Seals for all Seasons: Perfluoroelastomers
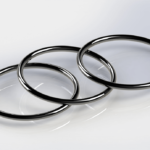
In the sealing industry, we follow a basic design scheme to help us determine what the best seal for the application will be. We’ve learned that the first place to start is the basic O-ring.
The O-ring’s low cost and ease of installation makes it our number one choice. And while we have a variety of materials and cross sections, the basic O-ring often delivers the best bang for your buck.
But what happens when the required environment is calling for an O-ring, but the fluid or temperature exceeds what the standard O-Ring can provide?
Perfluoroelastomers may solve these difficult sealing needs where other solutions can’t. Perfluoro’s give the seal-ability of an O-ring, combined with the temperature and fluid resistance of Teflon.
A few of the industries that have taken advantage of these rare characteristics are the semiconductor , oil , chemical, and pharmaceutical markets. These industries require seals to work in extreme chemical and temperature environments, and not allow the introduction of the seal materials to enter the fluid stream.
There are several different ways to accomplish this, but the first thing we must consider the operating characteristics.
When to Use Perfluoroelastomers
For static seals where no relative motion exists, the use of perfluoroelastomers, or FFKM rubber, is a first consideration.
Perfluoroelastomer parts have excellent chemical and thermal stability, and have been specially formulated and processed to meet the unique requirements of these varying industries. Depending on the application, standard O-ring grooves will accept these molded O-rings and custom seals using a series of specialty compounded elastomers.
For example, in the semiconductor industry, ultrapure compounds have been developed with the express purpose of not contaminating the fluid stream.
For dynamic seal applications where wear and friction are a concern, in these same operating conditions, Eclipse designs and manufactures spring and rubber energized seals made from materials such as Polytetrafluoroethylene PTFE, (Teflon®) or Ultra High Molecular Weight Polyethylene.
In combination, we may use a Perfluoroelastomer on the static side of the seal, or as an energizer where a metal spring could contaminate the fluid stream.
These seals are typically machined cross sections and energized by metallic springs or rubber elastomers. PTFE is essentially inert to almost any chemical, and a metal spring can be selected from the accepted metals that are used in other areas of the equipment, typically a 300-series spring steel.
If the seal is rubber energized, the use of a Perfluoroelastomer provides excellent chemical and temperature compatibility while allowing for the performance of Teflon or UHMW for the dynamic member.
The use of these polymers allows for dynamic motion to occur without abrading the mating surface. These polymers can resist contamination in the fluid stream, while keeping friction to a minimum and operating in varying temperatures to satisfy the application.
Dynamic seals can operate in reciprocating, oscillatory and rotary motion. Due to their relative coefficient of friction compared to elastomeric seals, these polymers can dramatically reduce the amount of heat induced by the dynamic motion into the system.
These materials are not limited to round shapes. They can be machined into virtually any profile to accommodate the application.
Temperature Limits of Perfluoroelastomers
When pressures exceed the mechanical strength of these standard polymers, Eclipse Engineering can build backup ring combinations to handle pressures exceeding 100K PSI.
When pressures go negative or vacuum, we’re capable of building sealing systems that are capable of sealing to extreme vacuum, and continue to function as dynamic seals. This is accomplished with our super finish process for polymers, in combination with the application hardware and finishing of the mating surface for the dynamic application.
For boundary seals in electronic enclosures, we can design seals or protection devices to keep the outside environment separated from the environment within the electronic device.
We have designed polymer enclosure seals that operate in severe glove box environments. We also build electronic enclosures to insure product remains within the enclosure.
When designing with the harshest of chemicals and operating at temperatures that can swing from -400F to in excess of 500F, the use of a polymers such as PTFE and elastomeric materials such as FFKM provide for long-term solutions that will keep your production equipment up and running longer, and your PM cycles to a minimum. This helps reduces overall downtime, improve run time, and ultimately makes your operation more profitable.
