Best Sealing Materials for Epoxy Resin
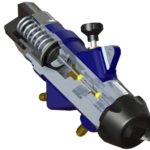
Sealing viscous fluids like epoxy resins requires a seal that contains enough force to ensure a good scraping action, while not overloading the shaft you’re trying to seal. This is often accomplished by selecting the best spring that will continue to be reactive, regardless of the fluid.
This means selecting a spring material that can successfully handle the following challenges:
- Maintain a sharp edge to ensure a good scraping action
- Ensure no fluid will pass under the lip
- Exhibit a relatively low coefficient of friction
- Won’t damage the shaft due to high unit loading
- Won’t contaminate the chemical reaction when used in combination of a mixing head for two part mixers
Temperature is sometimes also a factor in sealing, which means some seal materials aren’t suitable for these tasks. And of course, the chemistry of the fluids can’t interact with the spring or the seal.
The seal must be rigid enough to stand up to all the above conditions, and at the same time be flexible enough to be installed, and reactive to some side-loadings.
Best Seal Material for Sealing Epoxy Resins
We generally turn to two different seal materials: PTFE or Teflon , and UHMW or Ultra High Molecular Weight Polyethylene.
There are many differences between these two materials. The UHMW tends to be very stiff, and thereby does an excellent job of scraping. However, it’s often limited by temperature, and some fluids can react with it, although most epoxy resins don’t interact with UHMW.
On the other hand, Teflon is far more compliant than UHMW, has a broader temperature range, and chemical resistance is almost never an issue (especially with epoxy resins).
So how do you choose which seal material will work best for your needs? The answer boils down to a few factors: Temperature, which relates to speed (especially in rotary applications), and how well the seal will scrape off the shaft.
Speed in Epoxy Seals
Teflon performs better at high speed. But UHMW holds an edge better, which means it ultimately does a better job at scraping.
Springs are generally not an issue, as few chemicals in epoxy resins will affect stainless steels. But the type of spring you use is very important. You can expect that the fluid will completely cover the spring, so the spring force needs to stay unaffected by metallic springs.
The cantilever spring generally offers the best solution, as it allows the fluid in and out of the spring cavity, where other springs tend to hold the fluid, thereby affecting the overall spring force.
The cantilever cavity can be filled with silicone to close off the cavity. This keeps the viscous fluid from impacting the performance of the spring in the application.
Beyond a cantilever spring, other types of energizers tend to not do as good a job in overall performance. This includes O-rings , which are often affected by the fluid, or round springs like Helical , which tend to trap the fluid in the spring cavity.
Fillers for Epoxy Resin Seals
There are fillers that we apply to UHMW to enhance the performance and extend the life. They generally cost a bit more to produce, as they wear tools and could impact the shaft finish and wear life.
Teflon is always an excellent choice with the correct fillers selected. But again, Teflon doesn’t hold an edge for scraping.
While Teflon and UHMW are great choices for sealing and spring materials, these aren’t interchangeable due to the nature of the polymers and the desired result.
If we seal after the two-part epoxy is mixed (prior to leaving the head), we need to be prepared to clean or flush the seal quickly (prior to the compound hardening in place). Our selected seal material must be able to stand up to some of the harshest cleaning fluids and resist chemical break down during the cleaning process.
Rotary Applications for Epoxy Seals
Rotary applications are both easier and more difficult. We often see rotary during a mixing process, and Teflon will handle the increased shaft temperature much better than UHMW. And without the reciprocating action, the rotary seal only needs to provide enough downward force to not allow the fluids to push up the lip during operation.
The reciprocating action tends to want to draw or drag fluid past the seal. That’s why the edge and force on UHMW works so well. Whereas in rotary, no fluid is being drug under the lip, so penetration of the boundary is much more difficult.
Eclipse has designed seals at less than .062 inch (1.5mm) for many reciprocating applications with various types of seal materials to accommodate size, installation and operation of the Epoxy Pump mechanism.
