Celebrating 25 Years of Innovation & Growth: The Eclipse Engineering Journey
Humble Beginnings
In 1999, Eclipse Engineering’s founder, Cliff Goldstein, recognized an industry need for engineering support in the manufacturing and prototyping services sector. Eclipse was born with the goal of offering unparalleled service and custom engineered solutions for demanding applications.
Looking back 25 years, Eclipse Engineering started as a one-room schoolhouse. Cliff would spend mornings prospecting for business, afternoons working on CAD designs, and evenings machining parts. It was a family-run startup, with his wife Bobbi handling invoicing and bill payments, and even his mother labeling parts when she was around.
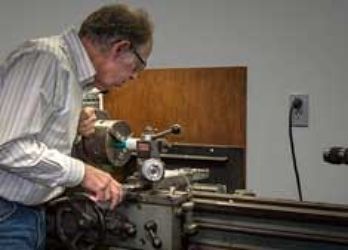
Growth and Expansion
After about six months, the business had grown enough to hire additional help. This was when the business really took off. Support from major national seal distributors played an instrumental role in getting the business off the ground. Thanks to local customers from Jemco Seal, Eclipse was on the move.
Initially, the goal was to run a basic plastics machine shop, with no intention of entering the seal market. However, inquiries started pouring in for seal manufacturing due to Eclipse’s engineering support, plastics machining expertise, and quick turnaround on parts. After about two years, Eclipse acquired all the seal business from Jemco Seal, along with their inventory, effectively establishing Eclipse as a seal distributor. This move complemented the fledgling distribution business that Eclipse had started independently.
A Major Milestone
Eclipse secured a major contract with Sundyne Pumps in Colorado, which launched the company into high gear. Over the years, Eclipse evolved to produce standard product offerings for a wide range of industries including Hydraulics, Pneumatics, Energy Production, Aerospace, Pharmacopeia, and Food Handling. The institution of the ISO9001/AS9100 quality system in 2015 allowed Eclipse to become a top-tier supplier.
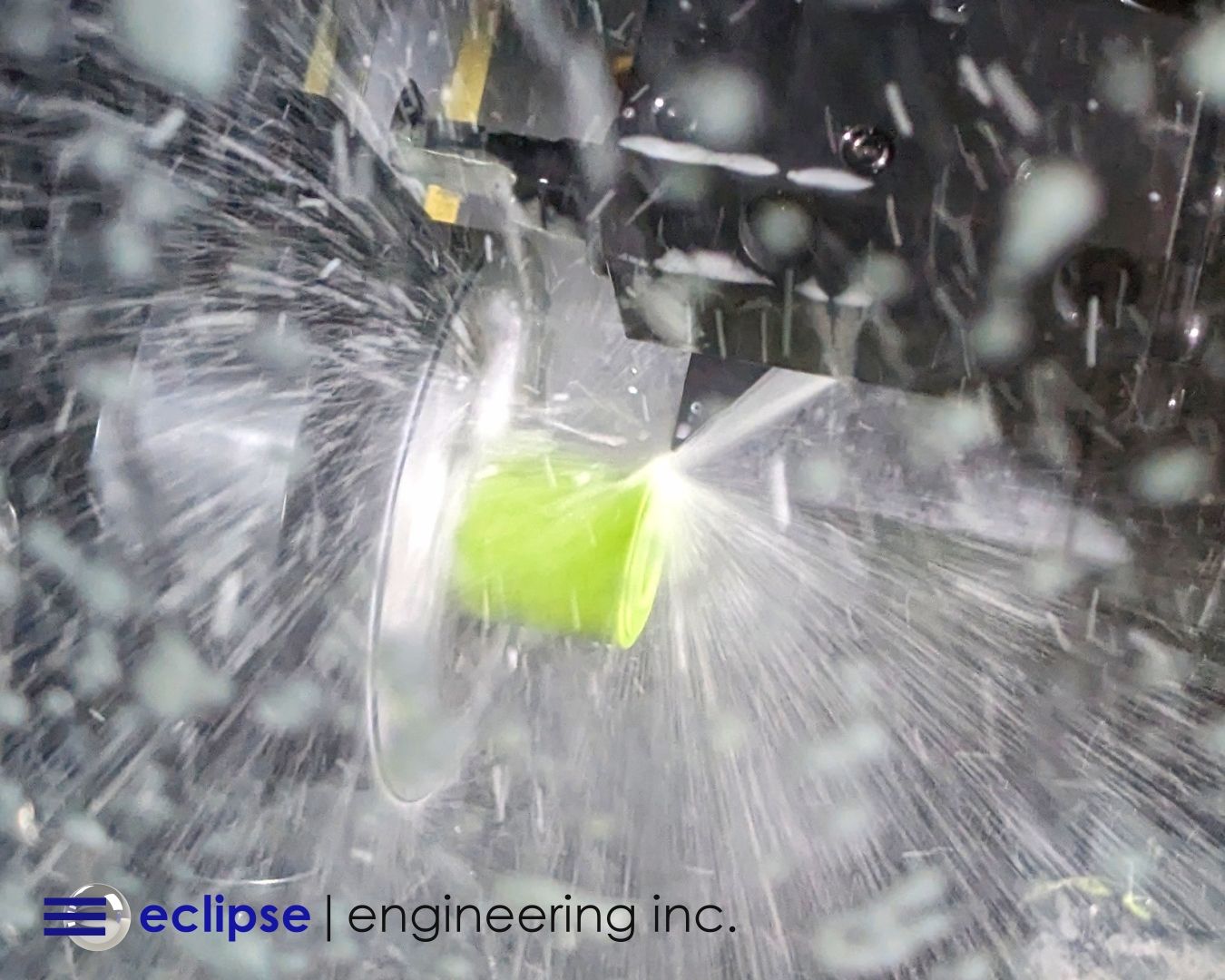
Empowering Employees
Fast-forward 25 years, and Eclipse has expanded from a few pieces of equipment to seven CNC turning centers, a CNC mill, two laser welders, visual measurement machines and all the support equipment for a modern design and machining center. Our expert sales and engineering teams help design and produce sealing solutions for customers down the street to across the globe.
