How Spring Energized Seals Are Made (And Why You Need One)
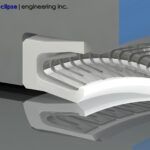
Eclipse Engineering designs and builds many types of seals for all kinds of applications. Whether it be a simple O-Ring energized seal ring or multi-lip cased rotary seal, Eclipse covers the spectrum in polymer-based seals for all projects.
With all the seal varieties available in the market today, spring energized seals represent a significant portion of Eclipse’s sales. With our ability to both design and manufacture spring seals in-house, including the cutting and welding of the springs themselves, we can genuinely say spring energized seals are one of our specialties and core products.
Here we’ll discuss the basic functionality and design principles of spring energized seals and discover why one might be the perfect sealing solution in your application.
How Does A Spring Energized Seal Work?
A basic spring energized seal consists of two components, a polymer-based seal jacket and, of course, the spring. Jackets are typically made from one of Eclipse’s many PTFE material blends, which have plenty of desirable properties in a sealing application. Namely, it’s low friction, high and low-temperature range, and broad chemical and media compatibility.
The seal jacket is typically machined in the shape of a “U” following the same design principle of many standard urethane and elastomeric U-Cup seals. Except in some special cases, the seal is usually installed with the open side of the “U” facing the system pressure.
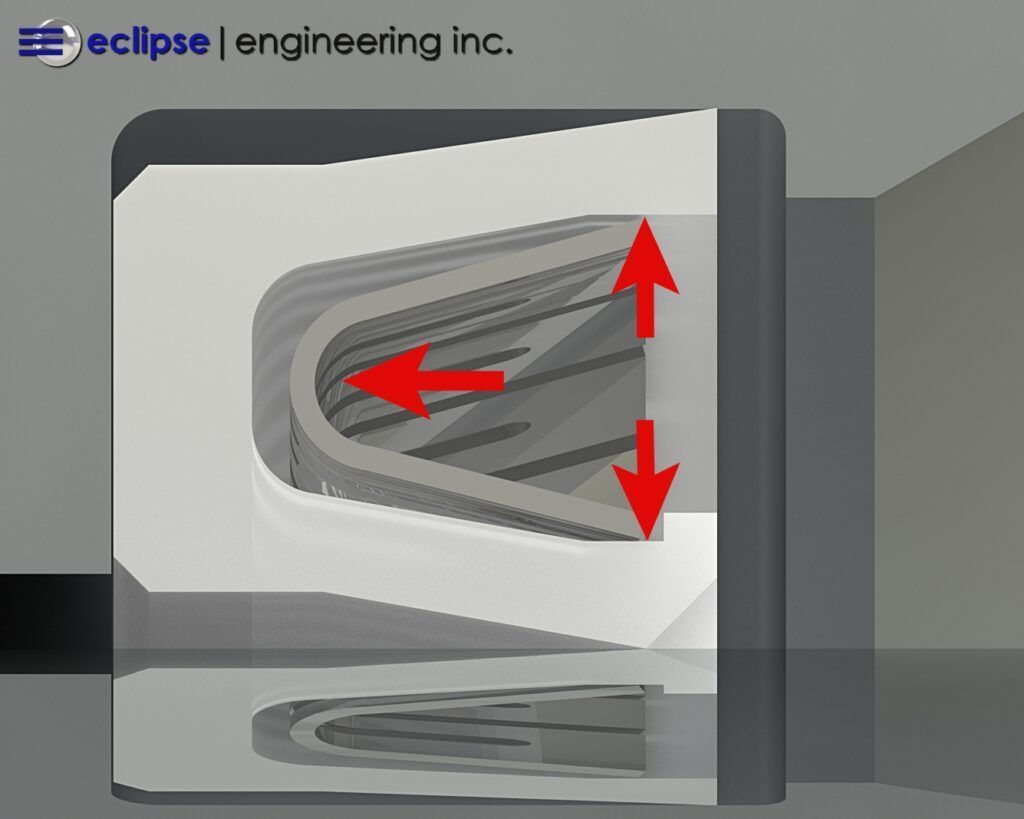
This is done so that the pressure actually energizes the seal to improve sealability. The force from the pressure will expand the seal lips driving them into the hardware sealing surfaces. The higher the pressure is, the more force is applied and therefore the greater the sealing potential.
So why is a spring needed if the geometry of the seal jacket is pressure energized? This is because the spring will be responsible for providing the primary sealing energy at low pressures and start-up conditions. Generally speaking, most spring energized seals are don’t begin to see the benefits from the pressure energy until at least 100 psi.
