AS9100 / ISO9001Certification!
Back in August 2013 we began the journey to gain AS9100 and ISO9001Certification . Up to this point, our size had allowed us to manage our organization by walking around and seeing what was occurring on the shop floor in real time. With the continual growth we were experiencing, it had become difficult to continue managing projects without guidelines in place. As an organization always looking to bolster growth and never stand still, we formed a management team and began the journey to become ISO/AS approved in the hopes that it could further strengthen our company. The process guided us in creating systems to run and organize our business in a more efficient manner. This process became instrumental in improving literally every aspect of our business, further allowing us to become more efficient while reducing or eliminating the number of errors in processing orders. Although it was a tremendous task upfront, documenting every process experienced in our building has allowed us to perform these operations more effectively when running jobs multiple times. This has also taken the guesswork out of our order entry and allowed those staff members to better utilize their time focused on contact with our customers instead of needing a detailed grasp of our production and how to make your job. With a process built for its attention to detail, minor changes to a product now require far less time to schedule and plan, at the same time reducing or eliminating errors that occurred due to oversight.
On November 4, 2014 we had our final audit, and subsequently on January 7 2015 received final certification and approval for ISO9001:2008 and AS9100C. The same day we received our certification, we were audited by an industrial/aerospace customer who gave us glowing reviews and opportunities for new business that came to light specifically because of our Quality Management System.
Congratulations to all the hard working folks at Eclipse that helped to open these doors.
Cliff Goldstein
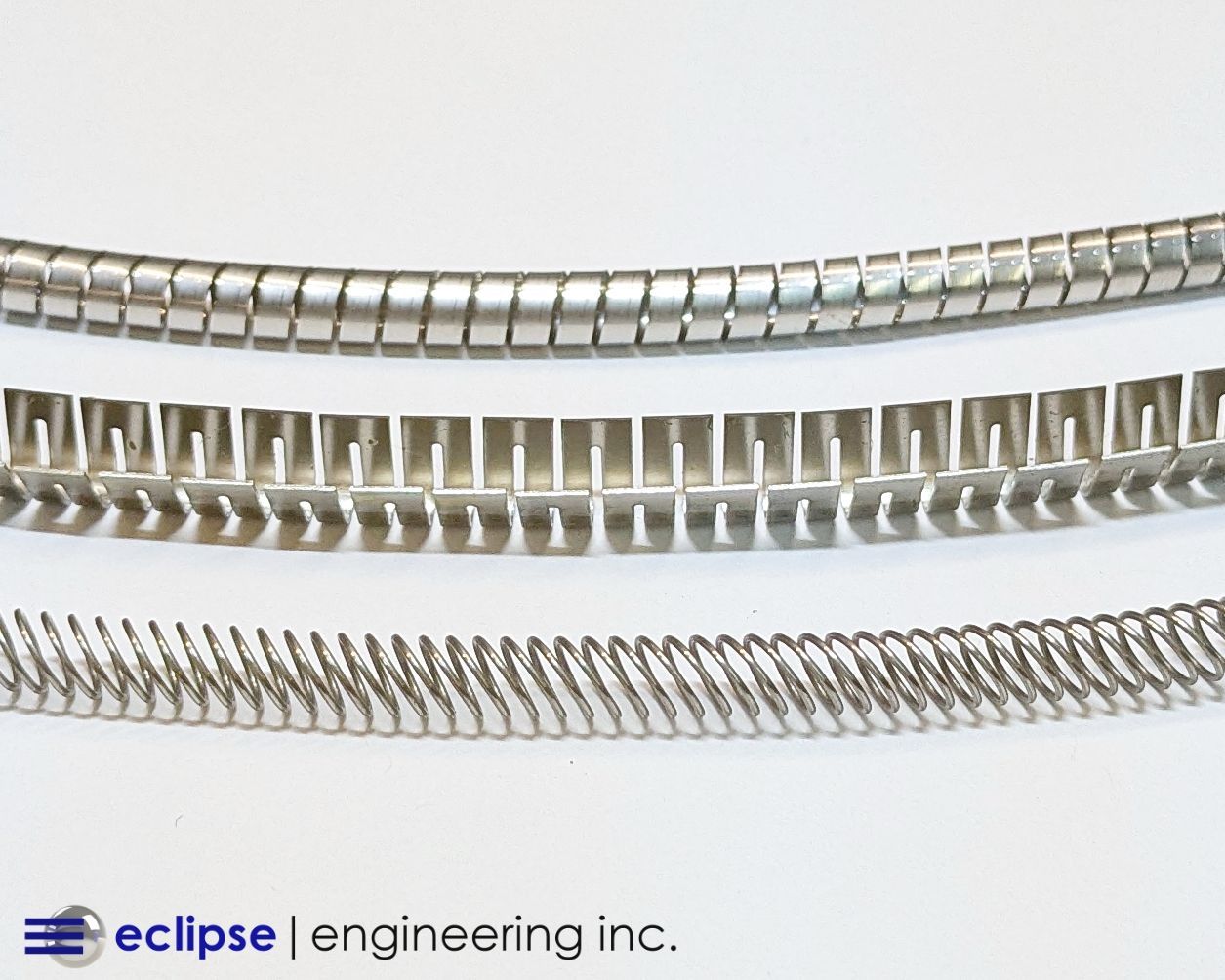