How Pressure Velocity Affects Seal Performance
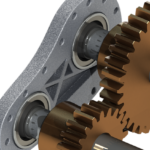
Wondering why that leak you fixed on your equipment just a few weeks ago is back to haunt you? There’s a chance it could be the type of seal you selected.
Your choice of seals has a direct impact on the performance of your equipment. Chosen wisely, the right seal can help prevent leaks, reduce friction, and extend the life of your machines.
There are a number of factors to consider while selecting a seal , including pressure, load, temperature, speed, media (or lubricant) in which they operate, and hardness and surface finish of surrounding materials.
And one of the most significant factors among these is the pressure-velocity, or PV, of your seal.
How to Calculate Pressure Velocity
Seals have a specific range of PV values in which they operate optimally, called the PV limit.
The PV limit for a seal is defined as the highest combination of pressure and velocity at which that seal operates with normal wear. Beyond this limit, the seal experiences severe wear.
It’s important to determine the PV in your equipment to choose the right seal for your application.
For practical applications, the PV limit of a seal also depends on other factors, like operating temperature and compatibility with the lubricant.
PV is given by the product of pressure of the media (in psi) and velocity of the shaft (in feet per minute).
For example, for a reciprocating engine with a 1” rod and a 3” stroke, operating at 100 cycles per minute, with a media pressure of 500 psi –
PV = 2 * [Stroke Length (in ft.)] * [Cycle Rate (cycles/min.)] * [Pressure (in psi)]
In this case, PV = 2 * (3/12) * 100 * 500 = 25,000 psi-ft./min.
For a rotary engine with a 4” rod, operating at 1000 rpm and 50 psi,
PV = [Circumference (in ft.)] * [Speed (in rpm)] * [Pressure (in psi)]
For this example, PV = (4/12) * 1000 * 50 = 52,360 psi-ft./min.
PV Values and Seal Choice
It’s easier to choose the type of seal for your application once you’ve determined the PV value.
Eclipse offers a variety of seals for different applications — Rotary Lip seals , Spring Energized seals , O-Ring Energized seals.
The following charts illustrate the seals best suited for specific PV values:
Dynamic Applications of PV Values
Reciprocating
PV Range | Type of Seals |
< 1,000 | X Ring (Rubber) V-Packing (Rubber, PTFE) |
1, 000 to 10,000 | U-cup (Rubber, Urethane) O-ring loaded U-cup |
10,000 to 100,000 | Cap Seal (PTFE, O-ring Energizer) Spring Energized seal (PTFE / SS) |
> 100,000 | Cased Spring seal (PTFE / SS) System design / Mechanical-type seals |
Rotary
PV Range | Type of Seals |
< 1,000 | Radial Lip Seal (Rubber, Cased) |
1, 000 to 10,000 | Spring energized seal (PTFE / SS) |
10,000 to 100,000 | Roto seal (PTFE, O-ring Energizer) Spring Energized seal w/ O-Ring |
> 100,000 | Cased Spring seal (PTFE / SS) PTFE Lip Seal System design / Mechanical-type seals |
Static Applications of PV Values
Pressure/Temperature | Type of Seals |
Pressure < 5,000 psi Temperature between -40 degree F and 400 degree F |
O-ring w/ back-up ring U-Cup w/ back-up ring Spring Energized PTFE seal (in case of issues with chemical compatibility) |
Pressure > 5,000 psi Temperature below -40 degree F or above 400 degree F |
O-Ring or Flat Gasket |
In general, at higher temperatures, the PV limit and pressure rating decrease and wear rate increases. Anything that can reduce heat generation, such as the presence of a compatible lubricant, reduces seal wear and aids prolonged operation at high PV.
Spring Energized Rotary seals are usually employed in high-pressure, low-speed applications, while Cased Lip seals are more suitable for low-pressure, high-speed applications.
Pressure-Velocity Curves for Spring Energized Rotary and Cased Lip seals
Important note: Any PV values to the right of the curve fall under the severe wear zone, while those to the left of the curve belong to the mild wear zone.
Eclipse Spring Energized Rotary seals
Pressure (in psi)
Velocity (in surface feet per minute)
Eclipse Cased Lip seals
Pressure (in psi)
Velocity (in surface feet per minute)
Ideally, rotary seals should stationary, and shouldn’t rotate in their glands. Seal rotation increases wear and could cause leakage of the lubricant.
To prevent unnecessary wear, the spring load on rotary seals should be just enough to ‘lightly compress’ the seal and achieve a good fit.
The seal needs to be in contact with a smooth surface like that of a shaft (and not with a relatively rough surface like the housing), so that the joint is ‘plugged’, preventing potential leakage of the lubricant.
