How to Use Tight-Tolerance PTFE in Your Next Manufacturing Project
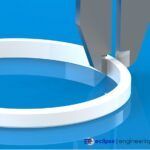
Author: Doug Montgomery
The machining of polymers such as PTFE, still remains somewhat of a specialty operation. While there are a plethora of machine shops dotted across the country focused on metal turning and milling operations, few specialize in plastics.
Only someone experienced in metalworking might call machining something like PTFE easy. PTFE is much softer and easier to cut than something like steel or aluminum.
While this certainly is true, polymers present their own unique set of manufacturing challenges, especially when tight-tolerance parts are required. And with Eclipse’s business of aerospace and specialty applications , they almost always are.
Though Eclipse designs and engineers the majority of the parts it manufactures, we still frequently entertain the machining of customer-designed seals and components. But customer prints tend to include dimensional tolerancing not suitable for process capability with PTFE and other polymers.
Calling out a +/-0.001” on a 15” OD isn’t very realistic. We’ll also see why in many cases, tight tolerances are not necessary for seal functionality and are likely driving up costs.
To help you with your next project, here’s our guide to PTFE and the challenges it can present while manufacturing.
The Inherent Instability of PTFE
PTFE has lots of unique and desirable qualities as a seal material. Its extremely low friction, broad chemical compatibility, and large temperature tolerance make it function where many other materials don’t.
One not-so-desirable property of PTFE is its non-uniform coefficient of thermal expansion over different temperature ranges. And more specifically, the unfortunate large transition it sees at common room temperatures.
The linear coefficient of thermal expansion of PTFE between the temperatures of 65° to 77°F can be more than 5 times higher than the coefficient in only slightly higher or lower temperature ranges. Therefore, a tight tolerance part machined in a room at 70°F will likely measure small if later inspected in a room either 60°F or 85°F.
So, a part received just off the delivery truck in the middle of winter will probably not measure in spec until brought up to room temperature. Eclipse assumes that part inspection will be done at approximately 70°F.
While this jump in thermal expansion might be an inconvenience for part inspection, it can create a significant challenge in the actual machining of the part. Localized heating from the cutting of the material can transition the part into different thermal expansion zones.
This is especially true in very large diameter PTFE parts where it’s not practical to use coolant while turning. A part measured right off the machine will be significantly different than when it’s measured a few minutes later. Eclipse’s experienced machinists are keen on this challenge and know the needed adjustments to produce the correct part.
Measuring Non-Rigid Parts
One of the most difficult aspects of machining PTFE parts is the inspection of the parts themselves. Most PTFE seals feature a thin aspect ratio that means the diameter is non-rigid and very flexible.
This presents a challenge when using common measurement tools such as calipers and micrometers. Not only will the part simply flex with any contact pressure, but any out-of-round aspects of the part will be very difficult to account for.
Eclipse uses a Visual Measurement Machine (VMM) to precisely measure diameters. The VMM works much like an optical comparator but can take hundreds of measurements to determine diameter. This provides very accurate measurement and takes into account any out-of-roundness.
While the VMM is a great tool for precise measurements, it’s limited to parts 12 inches in diameter or less. Larger parts become increasing more difficult to measure as the diameter increases.
Eclipse has turned to go/no-go gauges to aid in the measurement of tight-tolerance, thin PTFE parts that are large in diameter. This is the best way to ensure roundness is fully considered while measuring.
Tolerance is What Matters
The diameter of parts is usually the most challenging dimension to hold and inspect, especially for large components. But in most cases, the diameter of PTFE seals is not the most critical dimension for functionality.
Take a standard piston seal ring. The functionality of a seal ring comes from the radial cross-section of the seal compressing the O-Ring beneath it. The squeeze on the O-Ring provides energy to the PTFE ensuring constant contact force with the bore and thus providing a positive seal.
Therefore, the cross-section of the seal is really the most important dimension to hold tightly. Similarly, the cross-section, or lip-to-lip dimension, of a spring energized is what determines the spring compression and general functionality of the seal.
So again, this dimension is predominately the most critical aspect of tolerance.
Fortunately, the cross-section is also the easiest dimension to machine precisely, inspect with common instruments, and is proportionally less affected by any thermal instability. Because of this, Eclipse usually focuses its attention on this dimension rather than diameter.
In the case of products such as standard seal rings , many times these are installed in solid glands. This means the seal must be physically stretched to be installed. It’s not productive to tolerance the diameters needlessly tight if the part is only going to be deformed and resized later.
