EZ032: An Extreme Material for Extreme Applications
Every day, Eclipse works to push the limits of engineering and product requirements in a variety of industries. As surface speeds and temperatures are driven to extremes, wear resistance becomes an increasingly important factor to ensure long sealing wear life.
While heavily-filled PTFE materials such as glass/carbon/PPS blends have been available for years, even these have fallen short of expectations in the most demanding applications presented by our customers.
Luckily, Eclipse has a new material weapon at our disposal to meet the challenge: our EZ032.
What is EZ032 and What Makes It Special?
Eclipse’s EZ032 is a high-percentage fill blend of carbon, carbon fiber and Modified PTFE.
Proprietary blending technology is used to evenly disperse carbon and fiber fillers throughout the base resin imparting wear resistance and high temperature capabilities.
What makes EZ032 a unique material is how the resin blending allows for a high level of fillers to be added without degrading the properties of the base resin.
Typically, higher filled resins don’t lend themselves to being used in seals. In the case of EZ032, the desired properties of pliability and resiliency still remain, making this material useful in critical sealing applications where high pressure-velocities are present.
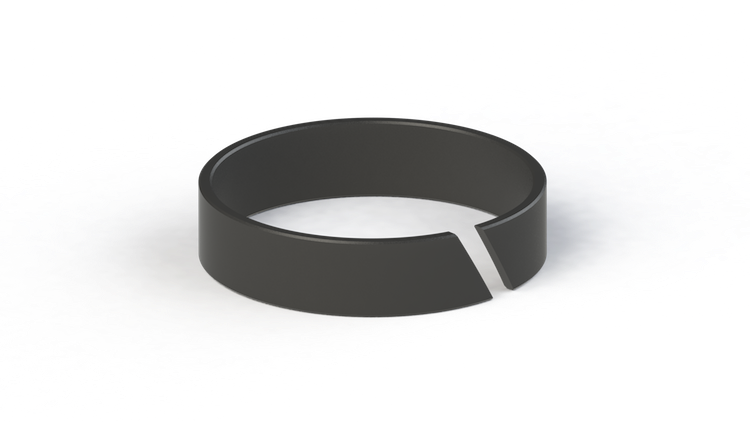
Where Should EZ032 Be Used?
Where wear or temperature resistance is the name of the game, EZ032 should be considered.
Eclipse has specified EZ032 with great success in linear bearing applications running continuously at 575°F and rotary sealing applications with Pressure-Velocities above 150,000.
With EZ032, Eclipse has manufactured effective solutions for multiple downhole rotary sealing applications where surface speed, temperature and abrasive media were too much for other materials.
Switching to EZ032 in a certain gear pump application increased seal wear life over 20%, which means 20% fewer rebuilds and associated downtime. That also means increased profitability for your team.
Contact Eclipse today to see if EZ032 can make a difference in your extreme applications, including the following:
- Gear Pump Seals
- Mechanical Face Seals
- Downhole Seals
- Wear Rings and Bearings
- Gearboxes
- Compressors
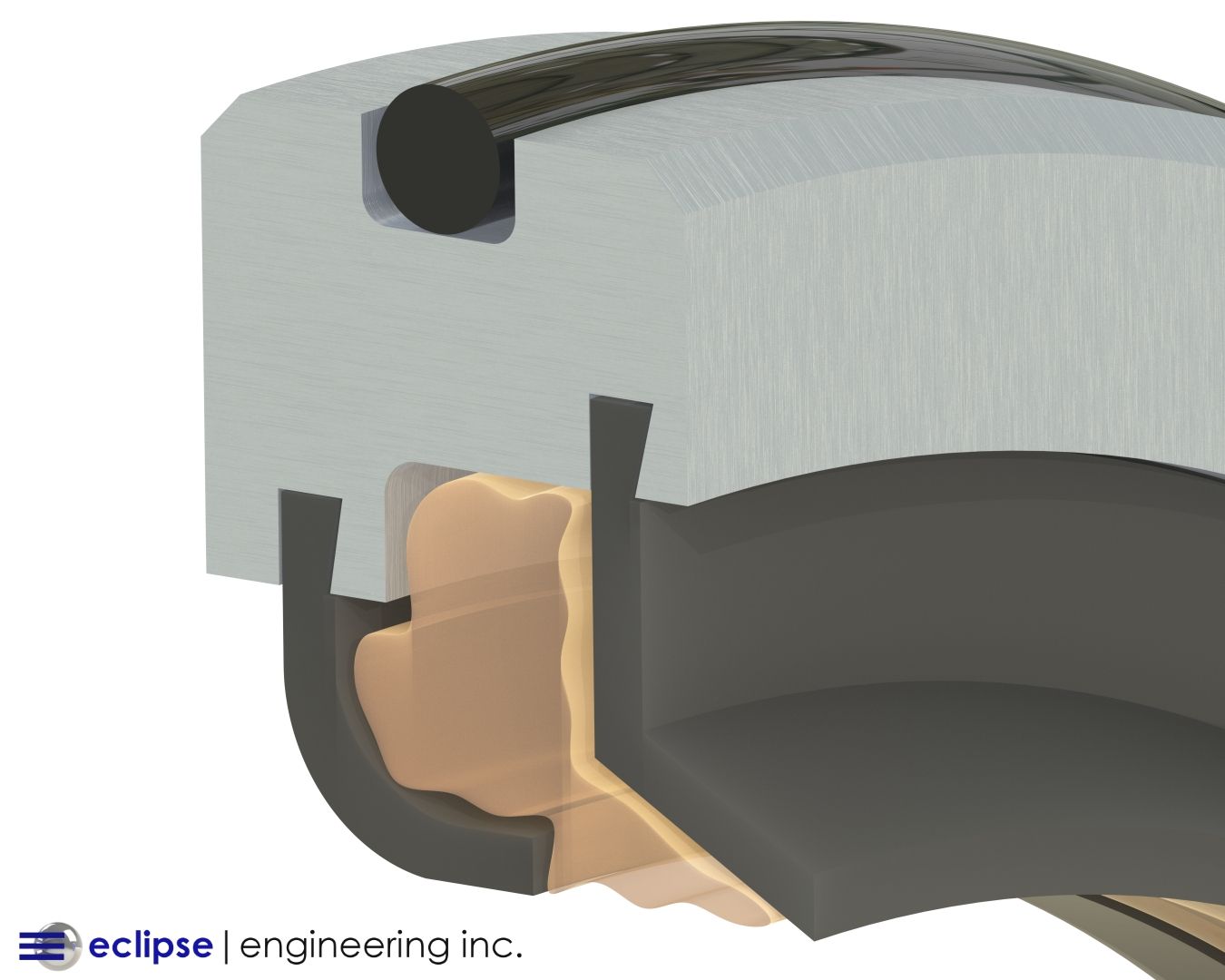