We have also designed a series of rotary seals, all of which can be CIP or clean-in-place sealing elements.
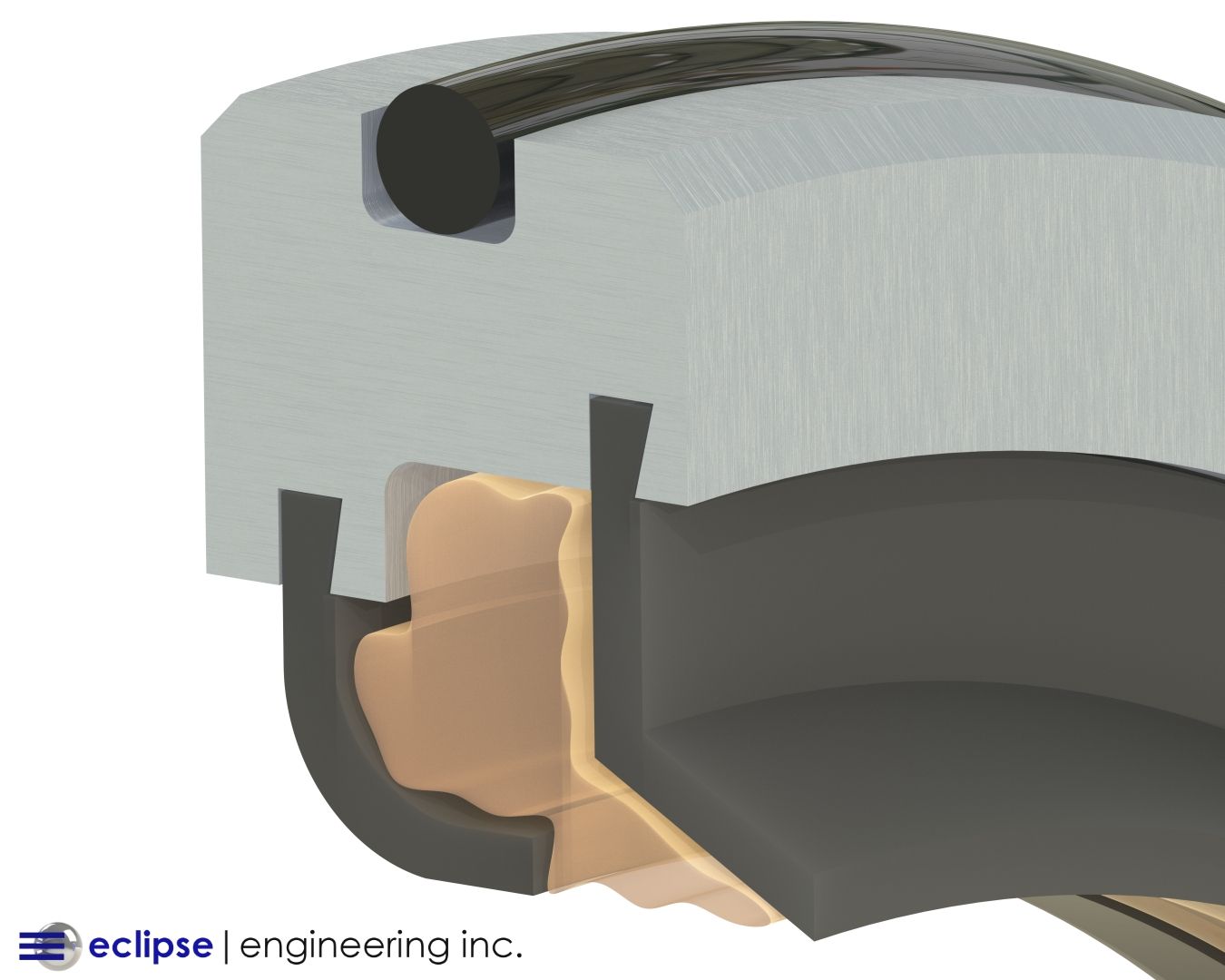