Case Study: Replacing U-Cups with PTFE Spring Energized Seals in High-Temperature Applications
The use of elastomeric U-Cups in reciprocating sealing applications is widespread throughout the industry. As commodity items, U-Cups are readily available in a number of materials and can be found on-the-shelf from multiple distributors and manufacturers in many standard sizes.
Named for the shape of their cross-section, a U-Cup’s design is pressure energized, increasing sealing effectiveness when compared to a standard O-Ring. This means as pressure increases, the sealing lips are continually forced into the mating hardware surface ensuring good contact at all times. The simple and easily moldable design is an effective sealing solution to many systems in both hydraulic and pneumatic applications. Modifications in lip thickness and inclusion of an O-Ring Energizer can tailor sealing loads and wear life to specific situations.
A key advantage to an elastomeric U-Cup is the relatively small and simple hardware space needed. Because of their flexible compounds, most U-Cups can be installed in a solid gland configuration. Therefore, a basic ID or OD groove is all that is needed for proper seal retention and no special tools or considerations need to be taken for correct installation.
U-Cups are available in many of the same compounds as standard O-Rings such as Nitrile, Fluorocarbon, and EPDM, but polyurethanes might be the most common material. Urethane provides a good combination of elasticity/pliability and toughness. Therefore, it exhibits good sealing characteristics as well as durability and wear resistance.
These desirable qualities make U-Cups an optimal solution for many sealing systems across multiple industries and can be found in countless standard products. But Eclipse is approached many times a year with customers pushing the limits of standard U-Cups and in need of better solutions.
The Client’s Issue
Eclipse was approached by a leading pneumatic cylinder manufacturing seeking a sealing solution for a unique application. While U-Cups typically provide optimal sealing performance in pneumatic cylinders, this application presented a difficult challenge. The air cylinder was to be used as an actuator for a latch on a large industrial oven. While pressures, speeds, and cycle times were nothing out of the ordinary, the temperature at which it had to operate at was – a continuous 500°F.
Operating Conditions:
- Pressure: 90 PSI
- Media: Air
- Stroke: 3”
- Cycle Frequency: 2-4 cycles/day
- Cylinder Rod Ø: 0.500”
- Operating Temperature: 500°F
The most common Urethane U-Cup seals have a maximum temperature rating of only 220°F, so they knew these wasn’t a viable choice. Their best option was a Fluorocarbon U-Cup, which are typically rated up to 400°F. Fluorocarbon can withstand temperatures up to 440°F but only for short periods of time. Despite not meeting the temperature requirements of 500°F, the customer gave these a try. Not surprisingly, though, the seals failed quickly.
The real challenge was the fact the oven operated at a continuous 500°F for long periods of time. Even if the properties of the Fluorocarbon could remain intact enough to provide an acceptable level of sealing, the longevity of the seal would be severely compromised. Like most rubber compounds, Fluorocarbon is subject to “heat aging” where high temperatures accelerate the degradation process that normally occurs over years of service. At this extreme temperature, the effect would be prompt. The customer quickly concluded a standard sealing solution wasn’t going to work and turned to Eclipse.
The Eclipse Solution
Eclipse knew that 500°F called for a PTFE based seal material. Depending on fillers, PTFE can successfully operate at temperatures as high as 575°F. The long-term exposure to high heat would also not be a problem for PTFE. Unlike rubber or elastomeric compounds, PTFE will not degrade over time and can be considered to have indefinite shelf-life.
With the temperature ruling out the use of O-Ring energizers, Eclipse’s Spring Energized seals would be needed. For optimal point loading in a reciprocating application, Eclipse chose a stainless steel Cantilever V-Spring for the energizer and ET006: Carbon filled PTFE as the seal jacket material. The carbon filler provides excellent heat and wear resistance while remaining commonly available.
Eclipse designs and manufactures thousands of spring energized seals every year, many of them successfully operating in conditions far more difficult than the parameters presented here. The challenge for this application was the packaging and installation requirements mandated by the customer. The simple solid groove housing, in which a standard U-Cup installs without trouble, would not work for a PTFE spring energized seal.
For rod configurations, installation into a solid gland requires the seal to be “kidney beaned” or folded in on itself to be put into the groove. For an elastomeric U-Cup, this is no problem as it can be bent and distorted and still spring back into its original shape once in the groove. For piston configurations, the seal needs to be significantly stretched for installation into the groove. Again, this is not a problem for rubber or urethane compounds.
But the combination of PTFE’s inelastic nature and the fact that a cantilever spring cannot be severely distorted without damage or yielding, means installation of PTFE spring energized seals into solid glands is normally not an option. At very large diameters, with comparable small seal cross-sections, installation might be achievable. But at diameters less than an inch, such as in this case, installation would be nothing short of impossible without seal damage.
The customer’s ideal solution would have retrofitted into the current U-Cup grooves, but with this not being feasible, Eclipse needed to propose an acceptable alternative. Most spring energized seals at smaller diameters are installed in split or two-piece grooves. This configuration is an open groove with a secondary retention piece. For example, the seal can be contained by a separate bolted on cover-plate or threaded packing nut.
The two-piece design facilitates easy installation and replacement for spring energized seals, but the customer did not want to significantly change the current hardware design for the cylinder. Adding a cover plate to the assembly would be out of the question. Eclipse had to work within the current hardware envelop of a standard air cylinder and present a design that allowed for easy installation of the spring energized seal without adding any components.
