The Ultimate Guide to Seal Glands for Any Project
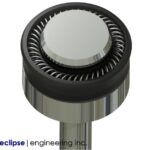
While seal performance, leakage control, and wear-life characteristics are frequently discussed, one critical aspect of a successful sealing system is often overlooked — how a seal is contained in the hardware.
Whether you want to call it a gland or a groove, the physical space for housing a seal is an important part of the system’s performance. The type of gland greatly dictates the ease and even the possibility of seal installation. Certain seals demand specific gland types, so it’s essential to take these requirements into account.
Below we’ll discuss the most common types of rod and piston glands and what seals work best for each one.
Solid Glands

The solid gland is the simplest way to contain a seal. It consists of nothing more than a rectangular groove cut in a housing or piston. Solid glands are prevalent throughout the industry because they’re mostly commonly used to contain O-Rings .
Solid glands work fantastic for O-Rings because they count on the elasticity of the O-Ring for installation. Stretching an O-Ring into a groove on a piston is usually a simple process.
Switch to a much harder and much less elastic material such as PTFE and the task can become quite difficult. PTFE seals such as Eclipse’s ESR Seal Rings and EDS Channel Seals are designed to work in solid glands in conjunction with an O-Ring. This doesn’t mean however, that installation will be trivial.
In the case of piston configurations, the PTFE seal will need to be stretched to be installed into the groove. This can become quite difficult with larger cross-section seals. Special installation tools may be required to evenly stretch and push the seal without damaging it.
Once in the groove, the seal will likely need to be resized to be properly seated. This is due to the inelastic nature of PTFE. Higher modulus materials such as UHMW can be even more challenging.
In rod seal configurations, a PTFE seal will need to be folded in on itself to make it small enough to be placed in the groove. In a process often called “kidney beaning,” the seal is folded as gently as possible to avoid any hard creases which can permanently damage the seal.
Ease of seal installation into a solid gland can be very dependent on the diameter of the seal. At very small diameters it may not even be possible. You should also consider the difficulty of removing seals from solid glands. This often can’t be done without damaging the seal.
Spring Energized Seals are generally never recommended to be used in solid glands. The geometry of the seal jacket contributes to the rigid nature of the PTFE and the risk of yielding or damaging the spring is very high.
Though in some special cases it is possible (like a small cross-section spring going into a large diameter rod gland) but compromises in seal performance and longevity are needed to facilitate this.
Open Glands
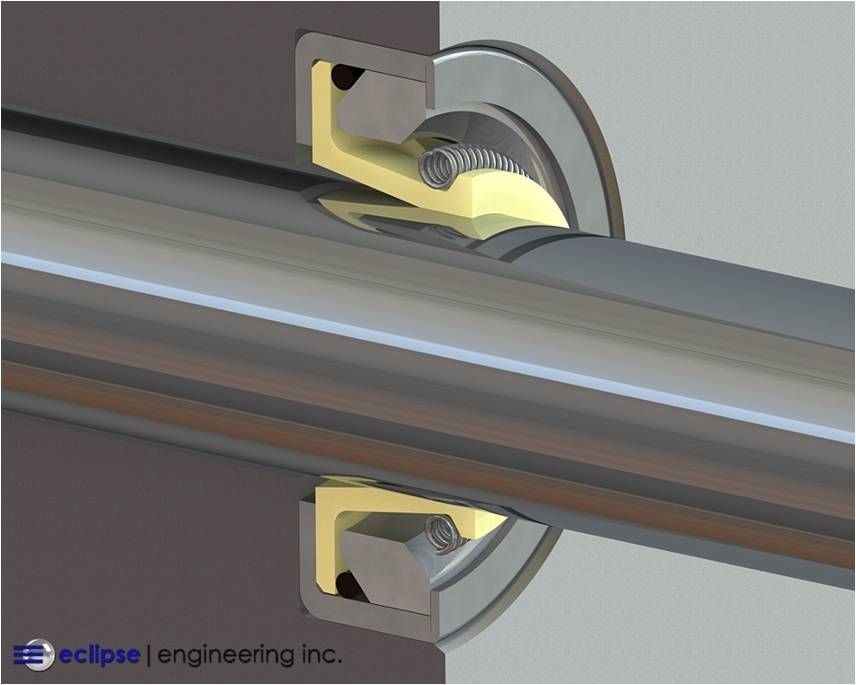
Open glands are essentially a counter-bore in the face of a hardware surface. Since one side of the gland is open, they’re typically reserved for seals with metal cases. The case OD is designed to be slightly over-sized compared to the groove diameter facilitating a light press fit.
The press fit on the case holds the seal in place. Seals without a case have the potential and tendency to “walk-out” of open glands, even in pure rotary applications. Therefore, products like Rotary Lip Seals , Cased Spring Energized Seals , and MicroLips are best suited for open glands.
