How (And Why) to Choose the Right Seal for Electric Motors
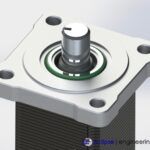
The current global electric motor market is valued at more than 100 billion dollars and is slated for continued growth in the decades to come.
It’s estimated that more than 30 million electric motors are produced every year. The increased development of robotics and automation in many industrial processes as well as demand for numerous consumer applications continues to fuel growth.
The recent push and increased adoption of electric vehicles, including everything from electric bicycles to automobiles is a prime example of the expanding need for electric motors. As we’ll see, the sealing requirements can be very different for an electric motor compared to a seal in a traditional internal combustion engine.
New technologies and applications also find electric motors serving new purposes and creating new requirements. Eclipse is at the forefront of meeting the unique sealing needs of the electric motor industry.
High Speed, Dry Running
Electric motors have many advantages over an internal combustion engine. We won’t discuss the extent of them here, but an electric motor’s few moving parts and limited friction points mean there’s no need for internal lubrication. This is in obvious contrast to an internal combustion engine which is filled with pressurized, circulating oil.
The dynamic shaft seals in a traditional gas or diesel engine are aptly named “oil seals” as they both keep oil or grease inside and the external environment out.
An oil seal usually consists of a stamped metal case over-molded with an elastomeric or rubber material to create a sealing lip. The metal case facilitates a press-fit in the hardware, while the lip rides on the shaft creating a seal.
Oil seals utilize the system oil to both lubricate the backside of the lip and to help keep localized heating in check. Without this lubrication, a traditional elastomeric oil seal will quickly overheat and fail.
Unfortunately, dry running capability is exactly what an electric motor typically needs. Any electric motor operating in an outside or unclean environment likely needs a primary shaft seal to keep dust/debris/water or possibly lubricants from other systems components from getting into the internals of the motor. Containing often highly charged electrical components, contaminants or fluids can quickly foul the motor operation.
To compound the difficulty of seal dry running, electric motor speeds are often much higher than internal combustion engines. Current production motors in electric vehicles can spin as fast as 18,000 rpm.
This is about 3 times higher than the maximum speed of most automobile gas engines. Smaller motors in other applications can run at even higher speeds.
As enhanced electric motor design continues to develop, along with the utilization of advanced materials, higher and higher motor speeds are expected. This is done in the pursuit of further efficiency as a motor with higher speed capability can better exploit advantages in mechanical gearing.
The seals in the motor will need to survive high-speed running and provide extended service life demanded by consumer products all without lubrication.
Low Friction
One of the other often stringent requirements for electric motor seals is extremely low running friction. The drag created from seals is never a desirable attribute, but the electric motor applications heighten the need for as little frictional loss as possible.
In battery-powered applications, such as electric cars, any friction created by the seals translates into efficiency losses in the power output of the motor. If the motor is working harder due to this, more energy is expended to move the vehicle forward and more of the battery is being used.
One of the chief concerns with electric cars is the available range per charge of the battery. It’s a major selling point to extend the range as much as possible, and manufacturers are looking to reduce inefficiency losses in every possible way. The motor seals will be a contributing factor in these losses, so the lower the friction, the better.
Another industry that frequently requires low friction motor seals is precision robotics and automation. Motor size can be limited due to space constraints.
For example, a motor that needs to be housed within an articulating robotic arm will have constraints for both physical size and weight. Low friction seals help make sure motor power is maximized so the smallest and lightest motors can be utilized.
Another important characteristic related to low friction seals is the smoothness and consistency of the dynamic motion. A robot responsible for placing electrical components on a circuit board requires high precision and very fast starting and stopping motions.
Rubber or elastomeric seals can exhibit what’s often called “ stick-slip ,” which is a function of the static friction being much higher than the dynamic friction. The resulting jerkiness is not desirable in these types of applications.
Eclipse Has the Solution
If you need a long-lasting seal, capable of high-speed, smooth dry running operation with very little friction — a PTFE seal is what you need.