Choosing the Right Seal for Your Application
PV values play a critical role in seal-selection. While selecting the right kind of seal is crucial, it’s also important to install and maintain the seal effectively to maximize its shelf life.
Poor installation and inadequate maintenance could result in leakages and accelerated wear.
But these issues are easily remedied by thorough understanding of the various kinds of seals, sealing materials and seal-selection considerations available. That’s where Eclipse comes in.
As the only seal manufacturing company that also specializes in engineering, we can help you determine if a standard off-the-shelf product would fit your needs, or if an engineered solution is necessary to get the job done right.
Eclipse can produce the exact seal, bearing or spring that you need. We also carry a wide variety of materials including plastic, rubber, nylon and thermoplastic elastomer, and can manufacture a product unique to your needs. Contact us today to find the best seal solution for your next project >
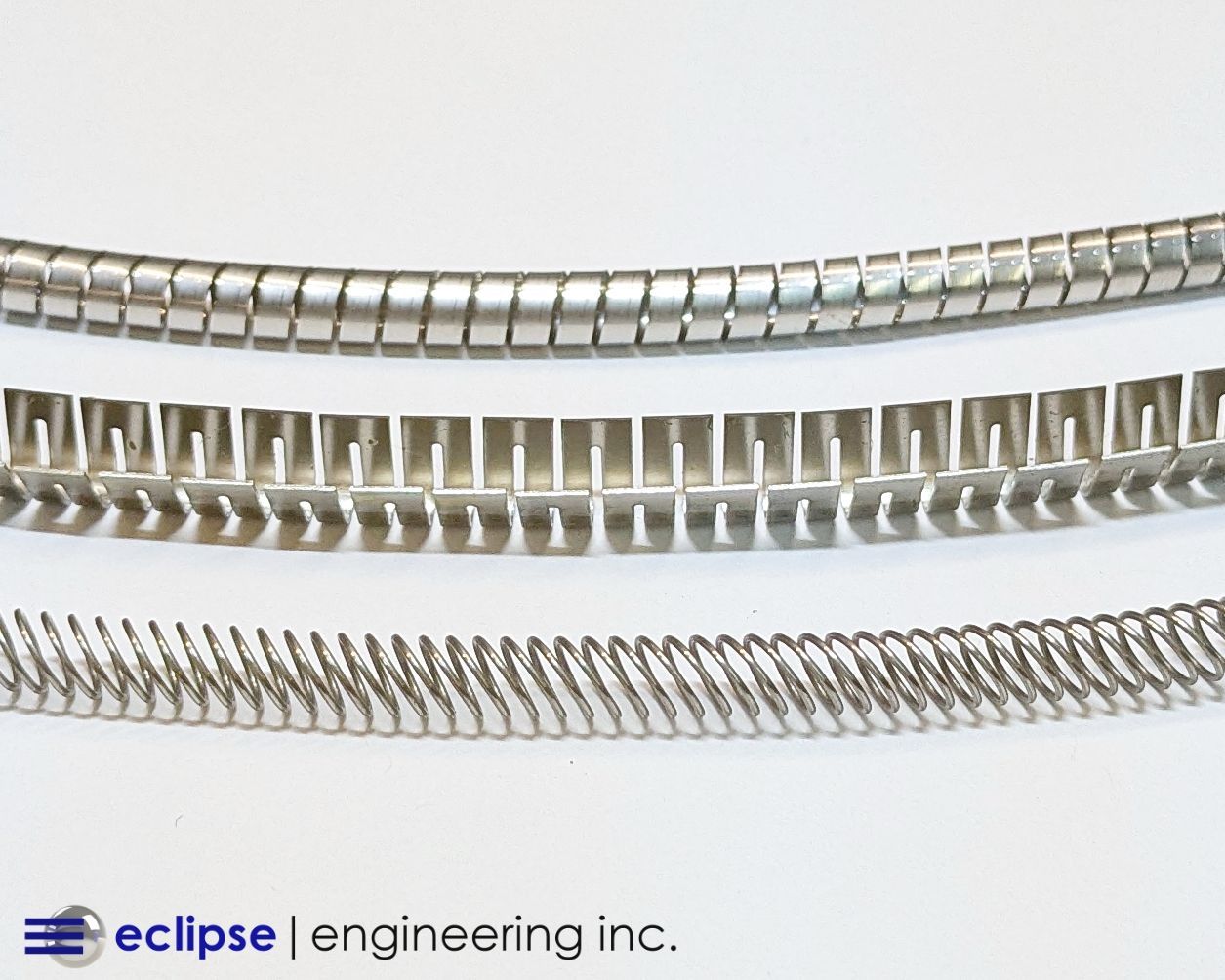