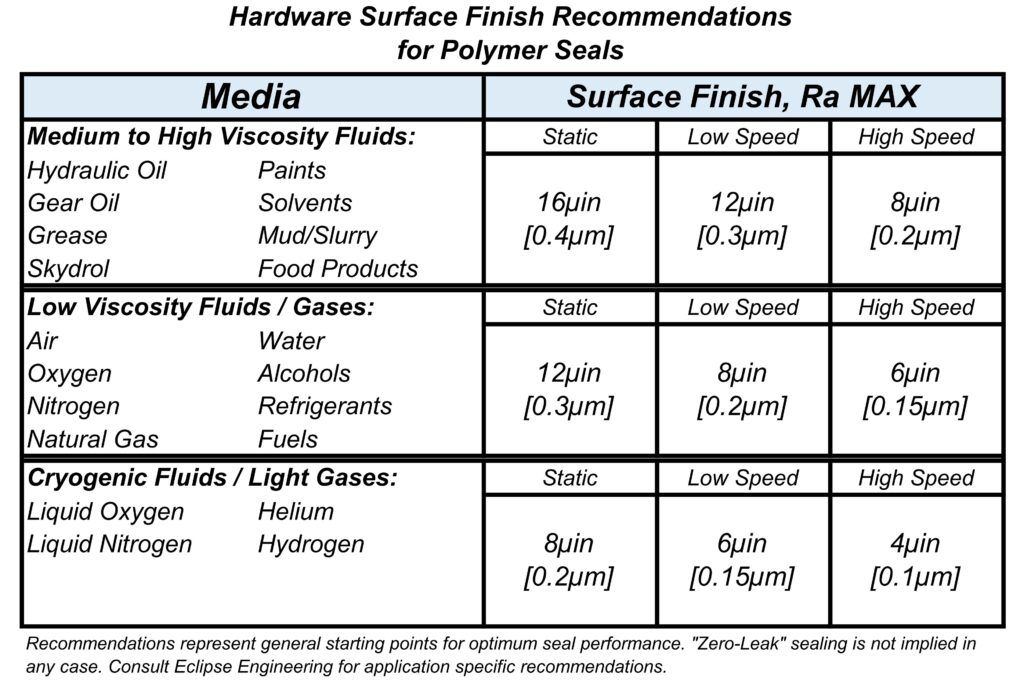
It’s important to note that the best surface finish that can be achieved from a typical turning machining process is usually a 16µin Ra. In many cases, it won’t be better than a 32µin.
Milling operations can result in even poorer finishes. Cast surfaces are also unlikely to have finishes better than these.
This is important, because aside from sealing a very viscous media in a static situation, an “as machined” or “as cast” surface finish is likely not going to be sufficient for a polymer seal. Some form of post process surface treatment will be necessary.
This will involve processes such as grinding, honing, polishing, and lapping just to name a few. These procedures can add significant cost to hardware.
Depending on the configuration, polishing the inside of the groove deep inside a housing may be very challenging. It’s usually easier to get better finishes on rod surfaces rather than bores.
Therefore, given the option, it’s typically better to keep the dynamic sealing surface on a rod or shaft.
What is Acceptable Leakage?
It’s important to note that surface finish recommendations can vary greatly depending on specific applications. Surface finishes may need to be more or less stringent based on the leakage goals of the system.
While any polymer seal will likely never achieve a “zero leak” situation despite the best surface conditions, it can be expected the better the finish, the tighter the leakage control.
This is not always the case when using a O-Rings where the finish is too smooth, and can actually hurt sealing performance and significantly increase friction in dynamic situations.
Generally, with any PTFE or polymer-based seal, the finishes “can’t be too good.”
But as stated earlier, achieving highly polished surfaces in certain hardware configurations can be very costly. It’s up to you to determine if the cost of achieving these finishes is needed to meet the goals of the application.
