Benefits, Features and Best Applications for Torlon
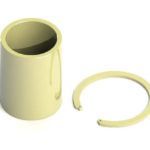
Torlon® polyamide-imide is one of the highest performance thermoplastics that is still melt processible.
Torlon can be extruded into shapes and injection molded into custom geometries. With a 500°F heat distortion temperature (softening temperature) and a 500°F continuous service temperature, Torlon allows for usage at elevated temperatures while maintaining its strength.
It’s stronger at 400°F than many other engineering resins at room temperature. Torlon is also tougher and more impact-resistant at cryogenic temperatures than other high strength polymers.
Its properties are the result of being transformed from a thermoplastic to a cross-linked thermoset during an extended curing process.
Glass-reinforced and carbon fiber reinforced grades offer even greater stiffness plus enhanced thermal expansion properties.
The various wear grades of Torlon offer unmatched performance over a wide range of temperature and PV values. *
Our Applications of Torlon
We apply Torlon to many applications that can be structural or as a part of an assembly with a PTFE-style seal.
Its ability to resist distortion under high temperature makes it an ideal material for under the hood componentry.
We’ve made snap rings from Torlon allowing for a retention method in a high temperature application where installation will not scratch or abrade the bore as a typical metallic snap ring would upon installation. This allows for the finish to remain in tact for sealing a gas.
Because Torlon is easily machinable, we’ve manufactured complex shapes operating in a wide temperature range as seal carriers with internal porting.
Torlon is used at higher temperatures for backup ring devices where PEEK is well beyond its Glass Transition Temp. Torlon has plenty of range to handle temperatures at or above 500+F.
Torlon is manufactured in various grades, which allows its use as a primary seal at elevated temperatures and — where bearing strength is required — may be blended with Carbon or other fillers to enhance its capability to resist strain.
Best Uses for Torlon
An excellent use for a Torlon bearing would be a drier bearing in the pulp and paper industry, allowing for a very complicated shape and resist the elevated temperatures found in the application.
Torlon is used frequently as a seal ring in transmissions due to its high strength and resistance to deformation.
It’s commonly found in automotive transmissions as a replacement for metal rings, which would score mating surfaces.
It also has excellent insulating properties for use in electrical service. Torlon can also be used as a thermal insulator for high temperature applications.
Torlon has a wide variety of uses where low-deflection and broad changes in temperature are required, while maintaining strength.
Torlon also has excellent resistance to Gamma radiation.
Eclipse has been manufacturing with Torlon for 20 years with continued success in the most arduous applications requiring high strength, chemical and thermal resistance.
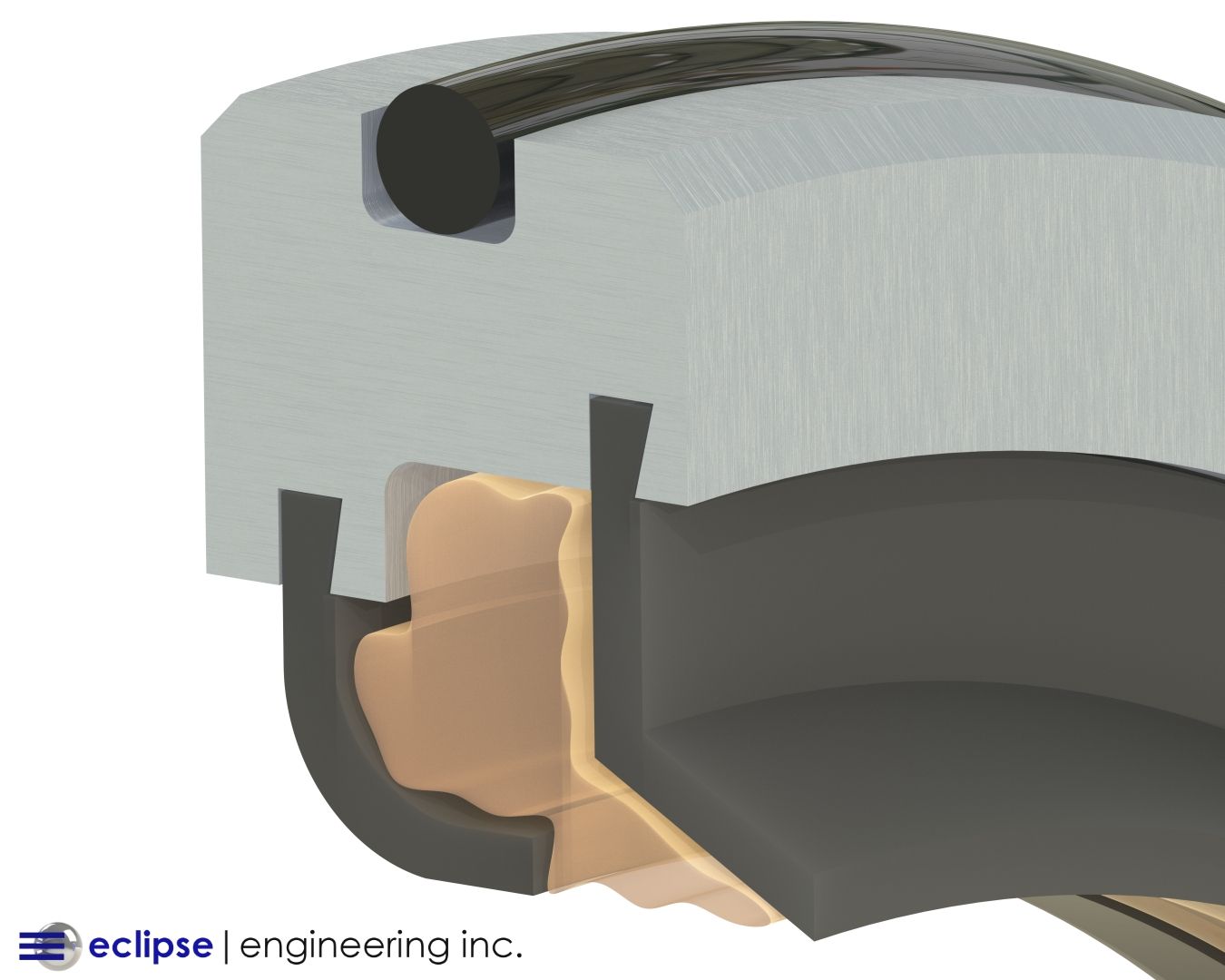