The Many Uses of Polytetrafluoroethylene Seals
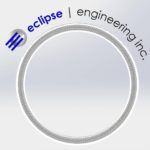
Better known as Teflon in the industry, Polytetrafluoroethylene is widely used in practically every industry on and off the planet (and even beneath its surface!)
Medical Uses
This material’s primary claim to fame is its resistance to most chemicals. It inherently has an extremely low coefficient of friction, it’s easily machined from rods, tubes or compression molded shapes.
It’s one of the few polymers that are approved for medical implants due to its inertness to bodily fluids — the immune system principally ignores its presence in the body.
Moving away from the body, you’ll find PTFE or Teflon products in medical devices such as heart lung machines, rotary tools for cutting, and sealing devices for maintaining fluid streams for irrigation and pumping. Tiny fragments that may come loose during usage are not harmful to the body, and simply pass through the system.
Pharmaceutical Uses
In the pharmaceutical industry
, Teflon is used in the processing of drugs for equipment used to manufacture such as mixers, presses, bushings. Teflon is found in a variety of applications, as any debris from the seal will pass through the body without consequence.
When considering press machinery (which are often water driven to ensure any leakage will not spoil the product), Teflon seals are often used to help reduce friction — especially in repetitive presses where a build-up of heat would be detrimental to the seal and the product.
Food & Beverage Uses
Mixers are another area to insure keeping grease and other contaminants from the motor to not descend into the product from the mixer shaft.
Another area is pressure vessels where two shells are clamped together to ensure product remains sealed inside. Failure of these seals usually results in loss of product.
Non-metal bearings that don’t requiring grease in rotary motion are an excellent place for Teflon style bushings. These bushings provide long life with very low friction while not contaminating the product. Shaft wear from the bushing may be eliminated with the use of Teflon.
Types of Polytetrafluoroethylene Seals
Seals in the medical field can be as simple as a static O-Ring , or a mechanical face seal which is costly and requires special consideration during installation. Most dynamic applications can be resolved with spring-energized style seals, which often have very low friction and can be clean in place (CIP) if required.
There are different styles of springs, such as cantilever or canted coil that provide varying loads. The cantilever-style spring-energized seal provides a linear load based on deflection providing a high level of seal-ability. It can be silicone-filled to provide CIP for ease of washing, and there are a variety of materials that are FDA compliant and that work well in both viscous and pure aqueous fluids.
Canted coil spring-energized seals provide a unique feature of controlling the load the spring exhibits on the sealing element. This allows for control of a device being manipulated during a procedure.
The polymer properties give the user materials with the lowest possible friction, while still sealing in an application. The load from a canted coil spring allows the user to feel a tool in a catheter while passing the catheter through a tube, and still retaining a seal.
Eclipse’s Unique Production and Design Capabilities
Eclipse Engineering manufactures a variety of products for the medical/pharmaceutical industry. Our engineering staff designs product to meet your exact need.
We often find ourselves designing in the MRO market at small volumes to meet a user’s needs. This often occurs with equipment manufactured offshore.
Replacement parts may either have long lead times, or are not available. We often find the OEM doesn’t recognize the problem the user is having. Our design/manufacturing team will often produce a product with longer life in much shorter lead times.
When designing a product, it’s not just a case of creating a copy of what the customer is using, but understanding the need for product improvement which requires an understanding of how the equipment is utilized.
Eclipse Engineering’s staff is trained to work with the customer, to understand the application and design a replacement that will reduce critical down time while not compromising the application and its performance.
We manufacture onsite, which allows us to respond to your equipment needs in quick fashion, so you can meet your deadlines. And depending on the need, this could occur in as little as hours.
Eclipse can tool grind onsite, which allows us to design and build specialty tooling as required for a job. Our engineers are trained on most polymers that are available in the marketplace giving us the opportunity to select the right material for your particular application.
