The Right Fillers for Optimum PTFE Performance
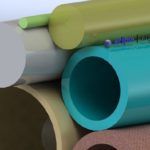
Polytetrafluoroethylene (PTFE) resin is a highly effective material for seal consumers due to its extremely low friction, high heat tolerance and chemical inertness.
With the right additives, PTFE resin can perform even better in terms of strength, thermal performance, chemical resistance and abrasion.
However, there are a few design considerations when using PTFE resin, particularly when combined with glass fiber and bronze.
A Quick Intro to PTFE: A Breakthrough Material
A common household form of PTFE is Teflon, which you’ll recognize as the slippery plastic used in non-stick frypans.
PTFE was discovered in the 1930s as an accidental byproduct in chlorofluorocarbon refrigerant production. It’s a synthetic compound consisting wholly of carbon and fluorine — a fluorocarbon.
PTFE is hydrophobic, so doesn’t get wet due to the high electronegativity of fluorine. It’s also chemically non-reactive, mainly because of the ‘independent’ strength of the carbon–fluorine bonds. This suits the resin well for reactive and corrosive chemical environments.
Where it is used as a lubricant or seal, PTFE has the huge benefits of reducing friction, wear and energy consumption of machinery.
Making a Great Material Even Better
After extensive experimentation and time-tested performance, the following additives/fillers have come to be strategically used to enhance PTFE performance:
Glass Fiber (typically 5–40%)
Improvements:
- Creep resistance
- Compressive strength
- Pressure tolerance
- Chemical compatibility/inertness (except for strong alkalis and hydrofluoric acid)
- Wear resistance and durability
- Similar friction to virgin PTFE
There are a couple of cons to glass fiber, including abrasion on mating parts and discoloration of finished parts.
Ideal for:
- Piston rings
- Backup rings
Molybdenum Disulfide (MoS2) (typically low %)
Improvements:
- Hardness and stiffness
- Friction
- Lubrication
- Wear resistance
- Chemically unreactive (except with oxidizing acids)
- Best when combined with glass and bronze
Ideal for:
- Dynamic seals
Carbon powder (typically 5–15%)
Improvements:
- Hardness
- Compressive strength
- Deformation resistance
- Thermal conductivity
- Permeability
- Abrasion reduction
- Wear resistance and reduced friction when combined with graphite
- Antistatic (electrically conductive)
Ideal for:
- Rotary seals
- Sliding applications
- Piston rings (with graphite)
Carbon Fiber
Improvements:
- Creep resistance
- Chemical inertness
- Lightness
- Wear resistance
- Abrasion reduction
Ideal for:
- Bearings
- Seal rings e.g. water pumps and shock absorbers
Graphite (typically 5–15%)
Improvements:
- Friction
- Lubricity
- Wear resistance
- Reduced wear against soft metals
- High load-carrying capability in high-speed contact applications
- Chemically inert
- Great combined with glass and carbon
Ideal for:
- Pumps
Bronze (typically 40–60%)
Improvements:
- Wear resistance
- Thermal conductivity
- Creep resistance
- Pressure tolerance
Disadvantages:
- Chemical reaction
- Oxidizes
Ideal for:
- Hydraulic systems
- Master cylinders
- Drug manufacture seals
- Not for electrical or corrosive applications
Pigments
Improvements:
- Color coding of seals
- No performance change to pure PTFE
Put to Profitable Use
PTFE seals , with their exceptional performance, are used for a myriad of applications, including:
- Motors
- Gearboxes
- Pumps
- Bearings
- Compressors
- Extruders
- Valves
- Blowers
- Spindles
- Mixers
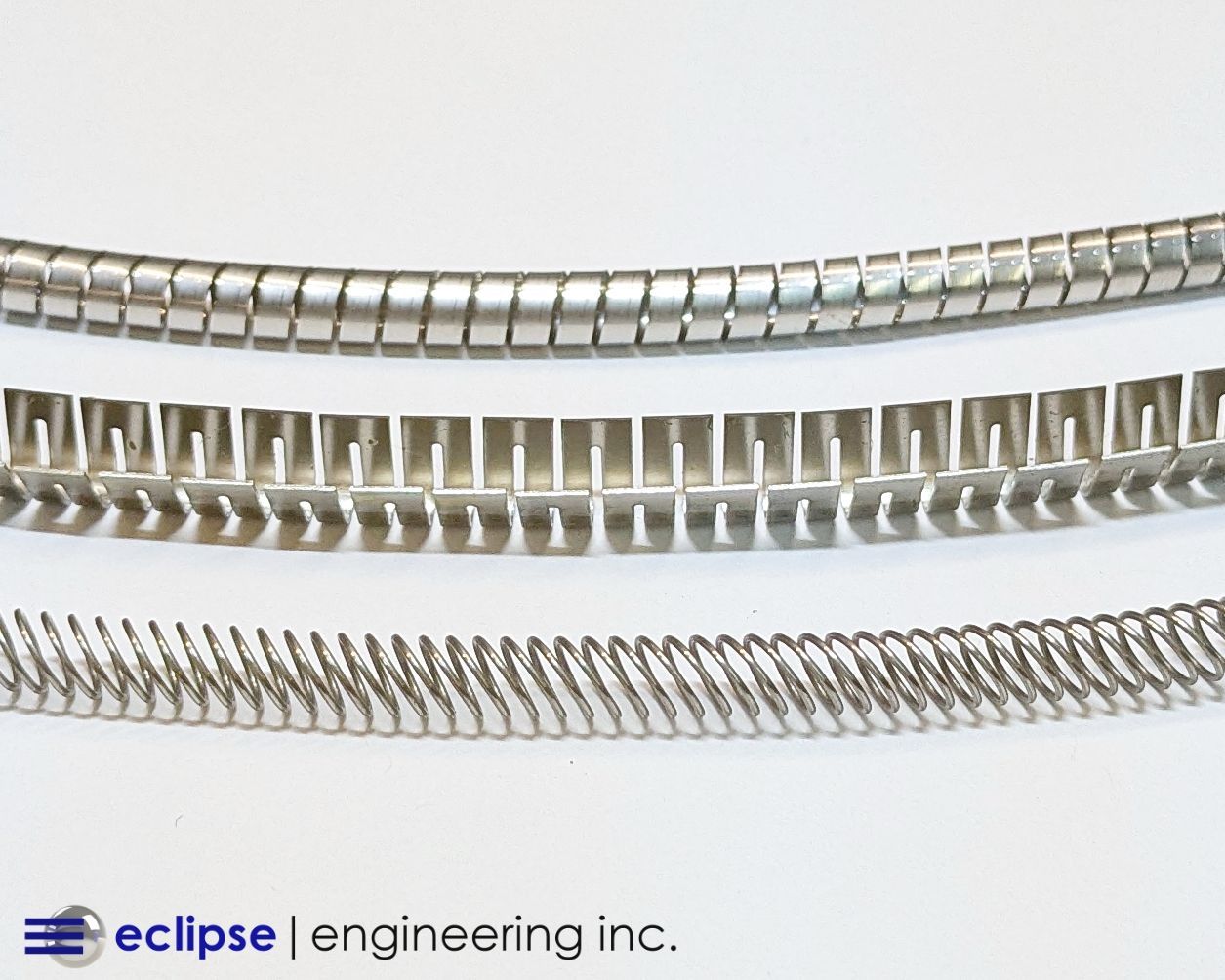