Case Study: Replacing V-Packings with Nested Spring Energized Seals
V-Packings, also called V-Stacks or chevron packings, have been around for decades and represent one of the earliest advanced sealing designs. While existing long before PTFE spring energized came into being, they are still used in a variety of industries today. Eclipse designs and manufactures its fair share of custom V-packings out of various materials every year.
V-Packings offer a simple yet effective design principle. A series of nested “Vees” are arranged in a gland where the points of the Vees serve as the sealing contact points in the hardware. They are designed in such a way that if the stack is compressed axially, the Vee behind will expand the radial cross-sectional width of the Vee in front of it. This will provide the needed energy to force the contacting sealing points into the hardware surfaces.
Compression force is usually provided by a packing nut in the hardware. The more the stack is compressed, the tighter the sealing potential. This offers big advantage over other simple seal designs such as rope packings because the seal can be energized in focused locations. If leakage is occurring, tightening the packing nut if often all that’s needed.
V-Packings are often used in heavy industrial applications where a robust and substantial seal is needed. The numbers of Vees in the stack represent the number of effective sealing points. Eclipse has designed manufactured packings with up to ten Vees, but the only real limit is axial gland space in the system. In these heavy industrial applications, the ability to affect sealing performance by turning a wrench is well utilized where system maintenance is regularly performed and monitored.
While V-packings can work well in the right application, there are drawbacks to the design. A spring energized seal offers numerous advantages over V-packings and in many cases can outperform them in all major sealing aspects.
The Client’s Issue
Eclipse was approached by a customer looking for improved efficiency and longer seal wear life in their Natural Gas compressor. The compressor piston rod seal was currently using a Virgin PTFE V-Packing, and while it was working sufficiently, the customer was looking for improved compressor performance. All system aspects were under review for enhancement, including the seals.
Operating Conditions:
- Reciprocating Rod Seal
- Compressor Type: Single Acting, Crosshead Piston
- 1.125” Rod Diameter
- Stroke Length: 4”
- Piston Speed: 850 FPM
- Media: Natural Gas
- Operating Pressure: 5,000 PSI
The Eclipse Solution
Eclipse knew that replacing the current V-Packing with a spring energized seal could potentially provide the customer with all the improvements they were looking for. While V-Packings certainly serve their purpose, they have a few limitations and drawbacks a spring energized seal does not.
The only energy applied in a V-Packing is from the initial compression in the hardware. In the case of PTFE, where it’s material properties essentially provide zero internal energy or elasticity, the initial compression energy will eventually diminish as the material relaxes and becomes worn.
Thus, a V-Packing will need maintenance over its lifespan. If leakage starts occurring, tightening the packing nut, or compression device will be necessary. But this also leads to a major disadvantage of a V-Packing with the imprecise way of loading the seal. A stack needlessly compressed too tight will experience accelerated wear and introduce excessive friction on the shaft.
A spring energized seal solves this problem. Its internal springs are a known and calculated value, providing the optimum sealing load at all times. This loading can be tailored to the application whether heavy scraping is needed or extreme low friction.
Unlike a V-Packing, the spring will properly load the seal over its entire wear life. Therefore, essentially maintenance free operation is possible along with much more consistent loading and friction. The seal is no longer dependent on an operator to adjust as needed.
Many customers like the fact that a V-Packing has multiple sealing points for redundancy. In a retro-fit situation, as in this case, the customer wanted to retain this aspect of the seal. Eclipse replicated this feature by using nested cantilever V-Springs within the seal jacket. The external seal lips were machined with point contact locations the correspond to each spring. Thus, multiple energized contact points were maintained.
Whereas a V-Packing uses separate rings to achieve these redundant sealing points, the spring energized seal accomplishes this in a single, self-contained seal. It is no longer necessary to assemble the separate rings during installation, reducing part count and eliminating the potential for assembly error.
Eclipse chose its ET014: Polyamide filled PTFE for the seal jacket material. While Eclipse can custom machine a V-Stack set out of any of its filled PTFE options, most V-Stacks are usually just Virgin PTFE by default. This leaves a huge potential for wear life improvement by switching to a filled PTFE material. Eclipse used ET014 because the customers shaft hardness was below what was recommended for aggressive fillers. ET014 would provide a significant improvement in wear life while not damaging or deteriorating the hardware.