As an Employee Owned Company, our staff is dedicated to insuring your needs are met in a timely manner as they have a vested stake in the outcome. Contact us today with your next polytetrafluoroethylene seal project »
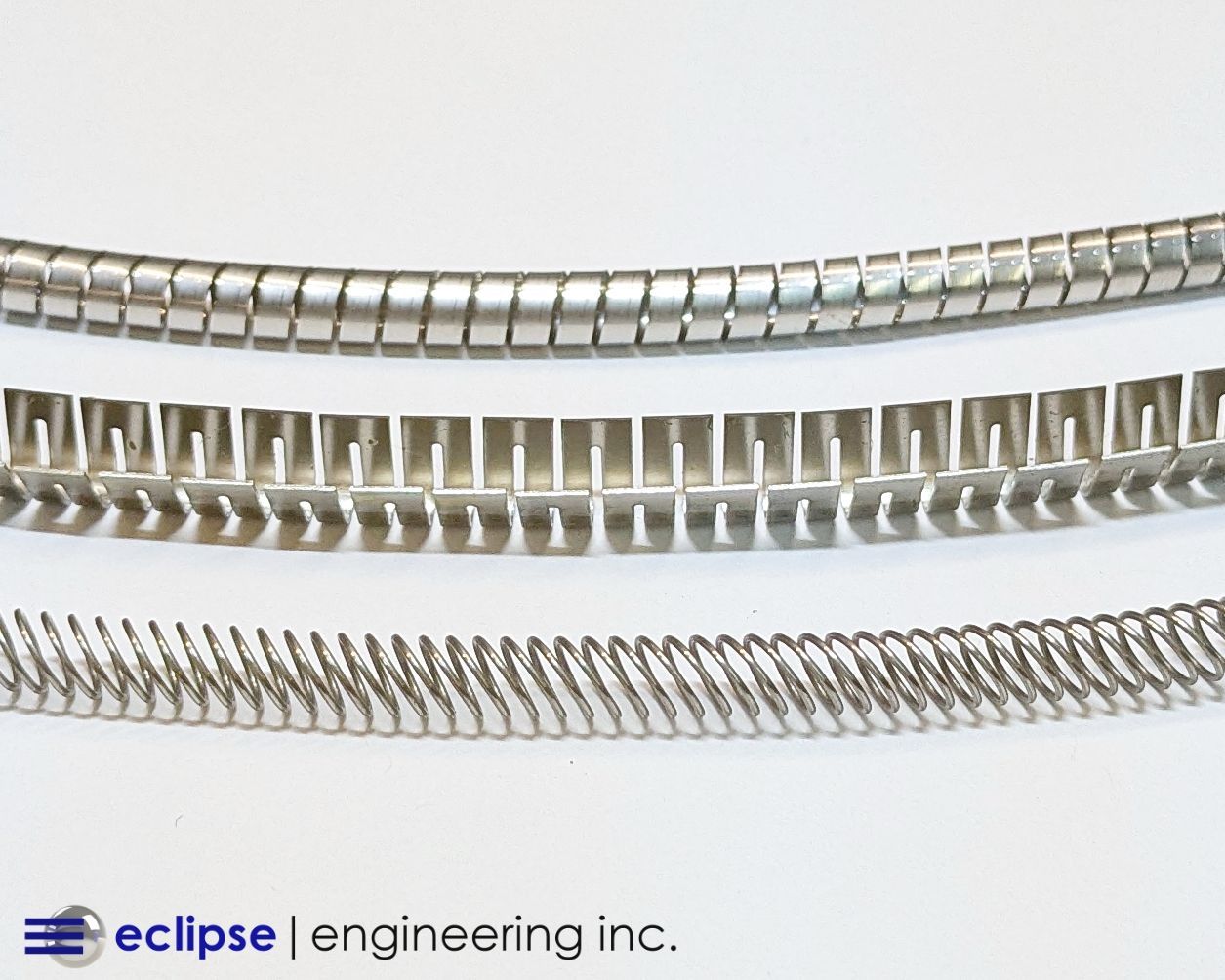