How Eclipse Seals Revolutionize the Medical Equipment Industry
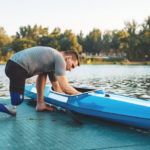
During an operation or a procedure, medical equipment must have a nearly 100% reliability rate to be considered a viable tool to work on a patient.
Seals play a very important role in many different facets of medical equipment operation.
They ensure that fluids are retained, and that contamination is kept out of operating systems. Seals also help keep electrical components dry and preforming at their peak.
There is a variety of equipment that use seals in the medical field. A few examples of this equipment includes the following:
- Disposable catheters
- Prosthetic feet for proper adjustment of foot angle
- Accumulator in prosthetic knee that provides a more natural gate
- Saline pumps to help push fluids through the body
- Respirator pumps to help force air through the lungs
- Suction pumps for pulling fluids from the body during and post-surgery
- Drills and saws for insuring retention of fluids and lubricants during an operation
- Mixer seals used to produce pharmaceuticals
Here’s an in-depth look at how seals help ensure the optimal performance of a variety of medical equipment.
Seal Components Found Within Medical Equipment
Disposable Catheters
Catheters are often used during a surgery or medical procedure to allow access into arteries or veins. Catheters serve many different internal procedures, including an atherectomy.
Sealing around the inserted instrument allows fluids to pass through the tube, or be blocked from exiting the body.
In some cases, the catheter is rotated during the procedure. This requires very low friction seals.
Some of these applications utilize small motors that require very low friction, so that the motor does not stall, and contamination is kept out of the motor.
Prosthetic Feet
In prosthetic feet, seals are used when fluids within a chamber allow a patient to adjust the angle of their gate.
This adjustment is based on the type of footwear being used. These types of seals need to be able to handle pressures that can exceed 4000 PSI.
Accumulator in Prosthetic Knees
Artificial knees can create a gate problem for the patient if the leg isn’t allowed to swing freely as the patient walks
By use of a small accumulator with oil and a gas in the device, a patient has a more natural gate as they walk.
Saline Pumps
Medical pumps commonly use seals for functions like pumping fluids into the body — including saline.
The seals must meet FDA compliance, and be capable of being sterilized or gamma irradiated without breaking down between cleaning cycles.
Respirator Pumps
Respirators are used to help a medical patient breathe when their lung action has been compromised.
These seals are typically over 5 inches in diameter, and often seal on non-metallic bores.
The seals must meet FDA compliance, and have very little drag. In the event of a power failure, friction caused by a seal will be a major power drain on the system. This friction will use up limited battery operation.
Suction Pumps
Suction pumps are found in numerous medical applications for drawing fluids from open or closed bodily cavities.
These suction pumps are used in central vacuum systems within institutions, or individual off-site pumps.
For off-site use, these pumps must be relatively quiet, and still produce enough suction to clear cavities or airways.
Seals are again a major contributor for energy use, so seal friction must be minimal to allow for optimal suction pump performance with limited battery life.
Saws and Drills
Saws and drills are commonly used in the operating room to aid the surgeon in a procedure.
Drills commonly have electric motors that are continuously being exposed to fluids.
Drills and saws must be able to seal out liquids, and endure a thorough cleaned via steam or irradiation.
Seals are necessary to keep electrical components dry and preforming at their peak.
Saws are also electrically driven. These components also require seals that will keep fluids from entering the electrical components — both during the procedure and when the tool is being cleaned and sterilized.
Eclipse’s Experience in Medical Equipment Seals
When a patient loses a limb, they often turn to a prosthetic limb that includes a device that would mimic a foot.
Every patient typically has a variety of different shoes. Because shoes are cut differently, the artificial foot needs to be able to rotate in a way that allows for proper orientation of the foot to the ground.
With a properly-designed valve mechanism within the prosthetic foot, the angle of the foot within the shoe may be modified to give correct orientation of the foot to the ground.
This valving may allow for absorption of shock for the user.
Through a series of valving, Eclipse has designed a series of spring energized seals that allow medical patients to unlock the valve within their prosthetic foot.
This system works by depressing a cylinder on the valve block and repositioning the angle. The valve is then relocked by depressing another button on the valve block.