The necessity of a spring inside the seal jacket is also in large part due to the material nature of PTFE. Unlike elastomeric materials, PTFE possesses very little memory or ability to rebound once deflected. Much like a lump of clay will stay in the position it’s pushed into, PTFE will not bounce back when a force is applied.
So, while a Urethane or FKM U-Cup will function fine without a spring, a PTFE jacket will require a spring energizer to ensure the lips are firmly contacting the hardware in all pressure scenarios.
Different Springs for Different Applications
Eclipse offers three different types of springs that can be used in seals. All have the same functional intent—to energize the seal lips—but one variety might be better suited for an application than another.
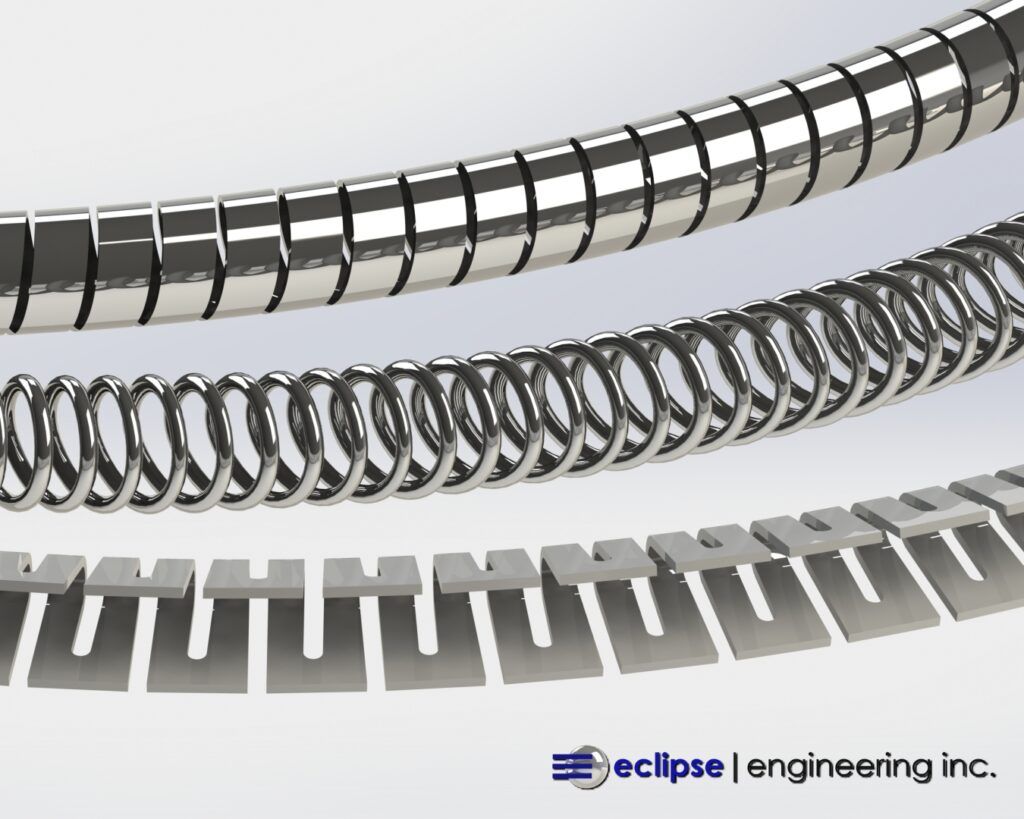
Cantilever V-Spring
V-Spring is made by forming and stamping thin strips of metal sheets through progressive dies. V-Spring offers a very linear load curve, meaning that the more it’s deflected, the more force it applies.
It provides more of a point load in the jacket, focusing energy at the leading edge of the seal lips. This makes it desirable in reciprocating applications requiring the scraping of media. Multiple springs can also be stacked together for even greater loading.
Canted Coil Spring
Canted Coil is one of Eclipse’s specialties and we manufacture our own spring in-house. Canted Coil is typically used in applications where low friction and consistent loading are needed.
It possesses a very unique load curve where spring force changes very little despite varying deflection. This uniform and predictable loading makes it the spring of choice for most rotary applications.
Helical Ribbon Spring
A helical spring is made by winding a thin, flat strip of metal into a helix, creating a round tube. Helical has a very steep load curve and offers the highest force per linear inch.
It’s most often used in static face seal applications and in cryogenics where high loading is needed. It can be yielded after being compressed so it’s usually not recommended for dynamic applications.
Why Use a Spring Energized Seal?
With many options available for Elastomeric U-Cups and O-Ring Energized Seals available on the market, why would you need a Spring Energized Seal?
A PTFE spring energized seal offers the greatest temperature range possible for a seal. They can be used in cryogenic applications approaching absolute zero all the way to combustion processes at 550°F. No elastomer will function at these temperature extremes.