Tight tolerances, particularly on diameters, can also unnecessarily drive up costs by slowing machine run rates. Yes, the VMM can provide very accurate measurements but it’s also not an “in-process” inspection method. The machinist must stop the lathe and go to the inspection room to get a measurement.
Get the Best Quality Engineering With Eclipse
Difficult or time-consuming inspections might be one thing, but Eclipse also knows some tolerance requirements will not be possible to meet.
Through years of experience, we know what tolerance ranges will ultimately be processing capable with a material like PTFE.
Our knowledge is all the more valuable when in-depth capability studies, such as a Level III PPAP are required.
We’re here to work with you to ensure your parts are not only in tolerance but are highly functional and cost-effective sealing solutions.
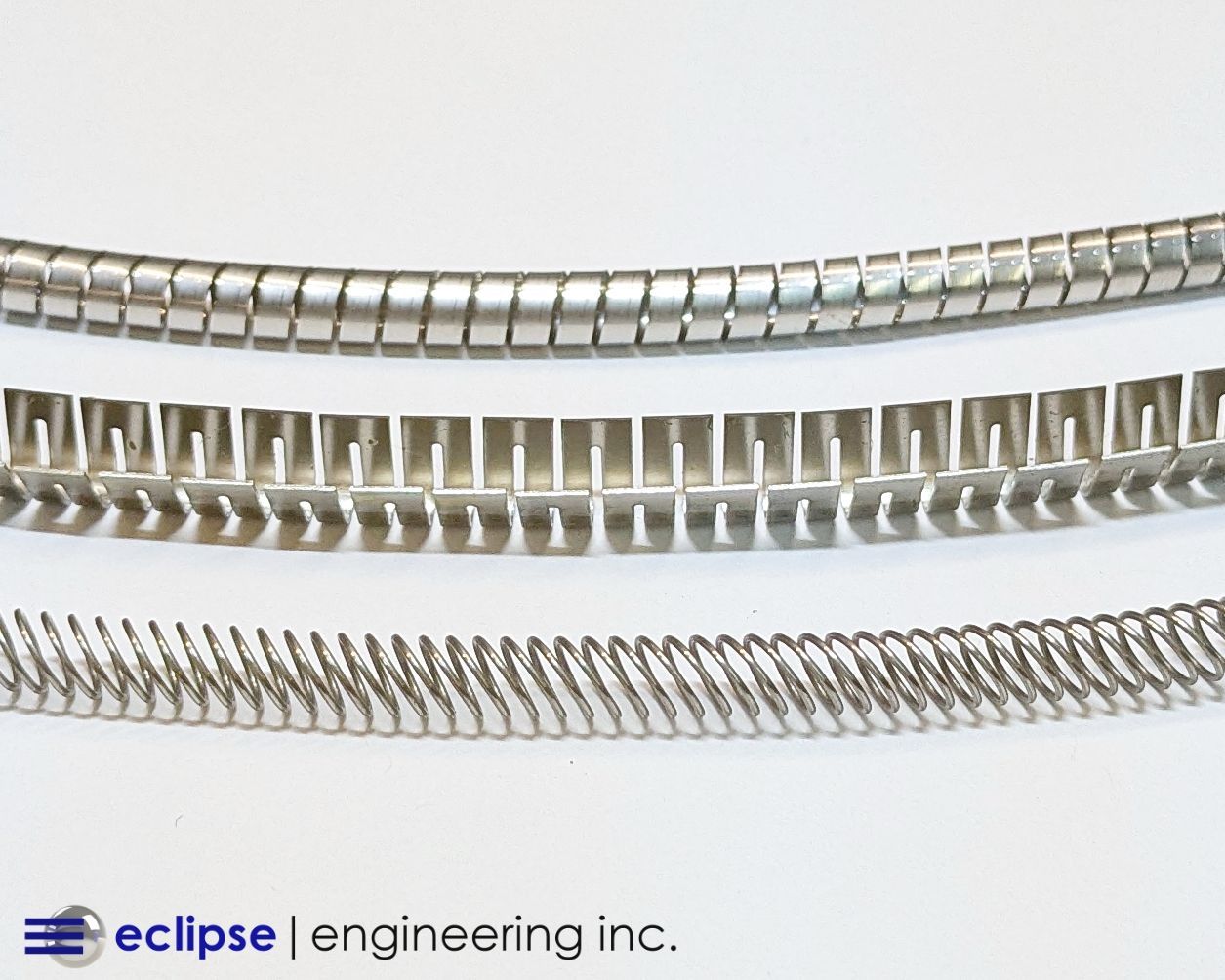