Eclipse has many customers who use finishes that are much worse than recommended because leakage isn’t a critical aspect. For example, a customer constructing a standard air cylinder might typically use O-Rings for all the primary seals.
In special cases where the operating environment temperature is too high for O-Rings, they use an Eclipse PTFE Spring Energized seal . In this circumstance, improving the hardware finishes isn’t necessary, because slightly more leakage only results in a small decrease in operating efficiency. This is deemed acceptable.
On the other end of the spectrum, finishes might need to be much better than recommended in critical sealing applications.
For example, a Spring Energized Seal used to contain cryogenic propellants on long term space exploration missions. Any leakage here represents a mission limitation and liability.
In this case, special techniques and materials might be necessary to provide the best finish possible.
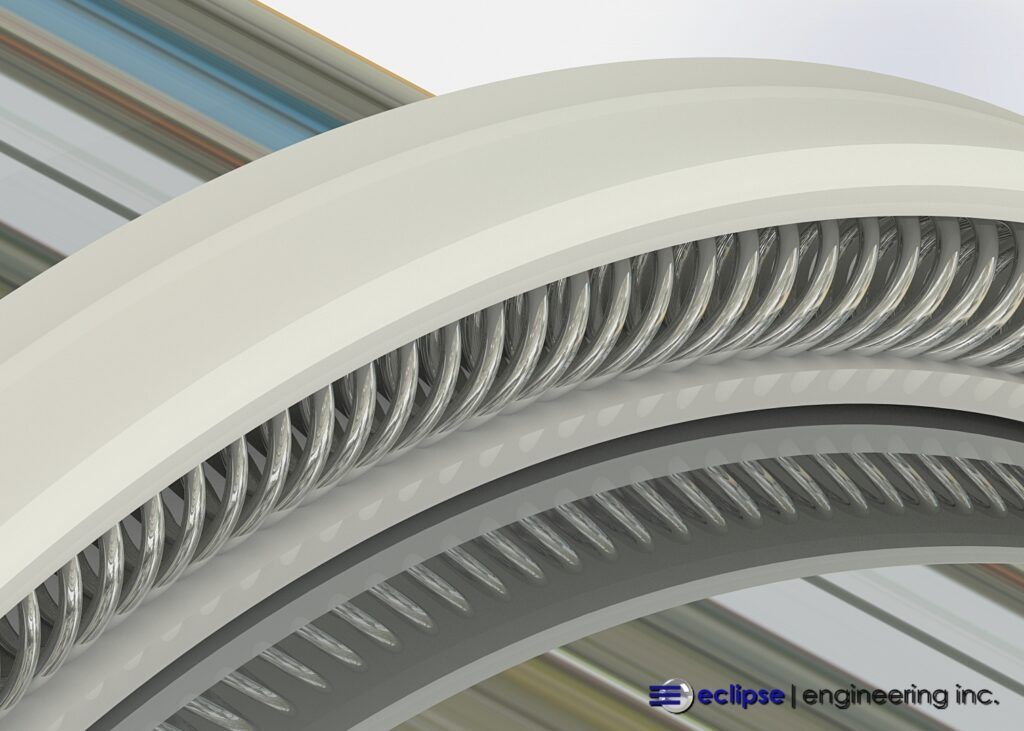
Eclipse Is Here to Help
Eclipse understands the implications of requiring polished surface finishes and that these kinds of operations are not always possible. We’re here to utilize our vast selection of seal materials and our decades of experience in seal design to provide a solution to even the most challenging applications.
For example, Eclipse had a customer looking for a seal for a large, heavy chamber door. The groove for the seal was a milled surface and it would not be practical or even really possible to remove the door and perform a polishing process to improve the finish.
By careful seal material selection and unique design characteristics, we were able to provide sealing solution that met their leakage requirement goals.