Split Glands
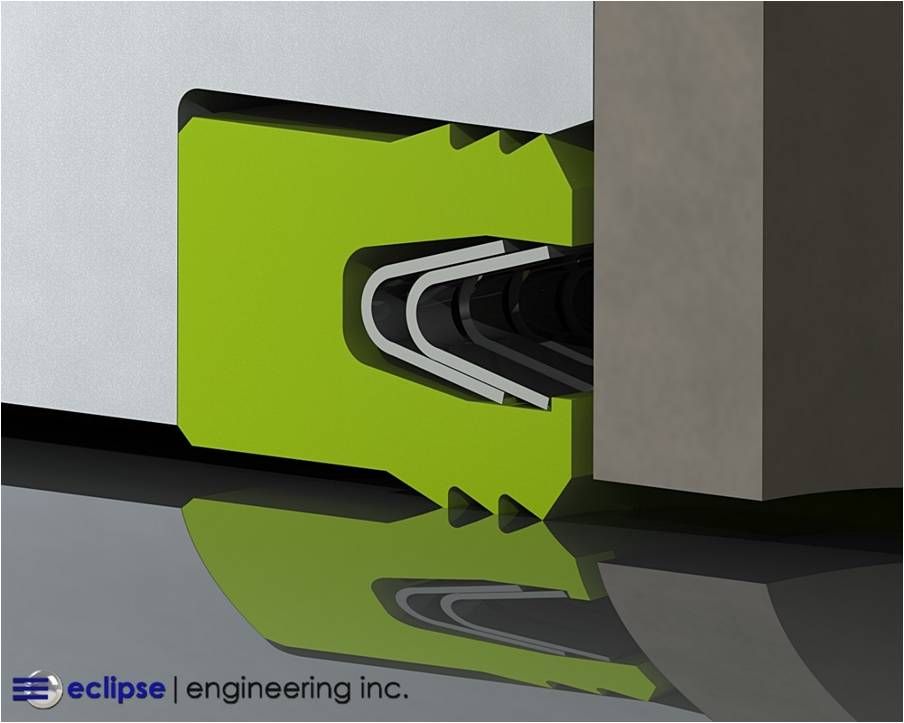
Split or 2-piece glands consist of an open gland with some means of mechanically closing off the open side once the seal is installed. This is commonly accomplished by a simple cover-plate affixed by a bolt pattern.
Split glands offer many advantages. Seal installation becomes as simple as possible with many cases being a “drop in” procedure. Without having to manipulate or contort the seal or use any specialized installation tooling, risk of damaging a seal during installation is largely mitigated.
Removing and replacing a worn-out seal also becomes a straight-forward affair. Seals in high-wear applications that need to be replaced regularly or seals that need to be serviced in the field will greatly benefit from the uncomplicated split gland.
With spring energized seals in critical gas sealing applications and cryogenics, hardware surface finishes typically need to be highly polished for the best control leakage. The split gland makes the polishing procedure in the groove easier since the gland is open.
The main drawback to the split gland is that it requires extra hardware components and fasteners. Not all hardware configurations present uncomplicated ways to split the gland. This is especially true when redundant seals are needed. Solutions such as a seal carrier group can potentially help. Glands can also be closed by using snap-rings in certain situations.
Despite possibly adding complexity to the hardware, some sealing solutions will have no other option but to require a split gland. Very small O-Ring energized seal rings and many spring energized seals cannot be installed in any other gland type without damaging the seal.
Stepped Glands
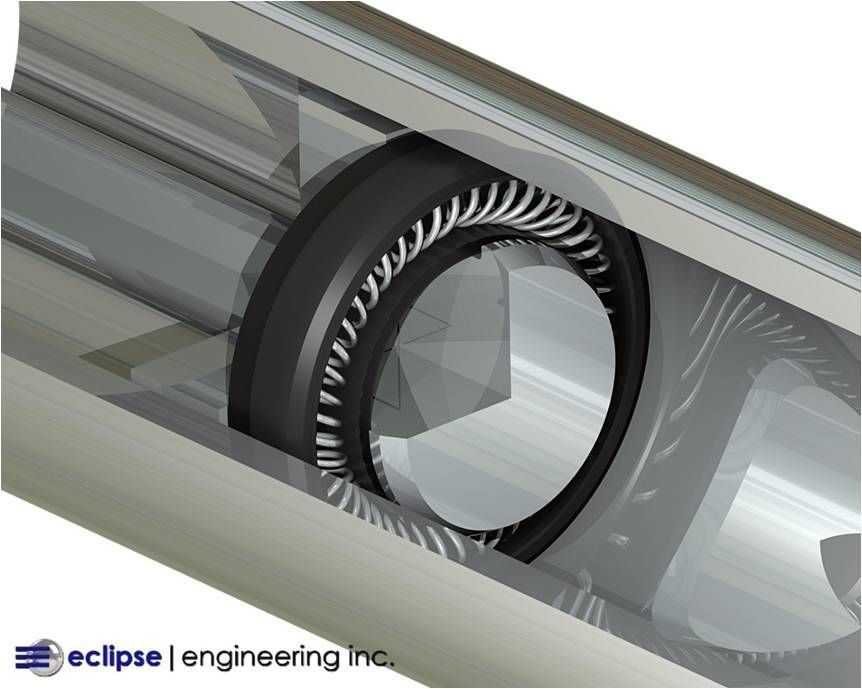
In certain situations, spring energized seals can utilize what’s known as a stepped gland. This is basically an open gland that has a small step or barb that retains the seal on the open side. The seal will need to be installed heel first and the lip will need to be the scraper style to lock in behind the step.
