5 Polymer Bearing Configurations and Their Advantages
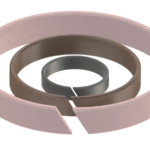
Polymer wear rings were developed to offer an alternative to dissimilar metal wear rings.
One of the advantages to using a polymer material such as nylon or filled-Teflon instead of a metallic bearing is that the load may be spread out over a broader area. Whereas when you use bronze or metallic bushings, these materials are prone to point loading on the edges of the bearing.
This property of polymer bearings combined with solid lubricants can yield a product that is much less likely to damage moving components.
5 Advantages to Polymer Wear Rings
- Polymer style bearings can be held to very close tolerances in the radial dimension to provide support without excessively opening the extrusion (E) gap by a large amount.
Polymer bearings such as filled Teflon can support a compressive load up to 1000 PSI. Nylons up to 36,000 PSI and polyester fiber with resin, up to 50,000 PSI. - Hydraulic cylinders that are found in excavators often use the higher compression materials because they experience extreme side load and shock loads. However, most applications do very well with filled Teflon materials.
- Bearings come solid or split. If designed properly, split bearings provide equivalent support, while improving installation options with no compromise in performance.
Solid bearings, or bushings, are convenient when installing on the outboard side of a rod groove. Split bearings are essential when installing in a piston groove designed to function internally in a system. - Nylon or composite bearings are typically cut to allow for installation because of their stiffness. However, a Teflon bushing can be made into a ring, or cut from a roll of sliced strip.
- The only time a bushing needs to be cut from a ring is if insulation does not allow the strip to be deformed for a clean install. Strip installation allows for variability in length, lower manufacturing costs, and the product can generally be acquired off the shelf.
Materials for Polymer Bearing Configurations
When selecting materials, we must consider the maximum load, the speed of the system, and whether there is any lubrication in the system.
The load (or pressure over area) that the bearing will see is the first consideration. This dictates which materials will be the best fit.
It’s important to use a material that has a minimum compressive strength rating so that it will not fail under the highest loading condition. The industry standard is to employ a safety factor so that the bearing is specified to be used well beyond its design limit.
Teflon should be your first consideration due to cost and ease of installation. Nylon or composites will provide much higher load rating, but the cost and installation need to be considered.
Teflon and composites provide service without lubrication, and the composites provide excellent service in aqueous solutions. Bushings are typically used in medium to slow reciprocating service. Rotary creates challenges that may or may not work depending on the design of the bushing.
There are many series of injection molded nylon bushings. However, nylon in low-lubrication or high-loading may create high-friction, and can be noisy. Nylon, as a low-cost bushing, can be used in some high load situations.
A final consideration before going into large scale production is the cost of talking a bearing design into high production. Some bearing materials are expensive and can only be processed by machining, which limits the cost reduction scenarios at high volumes.
The Eclipse Advantage
Materials such as filled-PTFE or thermoplastics that can be molded offer cost competitive solutions for high-production applications. Eclipse provides bearings in everything from low-quantity applications, such as bridges and dams, to mid-quantity applications in aerospace.
Eclipse Engineering has experience in bearing selections based on your exact needs. Our engineers will consider all the application variables to optimize the bearing design. We also utilize all the materials mentioned and many other materials such as PEEK , UHMW , and Torlon , just to name a few.
For all your polymer needs in bearings, seals, and shapes, we’re happy to develop a solution for your application. Contact us today »
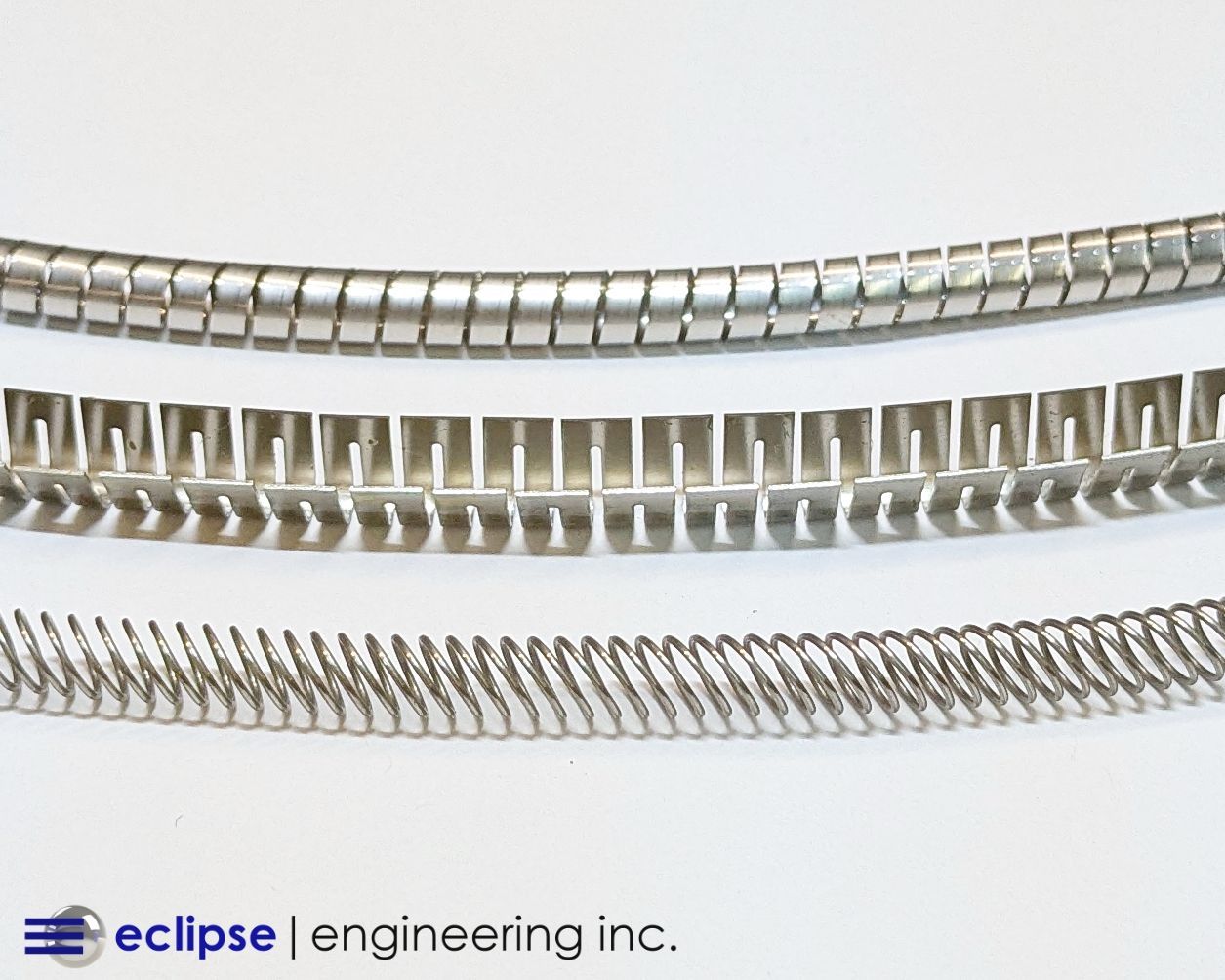