Case Study: Customized Cryogenic Face Seals for Liquid Oxygen Rocket Turbopumps
The space race is on! While headlines about returning to the Moon or manned missions to Mars garner most of the attention, commercial space launch platforms and services have become increasingly utilized and prevalent.
With demand for services provided by low orbit satellites ever expanding, there is no shortage of new launch vehicle requests. The communications, navigation, and weather services most people have become accustom to are all made possible by the thousands of satellites orbiting the Earth each and every minute.
While safety and reliability will remain the top priority of every launch, the success of a launch system has ultimately changed to be decided by one important merit – cost. In fact, the cost per kilogram of payload is often the prevailing factor in determining the commercial viability of a system.
New competition from privateer launch companies in the US, as well as state run programs from foreign countries around the world, have reset the economics of putting an object in orbit. While technological advancement has never ceased, the main focus has shifted to developments in reducing cost.
Whether it be innovations in performance or production/operating economy, components in the complex launch systems need to adapt to the new challenges. Its obvious seals play an important role in the success of a rocket launch and engineers are increasingly asking more of the sealing systems.
The Client’s Issue
Eclipse was approached by a designer and manufacturer of turbopumps used in rocket engines. A turbopump is used to supply high pressure fuel and oxidizer into the combustion chamber of a rocket.
The separate components of the turbopump need to be sealed at their mating points in a static face seal configuration. Seals are needed on both the fuel and oxidizer sides of the pump.
But the oxidizer, in this case Liquid Oxygen (LOX), presents the much greater sealing challenge due to the cryogenic operating temperatures.
Operating Conditions:
- Internal Face Seal
- Static
- Gland Outer Diameter: Ø6.250
- Media: LOX
- Pressure: 2,000 PSI
- Temperature: -335°F to +70°F
When sealing gases at cryogenic temperatures the surface finish of the hardware becomes critically important for leakage control. The low temperatures of cryogenics effectively harden any seal material reducing its ability to conform to hardware surface imperfections and machining grooves. In most cases, a surface finish of 6µin Ra or better would be recommended.
Finishes in this range would be considered “mirror-like” and almost certainly require secondary grinding, lapping, and honing to be achieved. Within a seal groove that must be milled, these operations can be difficult and time consuming to perform, therefore add significant cost.
Being a complicated and precision component, the turbopump can represent a substantial portion of the entire launch vehicle’s cost. Any efforts to reduce expenses in this area would have a meaningful impact on the program’s budget. By forgoing any secondary polishing process in the seal grooves, manufacturing time of the turbopump components could be lessened by a considerable amount and subsequent savings could be realized.
The best achievable surface finish without any secondary processing or operations would be somewhere around a 16µin Ra. While this is great in terms of potential cost savings, designing a successful seal under these conditions becomes challenging. On top of this, the seal itself would be under scrutiny to be as cost-effective as possible.
Eclipse was nevertheless, up for the task.
The Eclipse Solution
When dealing with cryogenic temperatures a spring energized seal is almost automatically chosen. The type of spring used can be decided based on the application though. Eclipse offers three types of springs that can be used to energize seals: Cantilever V-Spring, Canted Coil, and Helical. Each spring has its own advantages and drawbacks.
Helical spring is often used in cryogenic applications. It offers some of the highest unit loading of all the spring types. This is very desirable at cryogenic temperatures to ensure the seal remains energized keeping the sealing lips properly engaged and loaded in the hardware.
Eclipse knew that, as part of the cost savings efforts of the launch program, the seals would need to withstand multiple assemblies and uses. Helical spring has a good chance of being yielded or taking a set after one installation, so it is typically not recommended for multiple installs.
The other options would be Canted Coil and Cantilever V-Spring. Canted Coil’s relatively light and constant load curve, while great for rotary application would not be well suited here. V-Spring would be the correct choice. Good point loading and high resiliency to multiple compressions would be fitting for the application. V-Spring, in most cases, is also the most cost-effective spring due to lower raw material cost and higher run-rates for cutting, welding, and assembling into seal jackets.
With the relatively poor hardware surface finish, spring force would be critical in providing the best seal possible. Eclipse chose to incorporate two nested V-Springs to both increase spring loading and the energized area at the hardware/seal interface.
Turning to the seal jacket, at cryogenic temperatures only a few materials are commonly used. In static situations, typically unfilled or Virgin grade materials are chosen to ensure the best pliability and conformity as possible. PCTFE is known for it’s excellent sealing characteristics and mechanical properties even at temperatures as low as -400°F, but it also very expensive.