The height of the step will vary depending on seal cross-section and spring size, but it’s usually 0.020” or less. This is all that’s needed to retain the seal, even in demanding fast reciprocating applications. In fact, once installed the seal will be very difficult to remove without damage.
Stepped glands allow for easy seal installation but don’t add any extra hardware components like a split gland. This is the chief advantage of the stepped gland. It’s often employed in piston seal applications where keeping the piston a “1-piece” design is highly desirable.
The stepped gland is relatively difficult to machine in the hardware compared to the other gland types. Small details like chamfers and tool radii need to be carefully controlled to achieve the proper gland dimensions and functionality.
Eclipse is Here to Help
How a seal actually gets put in the hardware is a critical aspect that sometimes gets overlooked. Seal gland requirements can have a large impact on the hardware assembly procedure and overall design.
At Eclipse we have much more than your standard catalog recommendations to offer.
Some of Eclipse’s greatest engineering challenges have centered around seal installation and gland requirements. Eclipse is here to utilize our decades of seal design and manufacturing experience to help specify the best seal and gland configuration for your application.
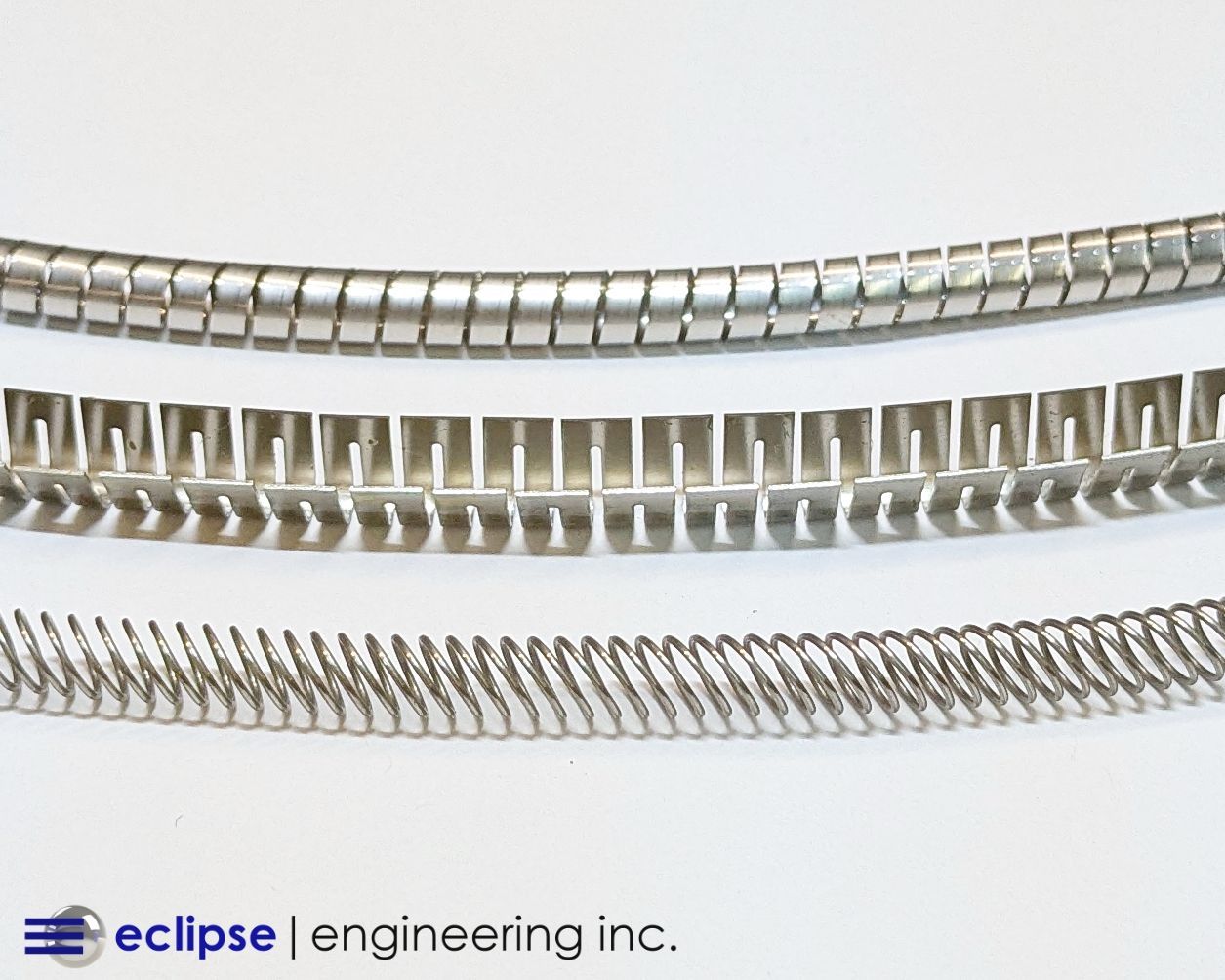