Eclipse Engineering has been supplying Perfluoroelastomers like Kalrez in the market place for 20 years, and has the experience to solve your sealing needs. Contact us today with any of your specialty sealing needs »
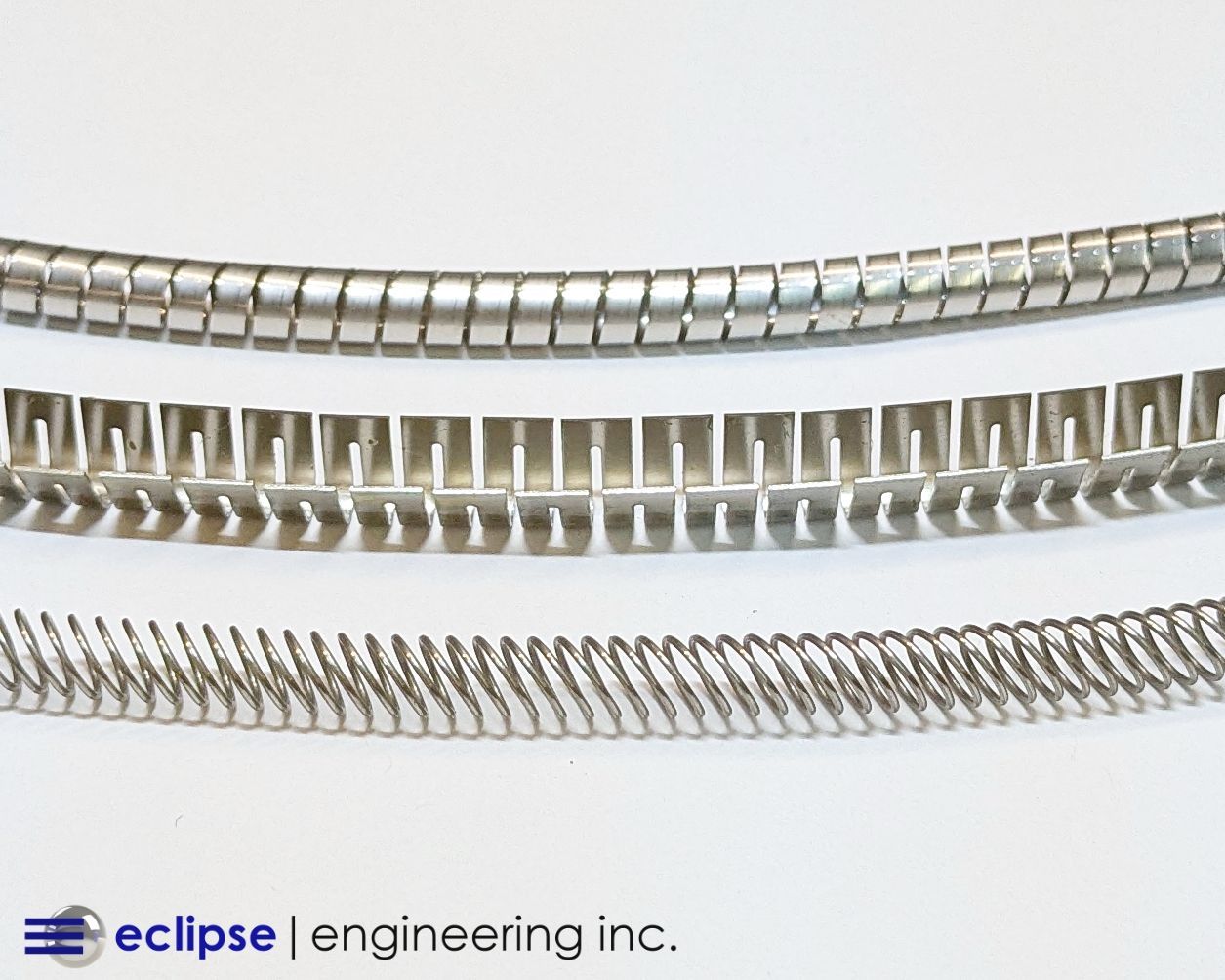