Eclipse chose its ET000: Virgin PTFE for the seal jacket material. While being one of the most simple and common materials Eclipse has available, it would fit all the desired characteristics needed for the application. Good elongation and pliability attributes at low temperatures, as well as, being extremely cost effective.
Eclipse also customized the seal jacket design and geometry. The lip thickness was carefully specified to maximize the spring force energy and maintain flexural capabilities. This was finely balanced with the need for high pressure structural integrity of the seal.
How It Performed
Eclipse’s choice of nested V-Springs and a custom ET000 seal jacket proved to be a winning combination. The seal met the customer’s leakage requirements even with their relatively poor hardware surface finishes.
This, combined with a very cost-effective seal itself, helped meet the overall budget goal of the launch system. This positioned the customer to be competitive in an increasingly crowded market of options to leave the planet, proving that great engineering can drive both reliability and affordability in critical aerospace applications.
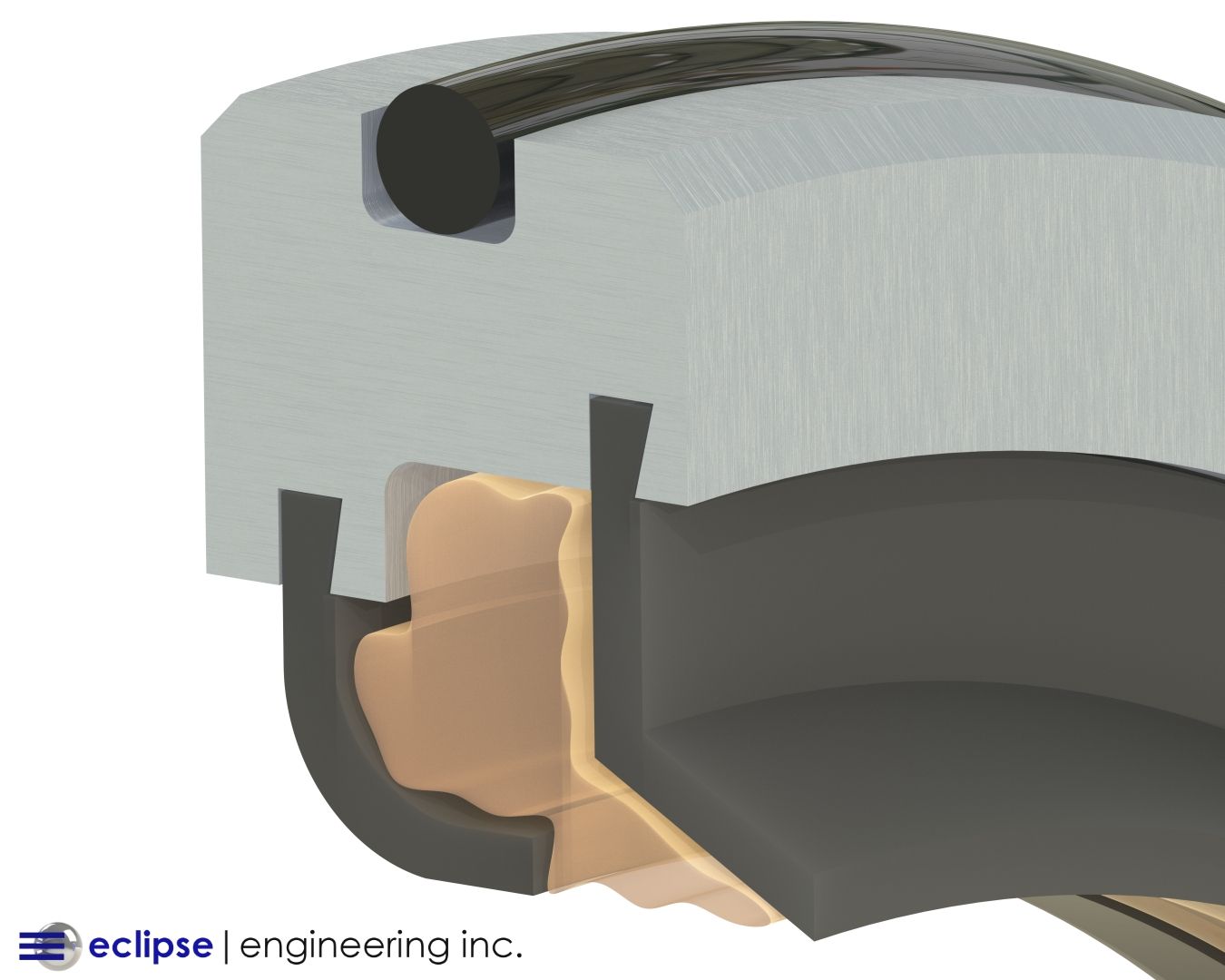