Eclipse knew this was the perfect application to use a stepped gland configuration. A stepped gland is an open groove with a small barb or step at the front which retains the seal. A specific seal lip type ensures the seal gets locked into place once pushed over the step. In this case, a step of only 0.010 to 0.015” is all that is needed for seal retention. The seal needs to be only minimally compressed or stretched (depending on rod or piston configuration) for a simple “push in” installation.
Most customers are surprised such a small feature can retain the seal fully. In most cases, once installed, the seal is so well locked in place that special tools or physically damaging the seal will be required to remove it. Stepped glands are successfully employed at a variety of diameters in the most challenging reciprocating applications.
How It Performed
Eclipse’s PTFE Spring Energized Seal ensured the air cylinder performed flawlessly at the 500°F temperature. Eclipse’s ET006: Carbon filled PTFE seal jacket provides excellent wear resistance and extended seal life even in the long-term high temperature environment. The improved low friction characteristics of PTFE also added to the smooth and consistent cylinder operation unlike an elastomeric compound.
The use of a stepped gland allowed the use of the spring energized seal without significant modification to the customer’s hardware and no additional components. Eclipse successfully designed and manufactured a sealing solution that met or exceeded the customer’s requirements in every way.
Eclipse has successfully converted many U-Cup seals configurations to use PTFE Spring Energized Seals in a diverse number of industries and applications. Whether due to extreme temperature, chemical attack, severely abrasive media, or better friction control, if you have a standard U-Cup that is failing in your application — Eclipse can help.
Contact us today to see if a Spring Energized Seal is right for you >
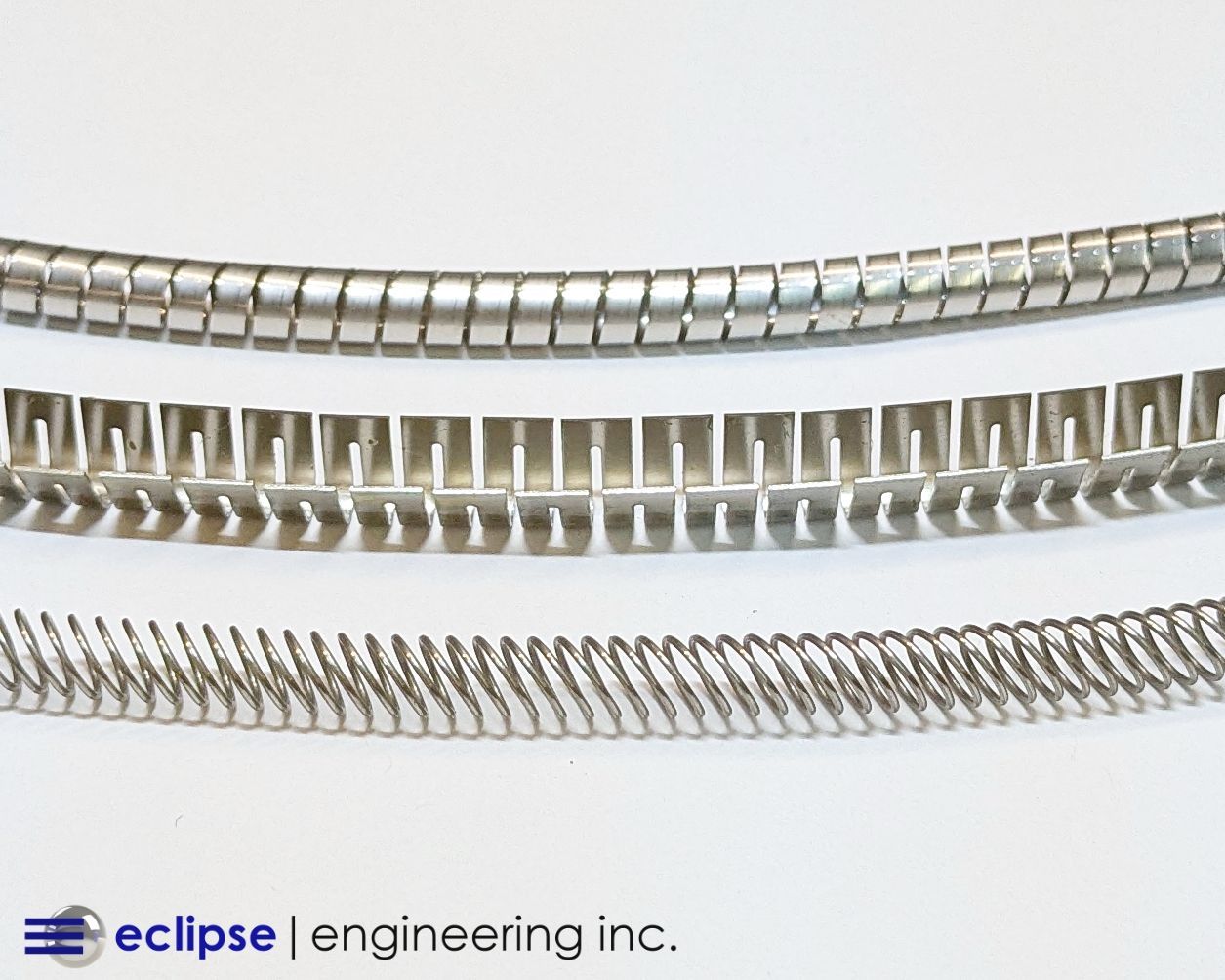