While recommendations are there for guidelines and starting points, they are not necessarily the end of the story. Contact Eclipse today to put our advanced knowledge base and manufacturing expertise to work >
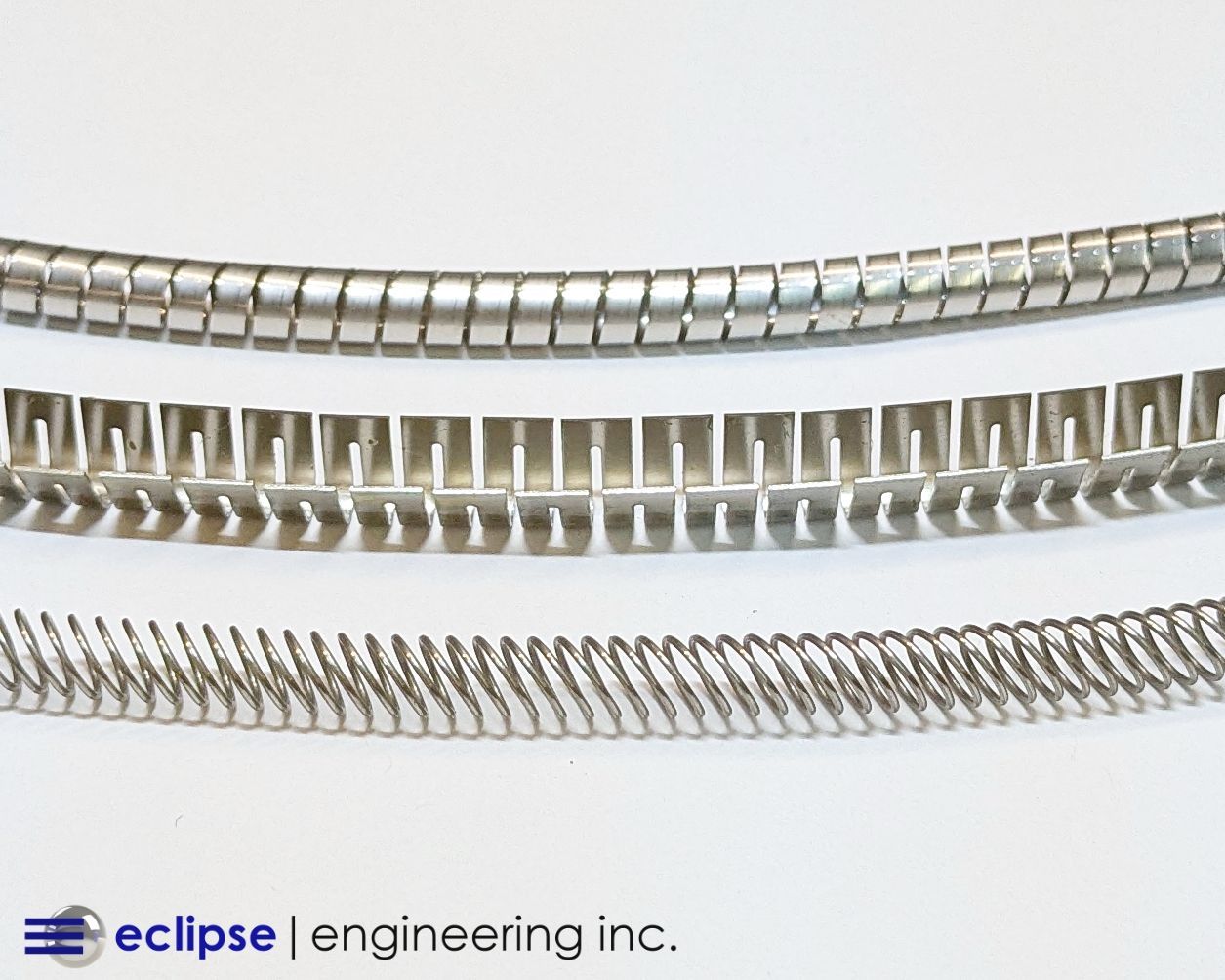