Other devices may contain a small amount of gas as a shock absorber to allow a more natural gate. In this instance, a spring energized seal can be used to retain fluid and keep the gases locked in the valve body.
The design staff at Eclipse Engineering is ready to assist in your design of medical equipment and devices for use in medical care. Call us today to learn more about Eclipse Seal’s medical equipment capabilities >
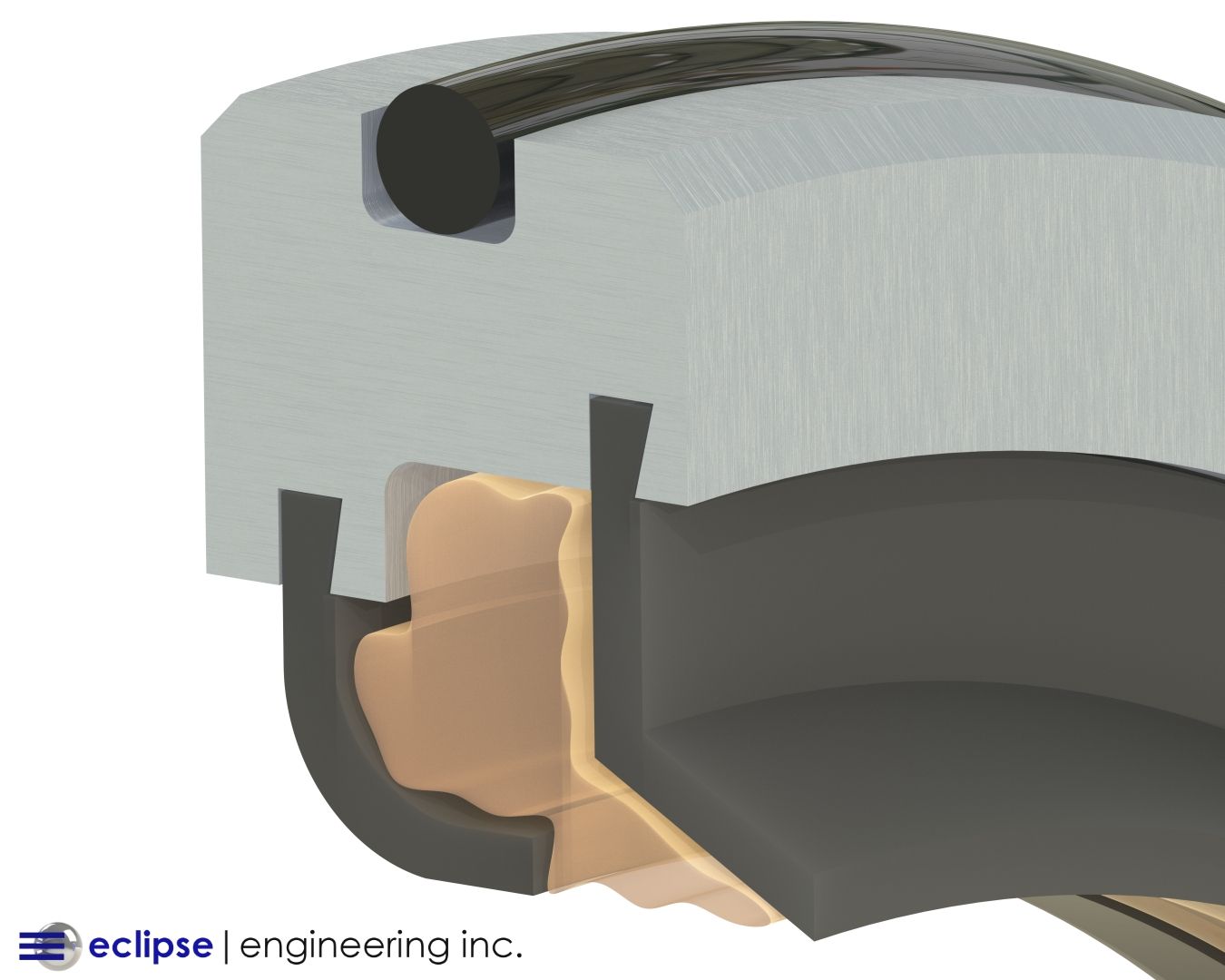