The Best Uses of UHMW Seals and Bearings
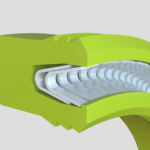
Ultra-High Molecular Weight Polyethylene , or UHMW, is an inexpensive easy to acquire seal material which, in the right environment, provides an excellent seal.
There are a set of operating criteria designers must follow to take advantage of the many benefits that other materials like PTFE can’t offer.
In this article, we’ll explore the uses of UHMW, how and where to apply it, and the pitfalls to avoid.
What are the Best Uses for UHMW?
UHMW is used in a variety of seal and bearing applications.
As a bearing, UHMW is used in many linear applications with both oil or dry environments. But it’s especially useful in low-load water applications, as UHMW will “wet” due to its hydroscopic nature in water.
Materials like PTFE are hydrophobic, meaning they tend to shed water. This causes water or aqueous solutions to be abrasive to materials like PTFE.
Here are a few most popular uses for UHMW seals and bearings:
Guide for ski gondolas
- UHMW is often used as a guide, and can be used as skid plates for things like guides in gondolas at ski areas, or where ever sliding wear occurs.
Low-load cylinders
- In low-load cylinders, UHMW is often used in both air and water environments for guiding rods and pistons.
- Again, in aqueous solutions, UHMW tends to wet and improves sliding friction.
Spring energized seals
- UHMW is an excellent spring energized seal material. It’s often found sealing air, water, and abrasives.
Sealing paint
- When sealing paint, which has solids, UHMW wears better than most other sealing materials as the solids do not cause the UHMW to break down at the sealing interface.
- Due to its structure, it’s a very rigid plastic and holds an edge, so it scrapes better than most other polymer-type seals, like PTFE.
Air cylinders
- Even in air, UHMW has a relatively low coefficient of friction. It’s commonly used as the main piston seal in air cylinders.
- UHMW is a low-cost material, and is often found in low-cost cylinders where an O-ring creates too much friction.
Joint replacements
- In medical applications, UHMW has been used in joint replacement.
- As UHMWPE also has good biocompatibility, it’s commonly used as a prosthetic material, particularly as bearing surfaces in hip and knee replacement.
- Extended exposure to gamma radiation breaks the long polymer chains shortening the life so repeated sterilization is harmful to the material.
We typically don’t use UHMW in rotary applications due to high loading, and the creation of localized heating which can quickly distort the material and reduce its ability to seal.
However, in very slow rotary or oscillatory applications, it can provide an excellent seal in the correct environments.
Installation Considerations for UHMW
UHMW has little memory, so stretching during installation can be a problem.
Typical spring energized seals are normally installed in two-piece glands or stepped glands.
With the proper interference, this material can act as a scraper as well as seal to keep systems clean in mild abrasive environments.
We see spring energized UHMW seals in a variety of applications, such as pump seals in two-part adhesive systems, or pumping two-part urethane into the mixing heads.
They are also often found in air cylinders where an O-Ring provides too much hysteresis or friction in the motion of the cylinder.
Guides in water or seals where glycol or aqueous solutions are the media cause UHMW seals to be the material of choice.
UHMW must be properly supported or it tends to yield or “smear” over a surface if it’s too heavily loaded. Also, it has a stringent temperature limitation of below 160F with brief excursions, and light loads to 200F.
UHMW machines easily, which keeps costs down. But in small parts the chips can create a problem due to the stringiness of the material.
Improving the Life of UHMW
To Improve UHMW against wear resistance, certain additives are available to extend the life of the material.
Some of the fillers include surfactant to improve lubricity, or yellow dies which improve wear. Ceramics which can also extend the life of UHMW by as much as 10X.
In the correct applications, UHMW provides an excellent seal material — especially against solids or aqueous-based solutions at medium temperatures below 160F.
As a spring energized seal, it provides excellent scrapping ability, and a very positive seal.
