Eclipse Engineering is Back on Mars with NASA MOXIE Project
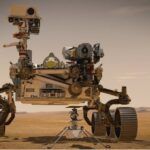
In 2004, NASA sent the rovers Spirit and Opportunity to our neighboring planet Mars. It was an exciting day for the world, and also for us at Eclipse Engineering.
We were honored to supply the seals that kept the Martian soil from damaging bearings on the overhead trunnion camera mounts. This was pivotal for keeping the machinery running smoothly.
Our latest venture 17 years later is even more cash today exciting. When Perseverance went to Mars, our seals were installed in a scroll compressor, an efficient rotary oil-less pump.
This scroll compressor is part of the Mars Oxygen ISRU Experiment (MOXIE).
The Mars MOXIE project is now laying the groundwork for man to set foot on the Red Planet.
What is the MOXIE Experiment?
The atmosphere on Mars is 95% Carbon Dioxide (CO2). The MOXIE project is intended to take that Martian atmosphere, pump it through a ceramic treated membrane and produce Oxygen. This process is called Solid Oxide Electrolysis.
The Martian atmosphere is at very low pressure. Because of this, MOXIE uses a scroll compressor which utilizes Eclipse Engineering’s products as the main compressor seal. This takes the Martian “air” and very efficiently raises the pressure. It’s then forced through specially coated ceramic plates heated to 800° degrees Centigrade.
Once that process is done, the output is Oxygen and some Carbon Monoxide and CO2 byproduct.
Why is This Process Important?
It is impossible to carry enough Oxygen onboard a spacecraft to support or survive a manned mission to Mars.
If MOXIE is successful, a future mission — prior to maned travel — would require a small factory to be created on the surface of Mars to produce a supply of oxygen.
This manufactured Oxygen would provide the oxidizer for manned missions to refuel and propel a manned mission back to Earth.
These early steps of the MOXIE project are the groundwork for creating a survivable mission to Mars and the potential to further our exploration of space.
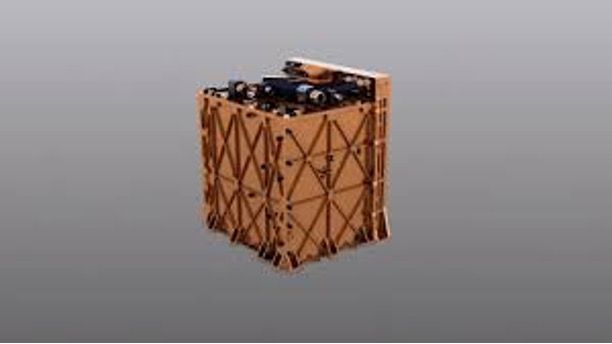
Which Device is Used on the MOXIE Project?
Many mechanical applications require extremely low friction and must work in very caustic chemicals that typically erode most standard seals. Here on Earth, our seals can be found in a variety of applications from controlling aircrafts to sealing chemical pumps.
For this project, a Scroll compressor is used to improve efficiency without the use of oil. Without oil, the compressor is capable of performing over a wide temperature range while maintaining high efficiency.
This is made possible by its design and the use of seals made from a filled PTFE compound (Polytetrafluoroethylene). PTFE or Teflon® has an extremely wide temperature range while maintaining a coefficient of friction around .08.
This low friction allows the pump to operate without lubrication. This becomes especially important in harsh and unpredictable environments.
We are proud to have supplied seals from a variety of polymer materials for over 20 years in many professional industries. Today, we are thrilled to provide devices that can be exposed to extreme conditions such as those found in space, or in other words, a typical day on Mars.
Our devices can be found in practically every industry — under, on, and off this planet — be it undersea propulsion systems, seals for electric motors propelling our newest automobiles, aircraft of all types, and of course, roving around the planet Mars.
How Can Our Seals Help Your Next Project?
You don’t need to be launching into space to get a great device.
Our custom seal and bearing solutions are designed for the perfect fit, no matter the job at hand.