With a PTFE and stainless-steel spring, chemical compatibility is also maximized. Applications with caustic or aggressive media may not be able to use any type of elastomer.
The shelf-life of a PTFE spring seal is also indefinite. Eclipse has employed spring energized seals in Dam Spillway gates that require 50+ years of service life.
Even in applications with benign media and temperatures, spring seals can still offer an advantage. Yes, you can energize a PTFE jacket with an O-Ring. But the load curve of an O-Ring is very undesirable, especially in rotary applications. A rotary seal using a canted coil will outperform an O-Ring in terms of friction, consistency, and wear-life.
Scraping viscous media such as epoxy resins? Multiple V-Springs inside a filled UHMW-PE jacket can provide optimum sealing and wear-life performance. With redundant sealing points and highly focused load, spring energized seal can do the job no other seal can.
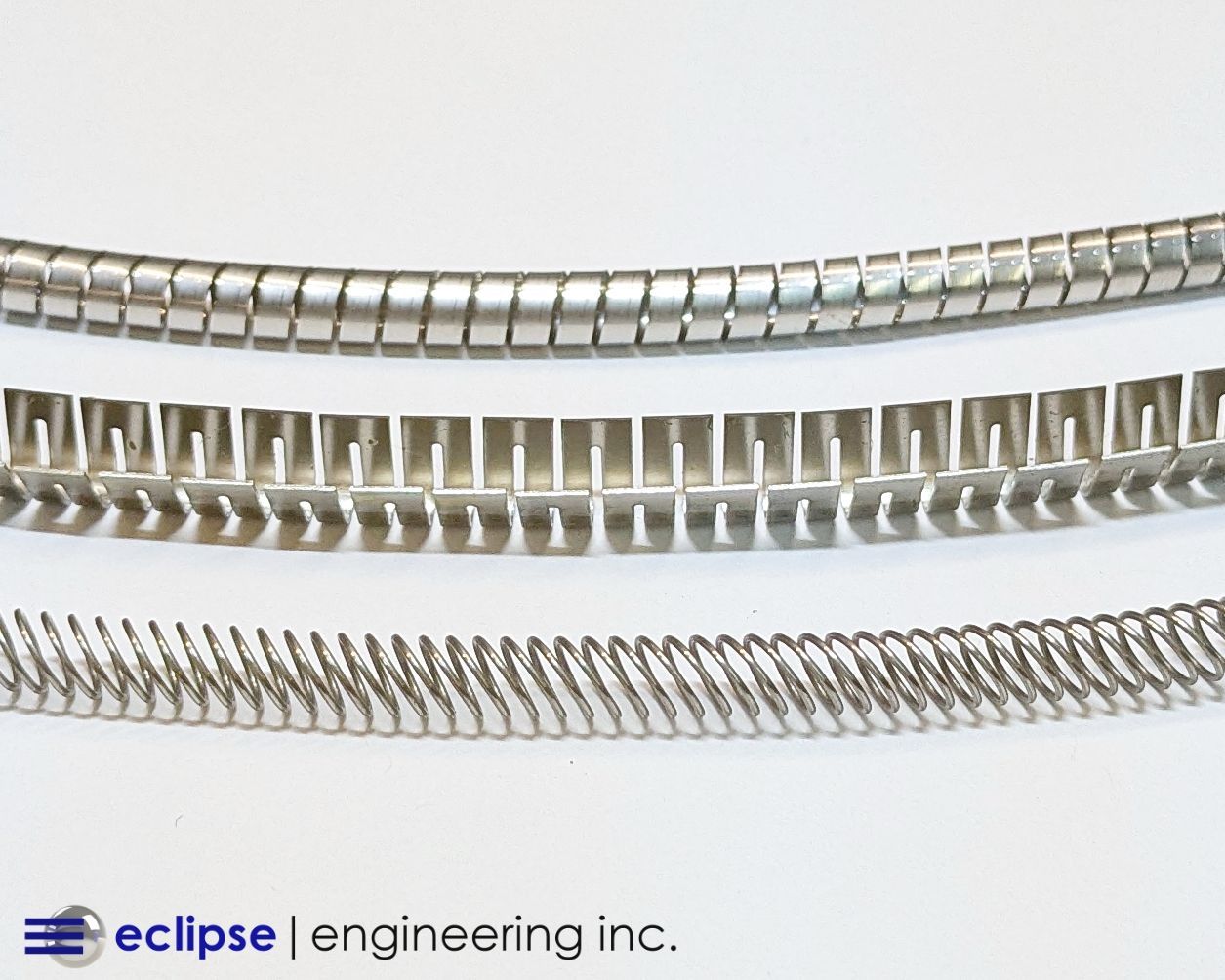