With 25 employees, five years ago, an ESOP (Employee Stock Ownership Plan) was created. This plan empowered the employees who had been with Eclipse since the beginning—they now own a stake in Eclipse and can shape their own destiny. For our customers, this business continuity means our culture of quick responsiveness to their needs remains unchanged.
Customer-Centric Approach
Eclipse Engineering was founded on the concept that if the company placed its customers’ needs above its own, it would always profitably grow. This customer-centric approach has remained steadfast, even in the face of Covid and the challenges of a global economy. Eclipse has continually adapted to evolving customer requirements including the increasing need for quality certifications and regulatory compliance.
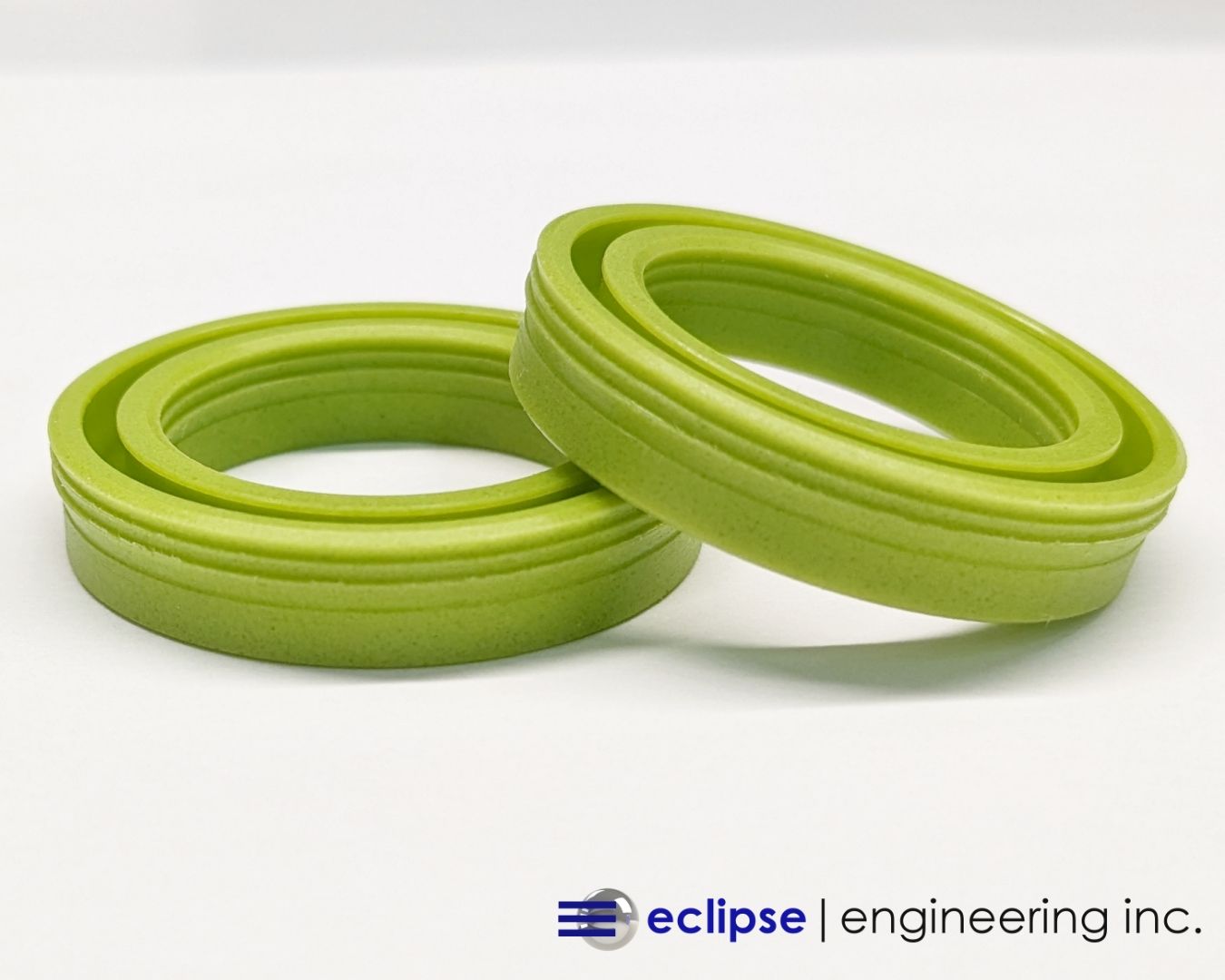
Looking Ahead
Today, Eclipse is a reliable supplier of polymer-style seals and bearings in the global marketplace. It’s the synergy between the employees and customers that has propelled Eclipse into the company it is today. As Eclipse celebrates its 25th anniversary, it looks forward to continuing its legacy of innovation, growth, and exceptional customer service.