While this can take many forms, electric motors most often utilize Cased PTFE Lip Seals. The metal case, usually stainless steel or aluminum facilitates an OD press-fit into an open gland much like an oil seal.
Eclipse can design a PTFE cased lip seal to retrofit most oil seal glands.
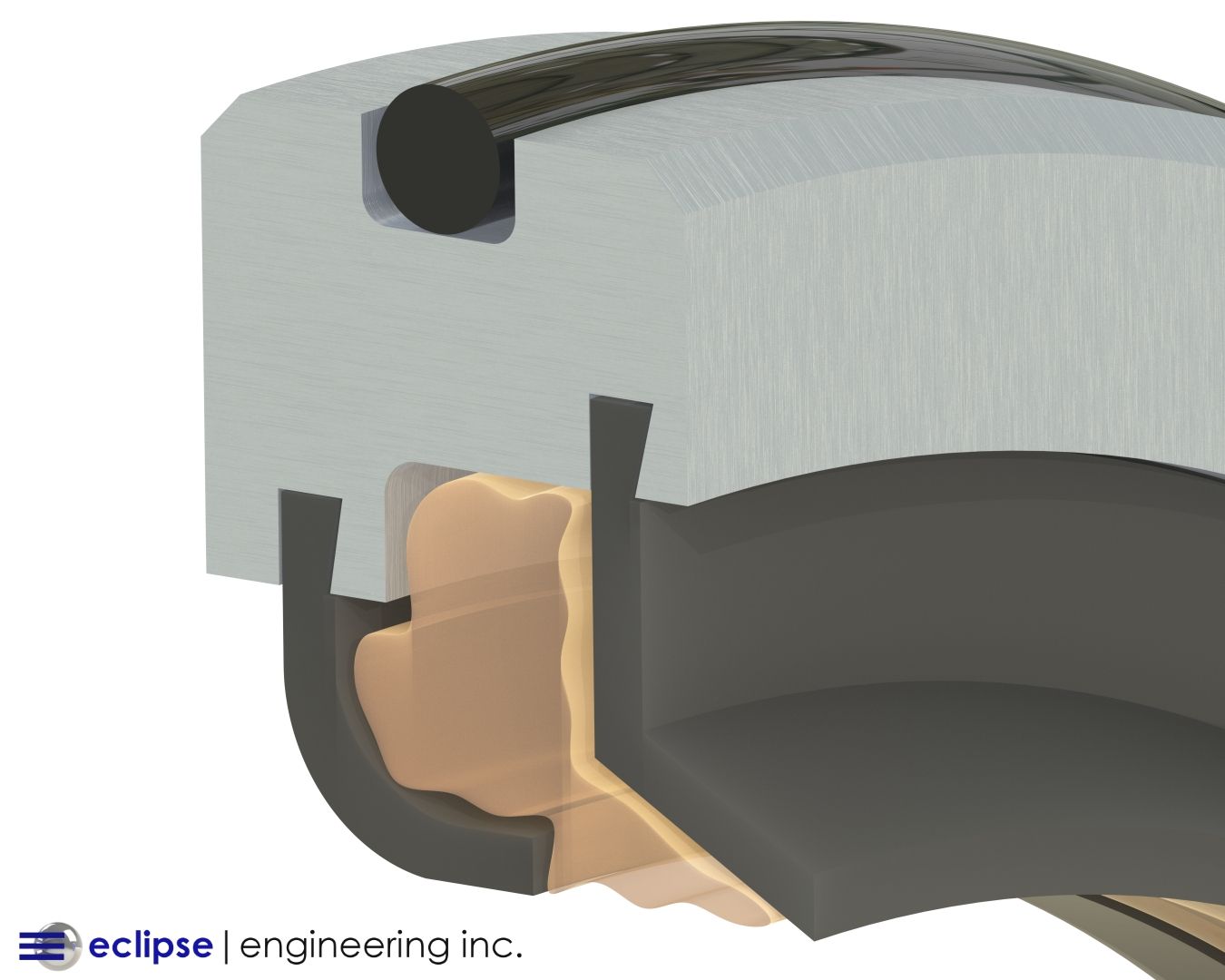