How It Performed
Eclipse’s spring energized seal met all the customer’s objectives in improving the efficiency and maintenance intervals of their compressor. The spring energized seal provided lower and much more consistent friction therefore improving the overall running efficiency of the whole mechanical compressing system.
The seal also no longer requires regular attending to perform optimally. This combined with the longer wearing ET014 seal material extended rebuild intervals greatly, thus saving the customer both time and money. The reduced part count and ease of seal installation were an added bonus to the project.
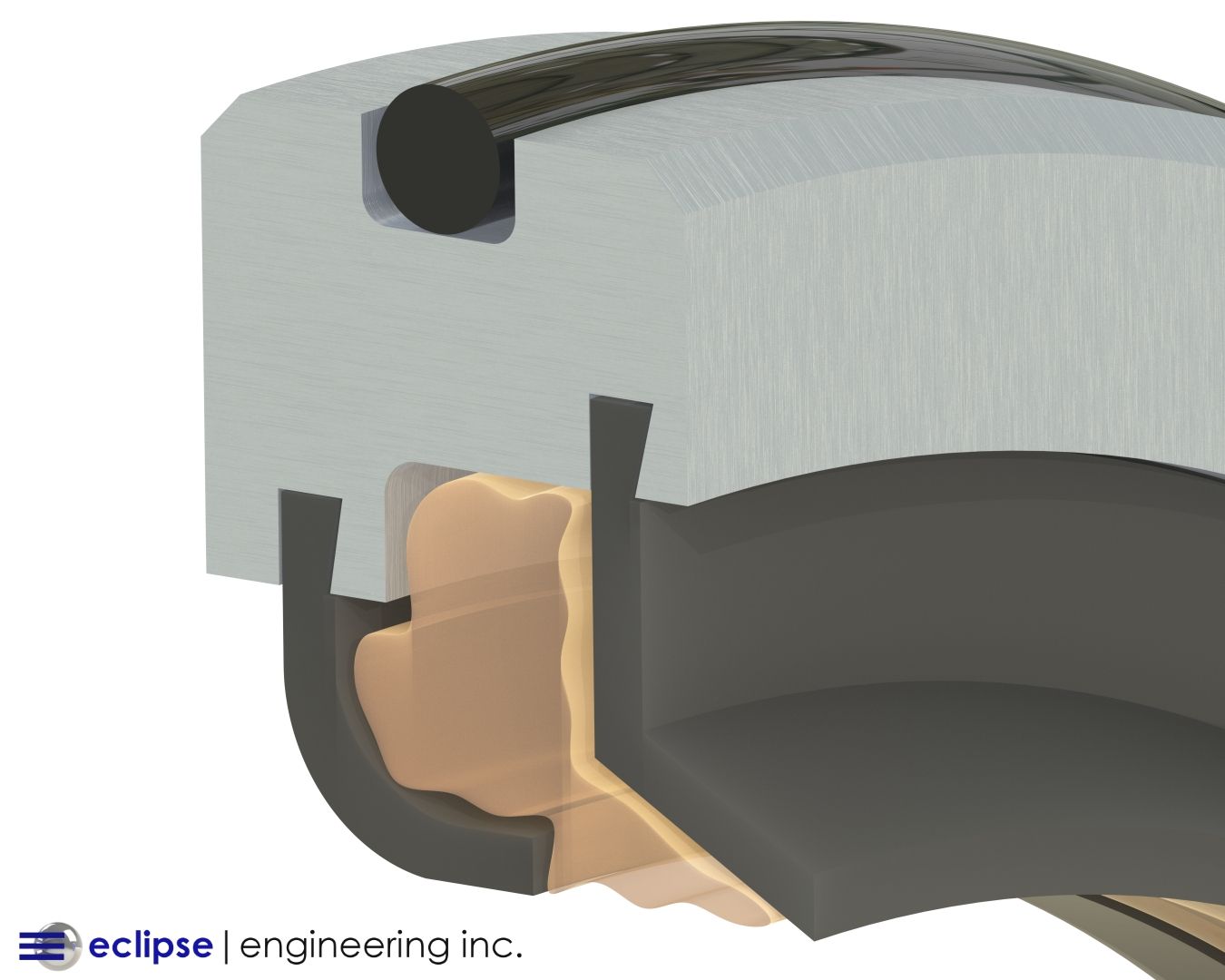