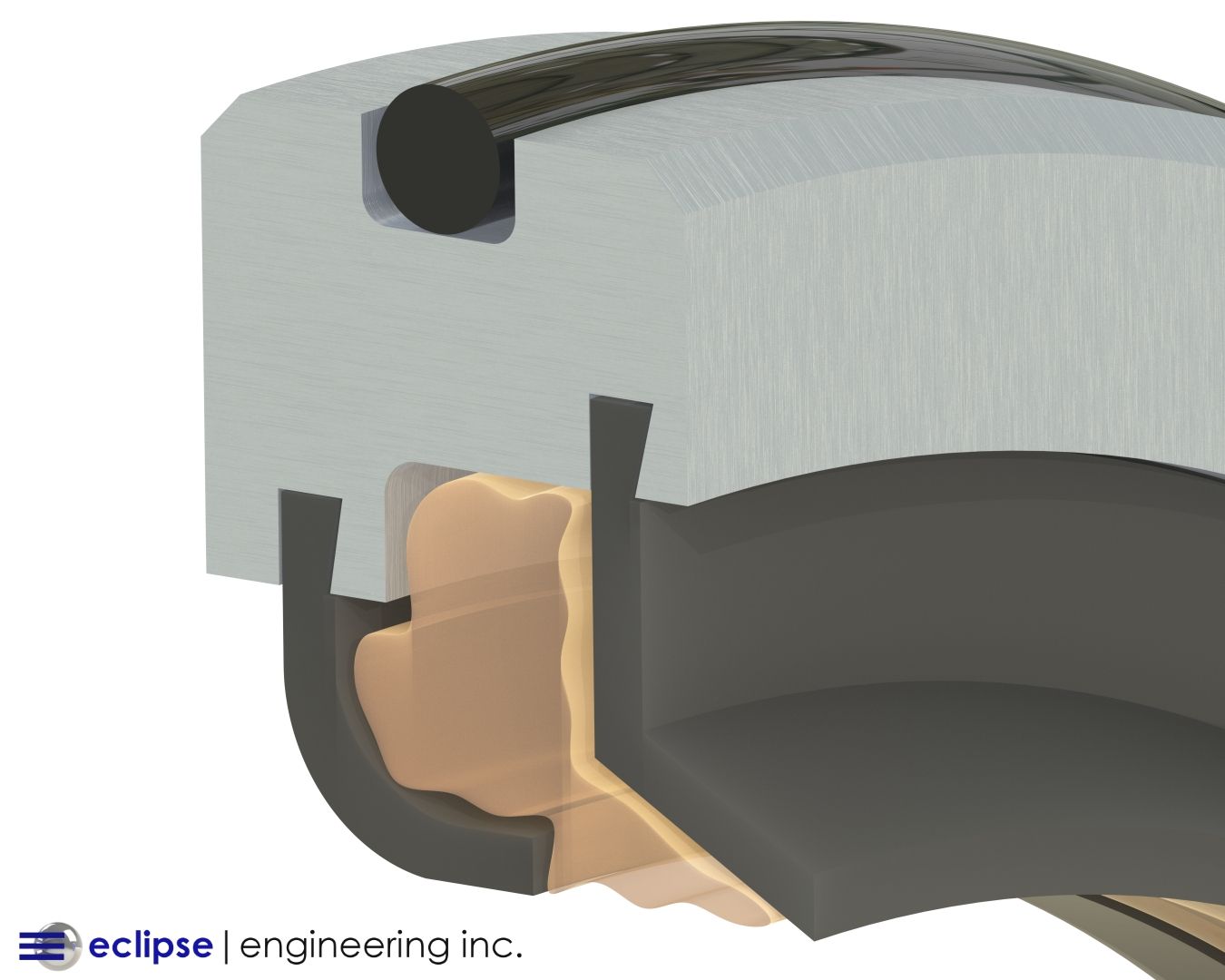