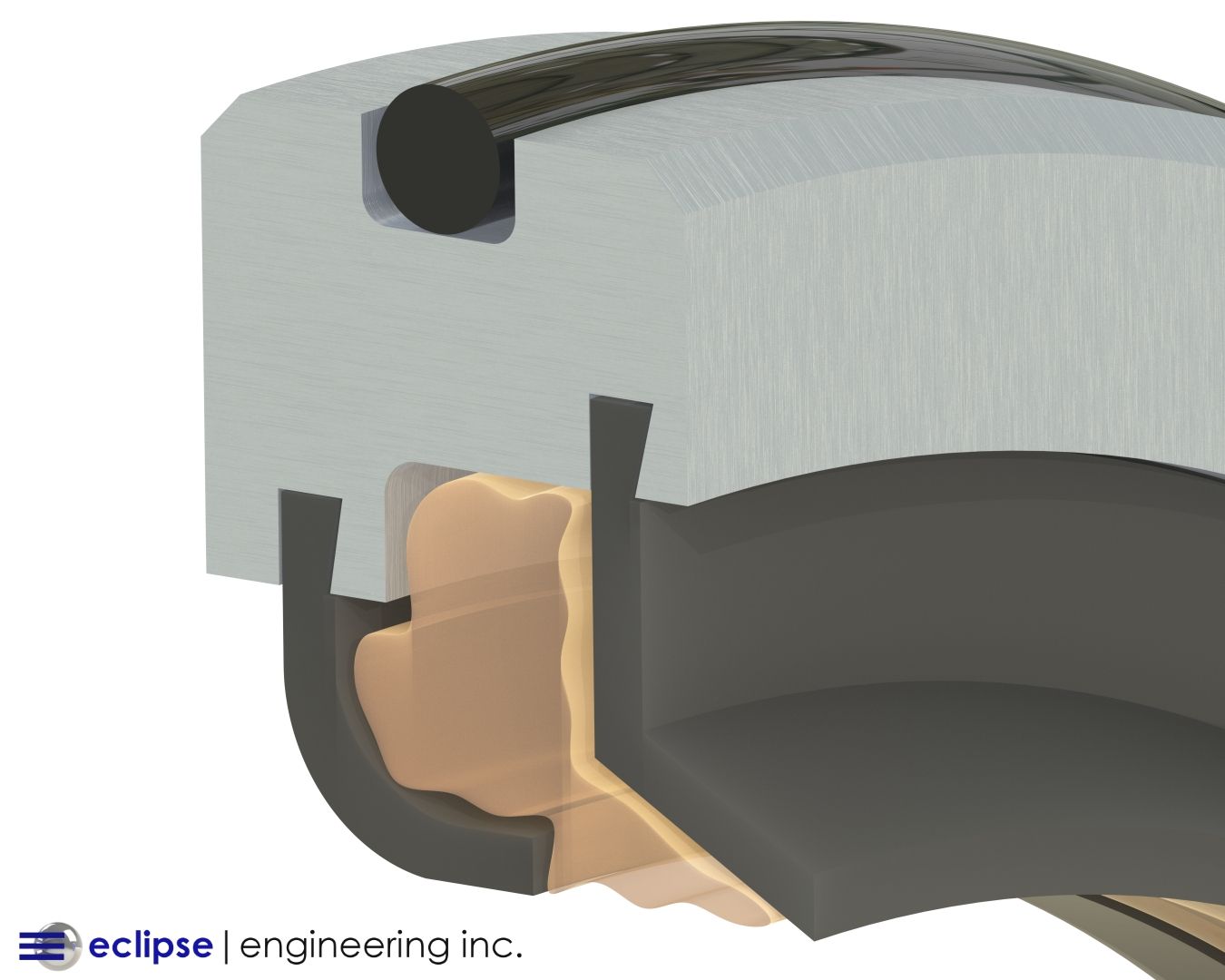