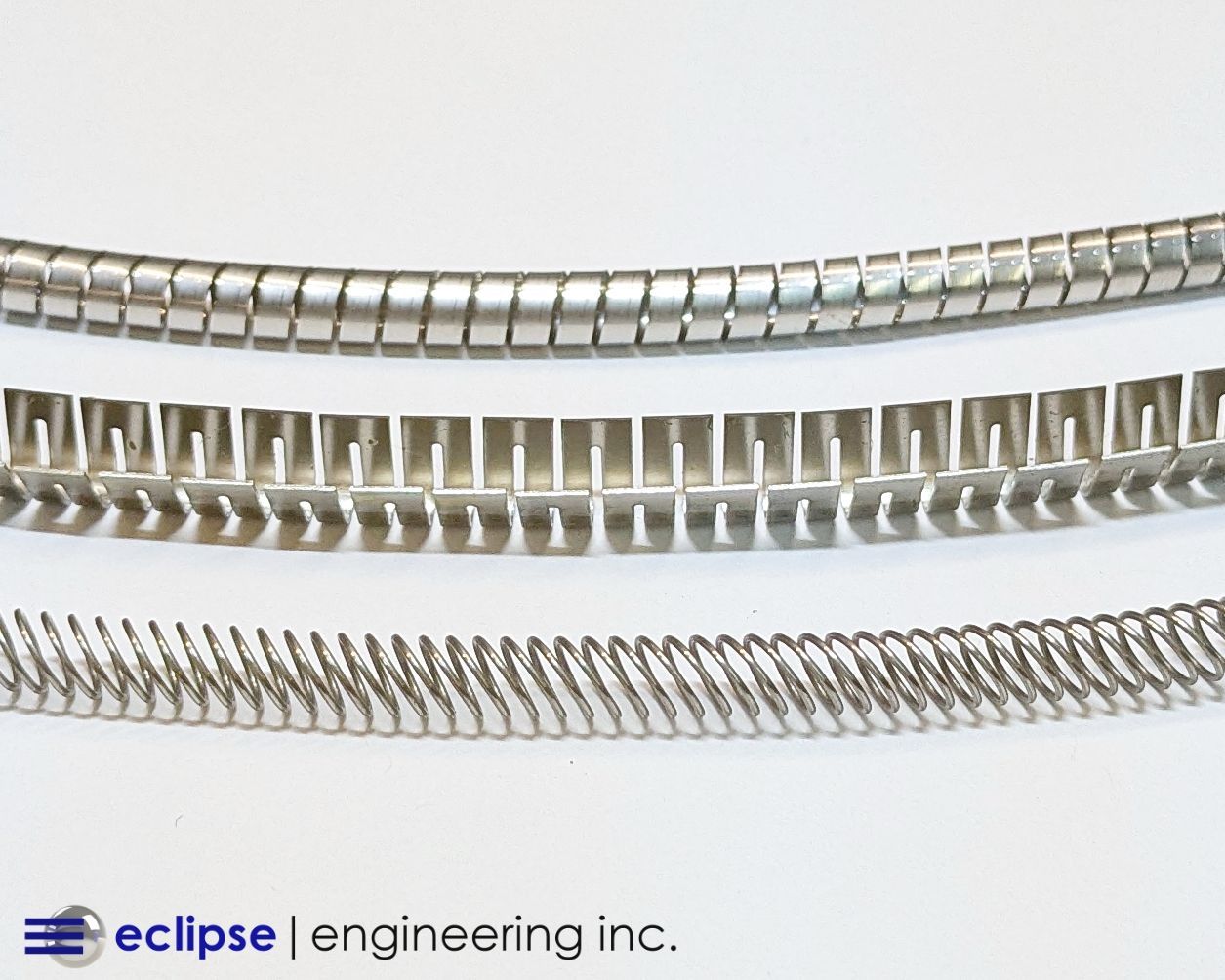